Predictive Maintenance in Manufacturing
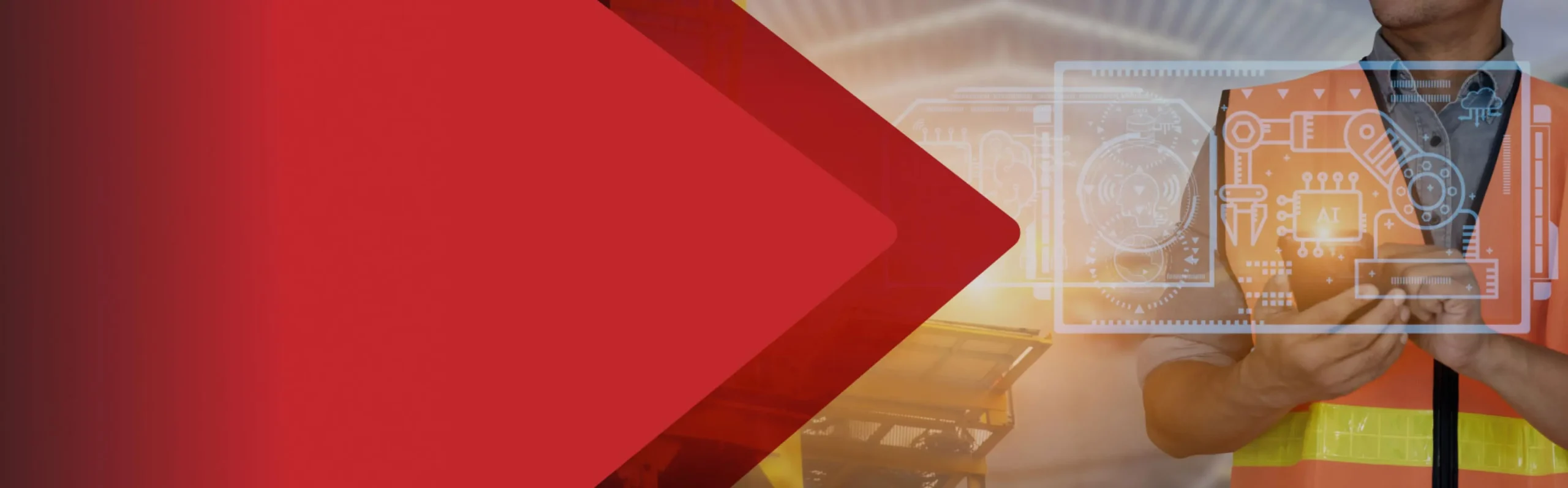
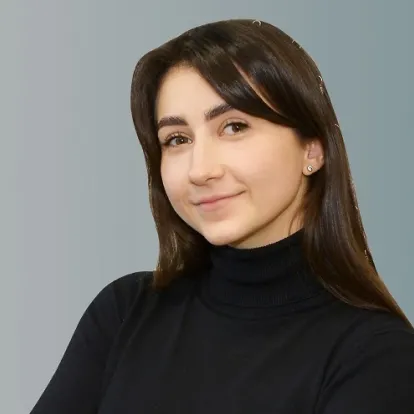
Predictive maintenance (PdM) is a proactive approach that heavily relies on data and hidden patterns. It helps detect possible malfunctions or equipment failure in the early stages, significantly reducing downtime and repair costs.
It helps remove the guesswork and visual inspections out of your workflows but to get data-baked insights with equipment failure forecasts and root cause analysis.
Industrial predictive maintenance in action
Let’s take a deeper look at how PdM works in manufacturing by revising the core components, workflows, and use cases.
In summary, predictive maintenance is enabled by collecting data from sensors installed near the equipment. The data is then transferred to the main server and processed to assess a machine’s health and predict a failure. The core stages of the PdM workflows are as follows.
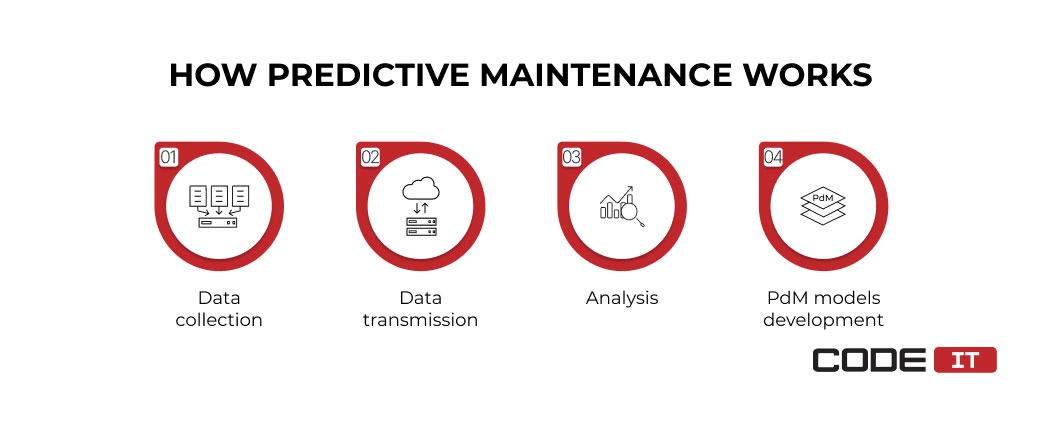
1. Data Collection
Sensors and IoT devices are installed on equipment to collect various data, including vibration, temperature, pressure, humidity, noise, and more. Any type of machine health and environment condition information can be collected. All the sensors collect and transit data in real time. Also, they may be capable of storing historical data and sending it upon request from the main server.
2. Data Transmission
Data is transferred to the main server via a wired or wireless network. Optimization algorithms may be developed to reduce bandwidth. For instance, software engineers can implement an algorithm that doesn’t share repeating values but ensures that a connection remains active.
Moreover, the implementation of edge servers helps reduce the load on the main server. Collected data is being pre-processed on computing units installed near the equipment. Hence, only transformed and condensed data is sent to the main cloud or on-premise server.
3. Analysis
Large volumes of data are analyzed using advanced tools and algorithms. First, algorithms need to check and validate the received data. Then, the datasets need to be filtered, cleansed and transformed.
Advanced algorithms include the implication of machine learning models and artificial intelligence to detect hidden patterns behind values received from sensors. The technology helps identify patterns, detect trends, and spot anomalies that can indicate a possible failure.
4. Predictive Models Development
PdM models identify what equipment is more likely to fail and when. The ability to predict the time of a failure is useful for scheduling maintenance to achieve the minimum downtime. The capability of AI to detect hidden correlations between datasets and the technology can help analyze the root causes of problems.
The results of analysis comprises reports and visualized data for rapid assessment. Also, the software sends alerts if anomalies or signs of possible failure are detected.
Ready to implement predictive maintenance?
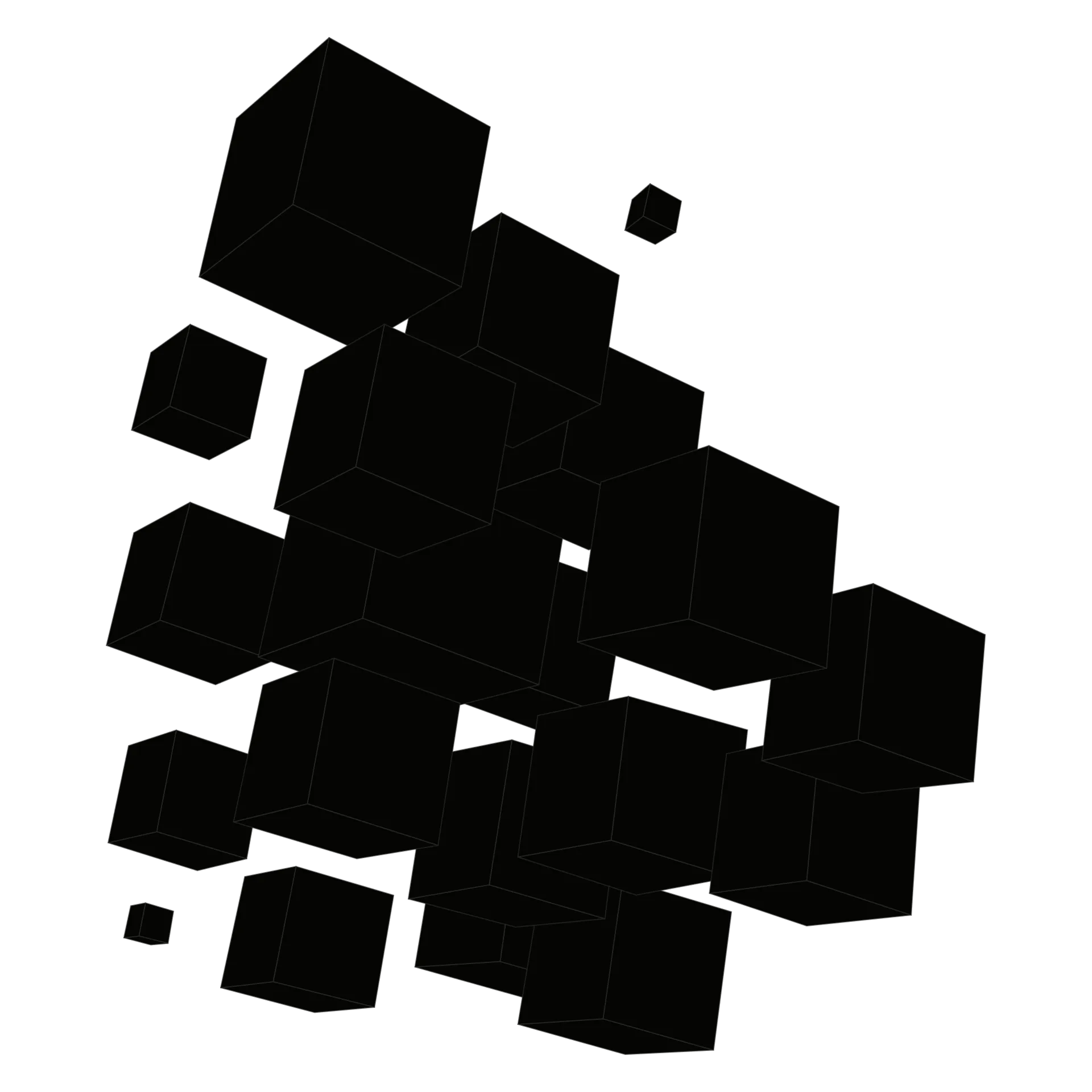
Business First
Code Next
Let’s talk
Corrective vs predictive maintenance in manufacturing
Let’s explore the real case study that unveils the real effectiveness of PdM compared to corrective maintenance.
The gearbox on the limestone transport belt conveyor has been functioning without any issues for four years. However, the system that analyzes data received from the vibration sensor installed on the equipment began noticing the continuous increase in the vibration. Eventually, it increased from 2 mm/sec to 14 mm/sec within three weeks. Also, the abnormal noise has appeared.
Corrective Activities
On-site technicians have conducted a visual inspection of the gearbox, but no issues were found. In order to fix the issues with abnormal vibration and noise, a lot of gearbox maintenance activities were conducted:
- Oil replacement
- Air duct and filter cleaning
- Isolated motor testing
- Components alignment check
- Rubber elements replacement
None of these activities helped detect the root cause of the anomalies and fix the issue. Moreover, the absence of a spare gearbox increases the risk of severe downtime if a failure occurs.
PdM Activities
An external condition monitoring analyzer has been installed to assess the increased vibrations and analyze root causes. The vibration analysis revealed that the problem was most likely with the drive drum bearings rather than the gearbox or the motor.
A closer examination revealed that the bearing on the non-drive side was worn, with a too large clearance. Replacing this faulty bearing restored normal operation and significantly reduced vibrations.
PdM Outcome
The deep analysis of the gearbox’s vibration spectrum has helped the company avoid critical downtimes by identifying and addressing technical issues in the early stages. The core positive outcomes of applying predictive maintenance included the following:
- Preserved gearbox (the approximate cost of new gearbox purchase and installation is $27,000).
- Avoided unexpected downtime caused by the gearbox failure and replacement (approximately $111,360 saved in avoided production losses).
- No safety incidents occurres
Applications of predictive maintenance in manufacturing
Predictive maintenance use cases in manufacturing include continuous machine health monitoring, downtime management, and more. Let’s thoroughly review the most common equipment manufacturers use and how PdM helps monitor its condition.
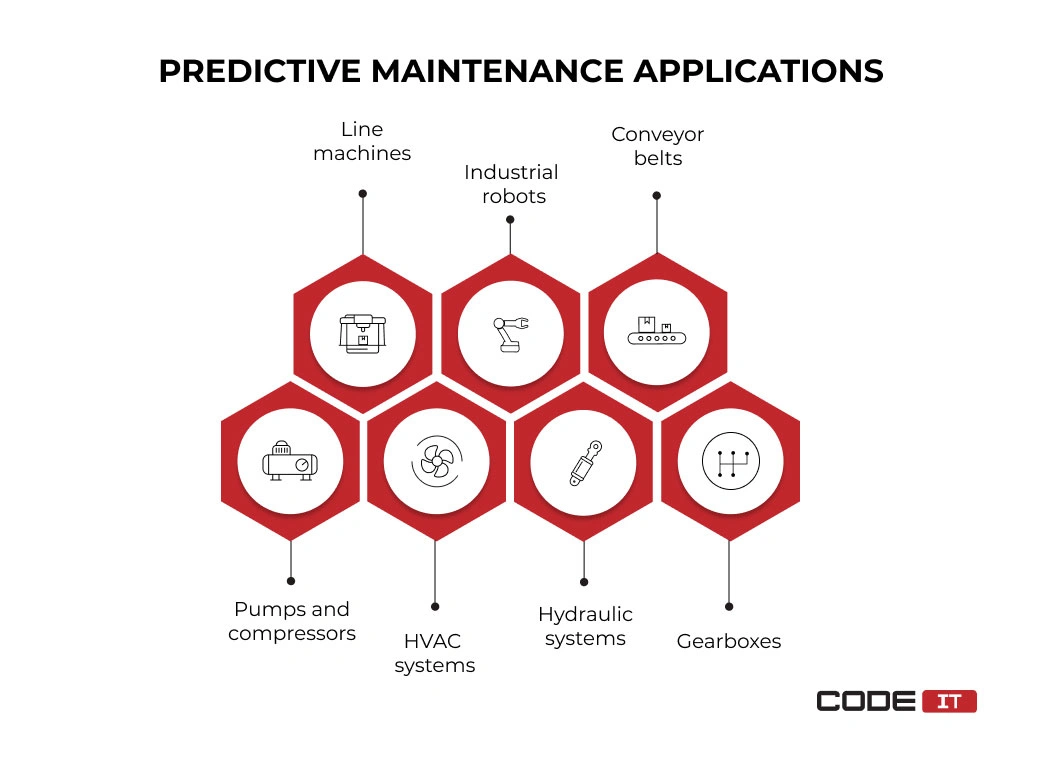
1. Line Machines
Basic sensors that continuously monitor vibrations, noise, temperature, and other data help detect possible anomalies at early stages. Technicians or advanced sensor data analysis tools need to investigate them further. Smart sensors help you get instant alerts when your production line machines begin acting differently from their usual behavior.
2. Industrial Robots
Joint sensors and data received as motor feedback help meticulously monitor the health of automated actuators and robotic arms. The analysis of the data collected helps detect unusual movements, excessive torque, and possible failures in picking items. Hence, technicians get full visibility into the motors, understanding when they are likely to fail or if any external factors affect the movement of robotic arms.
3. Conveyor Belts
The installation of vibration and acoustic sensors helps monitor the health of conveyor belts. Analyzing this data helps detect misalignments and worn-out components that may require replacement. Temperature sensors can also detect overheating in motors, notifying technicians that motors require servicing.
4. Pumps and Compressors
Vibration sensors are crucial for monitoring the health of pumps and compressors as they can help detect imbalances. Also, the installation of flow sensors help detect pressure fluctuations or leakages.
5. HVAC Systems
Temperature, humidity, and other sensors help monitor HVAC systems’ efficiency. Moreover, analyzing energy consumption data helps analyze the efficiency of cooling and heating systems. A drop in HVAC efficiency may be a sign of worn-out components that need attention. The additional installation of flow sensors is useful for detecting possible air duct or filter blockages.
6. Hydraulic Systems
The monitoring of hydraulic systems is usually enabled by pressure sensors, fluid level, and temperature sensors. The data received from the sensors helps identify possible leakages and pressure drops. The PdM of hydraulic systems helps predict seal wear, fluid degradation, or valve failures.
7. Gearboxes
The continuous monitoring of gearbox vibration helps identify worn-out details, gearbox misalignments, or lack of lubrication. The thorough analysis of all the changes captured by sensors helps predict when a gearbox is likely to fail and allocate the root cause of detected anomalies.
Enable continuous equipment monitoring
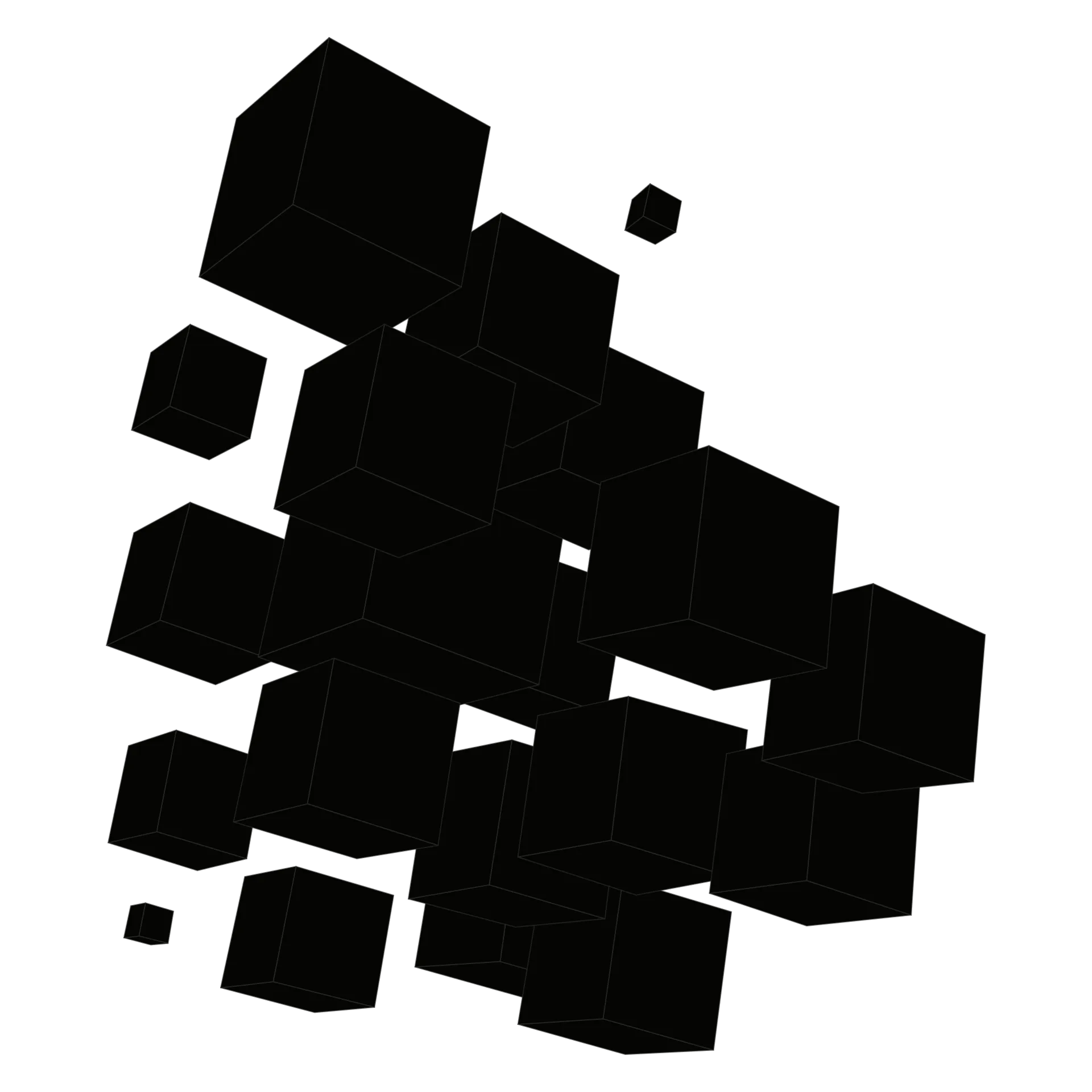
Business First
Code Next
Let’s talk
Evolution of predictive maintenance in manufacturing
The core three levels of maintenance in the manufacturing industry are: reactive, preventive, and predictive. Understand the PdM by tracing its development through the core stages.
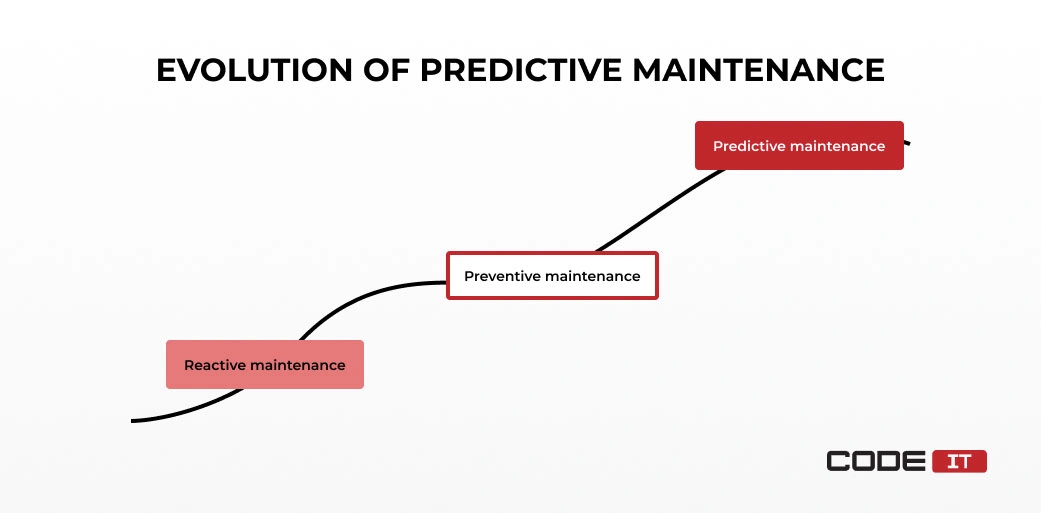
Stage 1: Reactive maintenance happens only when a machine fails. The cause of breakdown is investigated and broken components are replaced. It causes unplanned downtime and increased spendings.
Stage 2: Preventive maintenance relies on planned inspections and activities to keep the equipment in good condition. Significant signs of failure may stay undetected until a failure occurs.
Stage 3: Predictive maintenance collects a lot of data from various sources. The data is analyzed and predictive models are developed, forecasting the failure of equipment and providing insights into root causes of machine health issues.
The benefits and drawbacks of each maintenance approach are as follows:
Benefits | Drawbacks | |
---|---|---|
Reactive | No systems to implement No planned downtime | Unplanned downtime and maintenance expenses Time-consuming issues identification and part replacement No confidence in equipment health |
Preventive | Improved reliability of line machines Reduced risk of unplanned downtime and machine failure Reduced downtime-related financial losses | Regular downtime to inspect machines, even if they are in perfect condition A risk of machine failure because some problems may remain undetected |
Predictive | Optimized maintenance costs Planned downtime (only when signs of failure are detected) Extended lifespan of equipment Insights into root causes of issues | A complex PdM system needs to be established The installation of sensors and an IoT network is required |
Benefits of predictive maintenance
Let’s take a deeper dive into the benefits of predictive maintenance in manufacturing and how it helps optimize costs and cut costs.
Reduced Downtime
Predictive maintenance in manufacturing helps detect technical issues with production line equipment at early stages. Consequently, machine inspection and replacement of worn-out components can be planned, avoiding major equipment failures and production disruptions.
Moreover, the continuous monitoring of equipment health eliminates the need for scheduled downtime for planned equipment inspection. Manufacturers need to halt the production only when the signs of failing equipment are detected.
Lower Maintenance Costs
PdM practices help detect equipment issues at early stages, saving large components of machines from degrading. When a large mechanism fails, it usually requires urgent replacement that blows up maintenance & repair budgets. Moreover, the equipment is serviced only when the signs of possible failure are identified, saving costs on tech teams.
The PdM tools help analyze problems deeply, identify root causes of failure, and optimize the performance of service teams. Hence, they don’t need to inspect each machine component separately or run various maintenance activities, like oil changes, filter replacement, alignment checks, and others, expecting the issue to be resolved.
By identifying the exact condition of machinery through real-time monitoring, companies avoid over-maintenance and reduce the likelihood of costly, unplanned fixes.
Improved Efficiency
Production processes run more smoothly when equipment is maintained at the optimum performance level. The continuous monitoring of equipment helps ensure that machines always operate at their best parameters, reducing the chances of performance degradation over time.
When equipment is perfectly aligned and motor windings are not degraded, manufacturers can achieve optimized energy efficiency and higher-quality output.
Extended Equipment Lifespan
Access to actual data about production line machine health and manufacturing predictive maintenance activities promotes equipment’s extended lifespan. The predictive maintenance use cases in manufacturing highlight the approach’s help preserve existing equipment, improving the overall ROI.
Improved Safety
Unforeseen equipment failures put workers at risk of injuries. The condition-based monitoring (CBM) of production line equipment helps ensure machines are in proper working condition, reducing the risk of significant safety risks. The approach helps mitigate these risks by predicting when equipment is likely to fail and ensuring timely intervention.
Disruptions Prevention
The elimination of a need to run scheduled maintenance sessions helps run uninterrupted production. By preventing unexpected breakdowns and production halts, companies can meet their production targets and deliver on time, improving customer satisfaction and maintaining business continuity. This proactive approach also supports better planning and resource allocation across the organization.
Technologies and solutions
Industrial predictive maintenance is implemented by integrating interconnected sensors that continuously gather information about production line machines and send them to the main server for further analysis.
The technologies that enable predictive maintenance in manufacturing industry are:
1.1 Machine Condition Monitoring Systems
The digital solution is installed on a server. It collects and analyzes all the data gathered from production machines. Condition-based monitoring (CBM) enables technicians to quickly access all the available information about shop-floor machines’ conditions using a single solution.
Moreover, the systems can visualize data and prepare reports, highlighting anomalies detected. All the records are stored for further analysis, comparison, or trend identification.
1.2 Industrial Internet of Things (IIoT)
The IIoT implementation helps create smart factories by connecting all devices with a network of sensors, cloud computing, and analytics platforms, providing a comprehensive view of a smart factory. The connected devices collect and transfer data in real-time, providing manufacturers with comprehensive insights.
Moreover, the usage of programmable logic controllers (PLCs) helps manufacturers to control equipment and issue commands using a single predictive maintenance software. The capabilities of IIoT can be further enhanced by integrating edge computing. The term describes the usage of intermediate computing nodes installed near equipment. They pre-process the collected data, reducing the load on the network and main server.
1.3 Machine Learning and Artificial Intelligence
Rule-based is the common PdM approach that is easy to implement. It heavily relies on a defined algorithm (if this, then that). For instance, if the temperature of a machine reaches the defined values, the system halts the production and sends an alert to the technicians team.
However, the implication of AI enables the opportunity to analyze large amounts of data to detect trends and define root causes. Moreover, the technology is capable of detecting hidden patterns that may indicate future failures. The implementation of AI-driven PdM requires extensive technical expertise and large amounts of data to train ML models.
1.4 Digital Twin
The digital twin technology relies on using shop floor data for virtually simulating production activities in real-world conditions. Digital twins provide a dynamic, real-time model of machinery that helps manufacturers monitor performance, predict issues, and test maintenance scenarios before applying them to the physical equipment.
Industrial IoT for Manufacturing
Also, the tech teams can manually examine the components of machines without halting manufacturing processes. The foremost tools used by technicians are:
2.1 Infrared Analyzer
The device is used for remote thermal imaging, helping understand what areas experience excessive heat. The identification of hot spots helps detect possible technica issues such as a failing bearing in a motor.
The infrared analyzer is useful for noninvasive inspections by pinpointing overheating areas that need the technical team’s thorough attention. Overheating may signify component misalignment, clogged air ducts, worn-out bearings, failed electrical connections, and more.
2.2 Vibration Analyzer
This is one of the most popular PdM tools that records and analyzes vibrations. It can detect anomalies by comparing the records to the historical data. The thorough inspection of vibration helps detect any irregularities or misalignment of components. Technicians use the tool for allocating the root causes of problems to better understand what components are worn out and are about to fail.
2.3 Dynamic Analyzer
The tool helps assess the health of motors and other electrical equipment by analyzing electrical signatures. It thoroughly analyzes current and voltage waveforms to detect problems like worn-out motor bearings, rotor bar issues, misalignment, or electrical unbalance. The tool enables in-depth diagnostics without the need to disassemble motors and other electrical components.
2.4 Static Analyzer
This tool applies probing signals to analyze motor windings and insulation. The low-frequency signals issued by the device test for issues such as insulation degradation, short circuits, and phase imbalances. It helps technicians to rapidly inspect large numbers of motors to monitor their health and define the ones with degrading components that lead to decreased performance and increased energy consumption.
2.5 Ultrasound Analyzer
The device captures high-frequency sound waves produced by the equipment. It is usually applied to detect minor early-stage mechanical failures that cannot be identified during visual inspections run by technicians.
It is capable of detecting leaks in compressed air systems, gas lines, or hydraulic systems that are not visible or can’t be heard. Moreover, ultrasound analysis can record historical data to stop any changes or anomalies that can signify early signs of mechanical issues.
2.6 Oil Analysis
Oil change is the basic equipment maintenance practice that is applied when an anomaly is detected by a problem’s root cause is not identified. The oil analysis helps monitor the condition of lubricants to assess equipment health.
Technicians are required to take a sample of oil or other lubricant and test it for contamination, metal particles, chemical degradation, and more. The analysis of oil can signify internal wear and tear, helping predict when maintenance is needed. The regular oil analysis is required for monitoring the health of engines, gearboxes, and hydraulic equipment.
2.7 Laser Alignment Tool
It enables the opportunity to ensure perfect alignment of equipment. The tools emit laser beams to measure the alignment of machine parts. Correct alignment helps prevent issues such as premature bearing failure and excessive vibration, improving the manufacturing efficiency and equipment lifespan.
2.8 Acoustic Emission Sensor
The continuous analysis of sound helps automatically detect the sound of cracks or other possible signs of issues that happen only once. All the information is recorded and transferred to the main server so that technicians can access all the data on a dashboard. Using acoustic emission sensors to identify issues before they become critical helps prevent catastrophic failures and extend the service life of the equipment.
Hire PdM implementation experts
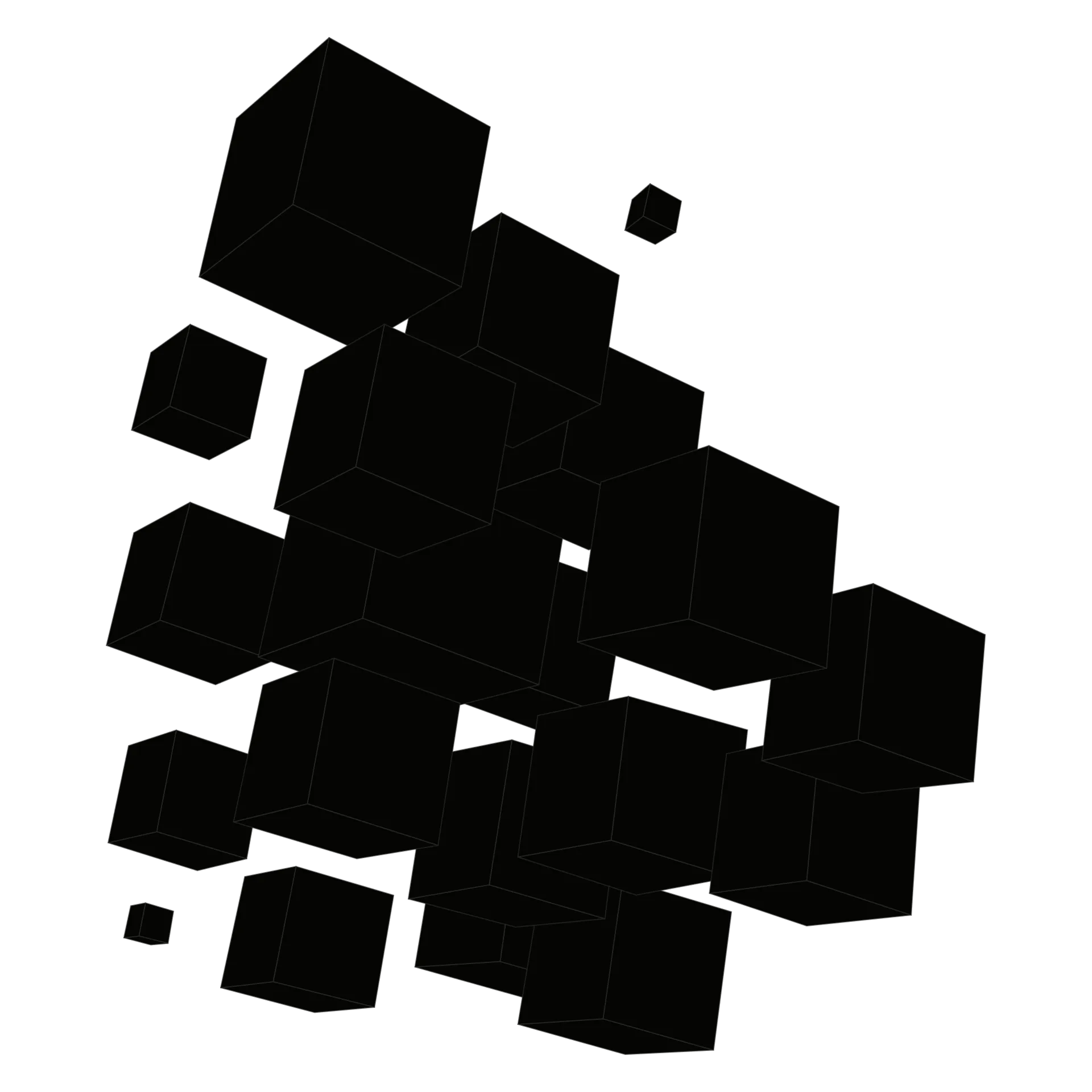
Business First
Code Next
Let’s talk
Industrial predictive maintenance challenges
The implementation of predictive analytics in manufacturing needs stakeholders to resolve a lot of issues. However, the most common challenges include the following.
1. High Investment Cost
Manufacturers need to pay high upfront costs to purchase all the required sensors, PdM devices, Industrial Internet of Things (IIoT) components, etc. Moreover, they need to hire an experienced vendor to install and configure all the hardware and software. Additionally, there may be costs related to upgrading existing infrastructure to ensure compatibility with PdM tools.
2. Lack of Skills and Expertise
Predictive maintenance in manufacturing heavily relies on top-tier technical expertise, like data analytics, IoT, and machine learning. It may be challenging to scout and hire specialists who have the required expertise and hands-on experience. Moreover, in-house maintenance teams also require training and guidance to run PdM operations smoothly.
3. Complicated Data Management
AI predictive maintenance manufacturing generates large amounts of data that need to be analyzed to identify anomalies and forecast upcoming equipment failures. It’s required to ensure the proper data is collected and that it contains no bias to get accurate insights. Moreover, infrastructure is required to store and process all the data. Poor data management can lead to incorrect equipment failure predictions.
4. Machine Learning Model Creation
Machine learning models need to be created and trained so that they can analyze data and generate actionable insights. The process requires top-tier technical expertise and large volumes of data for model training and testing purposes. Moreover, these models must be continuously trained and updated as new data is collected.
5. Change Management
The implementation of predictive maintenance in manufacturing needs manufacturers to implement a lot of changes, including new workflows, updated instructions, and more. In-house teams frequently resist implementing new technologies and grasping new skills as they already have tried-and-tested workflows.
Switching from reactive to predictive maintenance in manufacturing
The process of implementing predictive maintenance in manufacturing implies a lot of custom stages that are defined, considering the existing infrastructure and digitalization level.
The foremost steps to follow to enable PdM in manufacturing are as follows:
Step 1: Assess Existing Practices
For starters, you need to thoroughly examine the existing equipment condition-based maintenance practices and outline all the workflows. Hence, you can understand what processes need to be improved and how they can be enhanced with AI predictive maintenance manufacturing.
Moreover, it’s crucial to understand the effectiveness of the existing maintenance practices to assess the outcomes of the PdM implementation. Evaluate historical maintenance data, failure rates, production uptime, and associated costs to understand the gaps in the existing system.
Step 2: Set Goals
Understand what measurable outcomes you have to achieve by implementing predictive maintenance in manufacturing. The common goals to set may include:
- Reduced downtime costs
define the current cost of downtime caused by planned inspection and unforeseen technical failures.
- Lowered maintenance costs
identify specific areas where predictive maintenance can reduce unnecessary repairs or part replacements.
- Increased equipment lifespan
create the list of the expected vs real equipment lifespan that may be affected by the lack of early problem identification.
- Reduce energy consumption
record the existing energy consumption and set the goals to achieve by replacing worn-out equipment.
Step 3: Implement Hardware and Software
Pick the most required equipment to install PdM software. Also, it’s recommended to implement data visualization tools that enable the opportunity to create custom dashboards to access PdM data in a convenient-to-consume way.
The main stages of PdM hardware and software implementation are:
- Sensor installation
mount and configure vibration, temperature, pressure, or other relevant sensors to monitor the performance of your machines.
- IoT platform implementation
create a network for sharing data and connect sensors to an IoT platform to enable real-time data collection and analysis.
- Data management
configure an on-premise or cloud server so that the collected data is stored securely and accessible for historical analysis.
- PdM data analysis
implement rule-based or AI predictive maintenance manufacturing to continuously monitor equipment health, identify early warning of equipment failures, and detect hidden patterns.
Step 4: Train Maintenance Team
It’s crucial to train your team of technicians to ensure smooth transition from reactive to manufacturing predictive maintenance. Conduct a workshop, explaining how to apply new tools for running predictive maintenance in manufacturing.
Also, it’s recommended to prepare thorough instructions for your team of technicians so that they can follow clear guidelines, ensuring no crucial activities are missed. Teach technicians how to read and analyze predictive maintenance data, including interpreting trends and determining when maintenance should be scheduled.
Step 5: Test, Monitor, and Scale
Continuously monitor the success of the predictive maintenance program and make adjustments as necessary. Establish key performance indicators (KPIs) to measure the success of implementing machine learning for predictive maintenance and other PdM practices. Gather feedback from the maintenance team and stakeholders to continuously optimize processes and workflows.
Wrapping up
Industrial predictive maintenance is a powerful approach for manufacturing to promote asset performance optimization, reduce costs, and improve overall efficiency. By leveraging data analytics, machine learning, and IoT technologies, businesses can proactively identify and address potential equipment failures before they occur. The early detection of issues helps minimize downtime, lower maintenance costs, and extend the lifespan of machinery.
Let’s make your shop floor smart
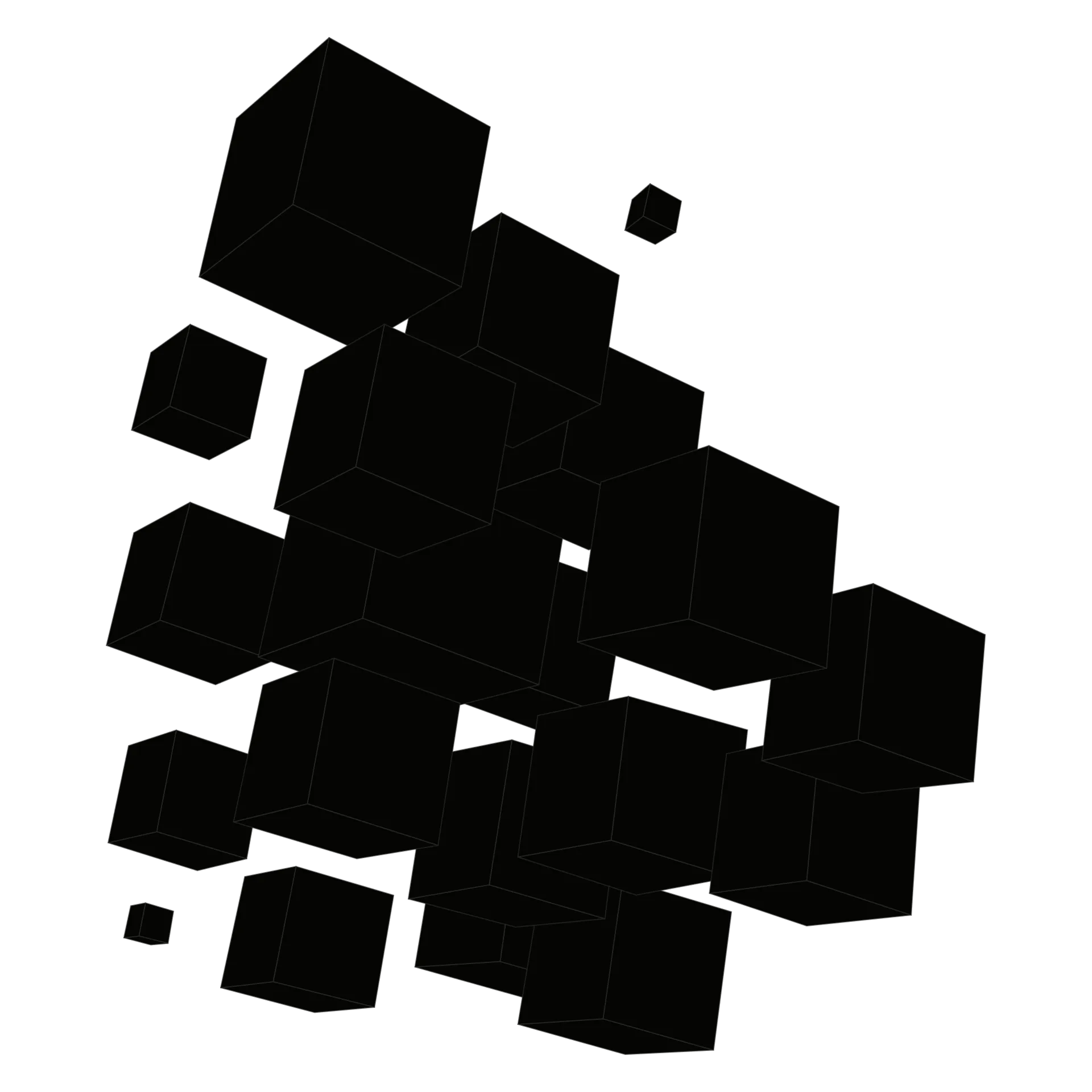
Business First
Code Next
Let’s talk
FAQ
One of the predictive maintenance examples is a manufacturing company that uses sensors to monitor the vibration levels of its equipment. When the vibration levels exceed predefined values, the system sends an alert to the maintenance team, indicating a potential bearing failure. Hence, scheduled maintenance is to be performed before the failure occurs, preventing unplanned downtime and costly repairs.
Predictive maintenance has a significant impact on manufacturing by:
- Reducing downtime—early detection of potential failures allows for scheduled maintenance, preventing unplanned downtime and production disruptions.
- Lowering maintenance costs—by identifying issues early, preventive measures can be taken to avoid costly repairs and replacements.
- Improving efficiency—well-maintained equipment operates at optimal levels, leading to increased efficiency and productivity.
- Extending equipment lifespan—proactive maintenance helps prevent premature wear and tear, extending the lifespan of machinery.
- Enhancing safety—predictive maintenance reduces the risk of unexpected equipment failures, which can pose safety hazards.
AI predictive maintenance manufacturing involves leveraging machine learning algorithms to analyze vast amounts of data collected from sensors and equipment. These algorithms can identify patterns, trends, and anomalies that may indicate potential failures. By analyzing historical data and real-time sensor readings, AI can predict when a piece of equipment is likely to fail.
To implement predictive maintenance in your manufacturing facility, you can follow these steps:
- Assess your current maintenance practices—evaluate your existing maintenance procedures to identify areas where predictive maintenance can be applied.
- Set goals—define specific objectives, such as reducing downtime or lowering maintenance costs.
- Implement hardware and software—select appropriate sensors, IoT platforms, and data analysis tools.
- Train your maintenance team—provide your team with the necessary training to understand and utilize predictive maintenance technologies.
- Test, monitor, and scale—continuously monitor the effectiveness of your predictive maintenance program and make adjustments as needed.
Yes, there are some challenges and limitations:
- High initial investment—implementing predictive maintenance can require significant upfront costs for hardware, software, and training.
- Data management complexity—managing and analyzing large volumes of data can be complex.
- Lack of expertise—finding qualified personnel with the necessary skills in data analytics and machine learning can be difficult.
- Change management—implementing predictive maintenance may require changes in organizational processes and culture.
Predictive maintenance can contribute to cost savings by:
- Reducing downtime—unplanned downtime can be extremely costly. Predictive maintenance helps prevent such disruptions, saving money.
- Lowering maintenance costs—by identifying issues early, preventive measures can be taken to avoid costly repairs and replacements.
- Improving equipment lifespan—proactive maintenance can extend the lifespan of equipment, reducing the need for costly replacements.
- Optimizing resource allocation—predictive maintenance enables more efficient allocation of maintenance resources.
Predictive maintenance utilizes various technologies, including:
- Sensors—to collect data on equipment performance.
- IIoT—to connect sensors and devices to a network for data transmission and analysis.
- Data analytics—to process and analyze large amounts of data.
- Machine learning—to develop predictive models and identify patterns.
- Digital twins—to create virtual representations of equipment for testing and simulation.
Build your ideal
software today
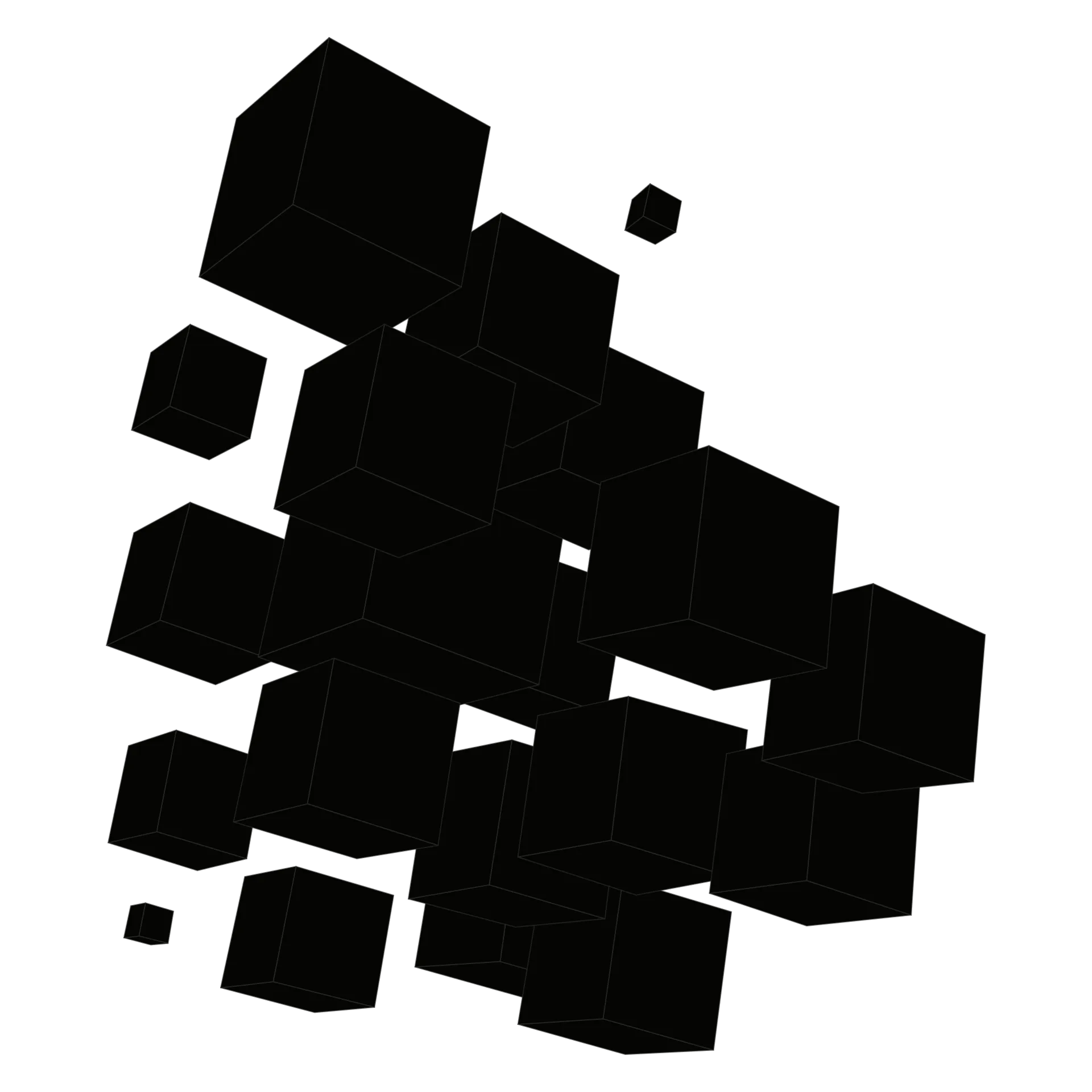