MES System Architecture
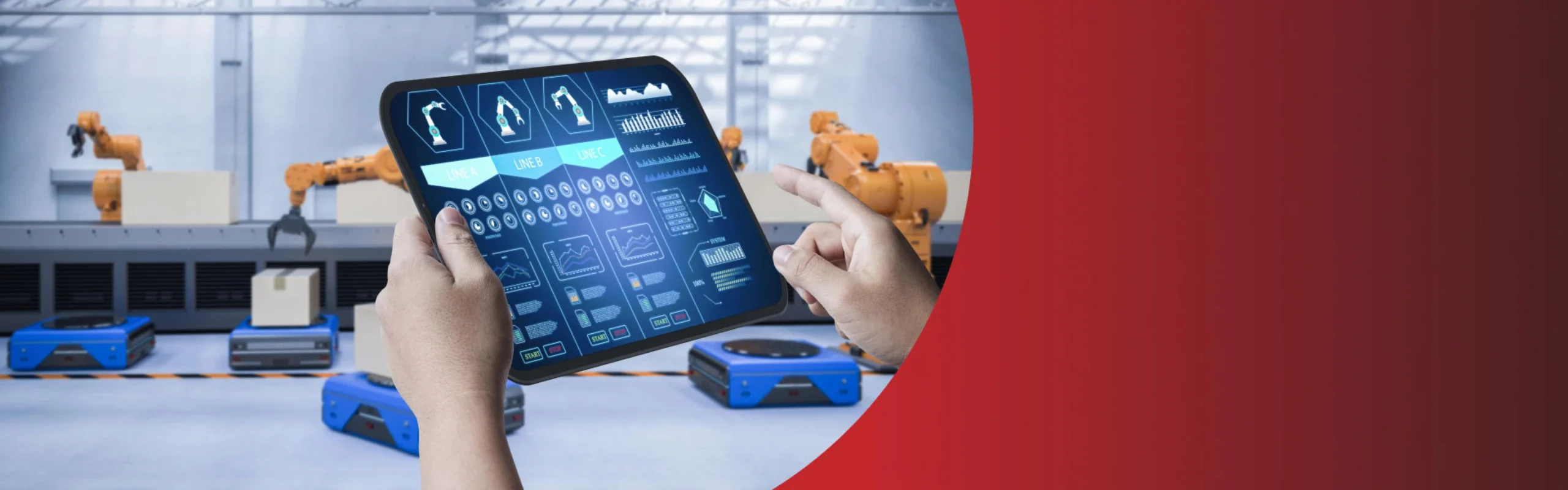
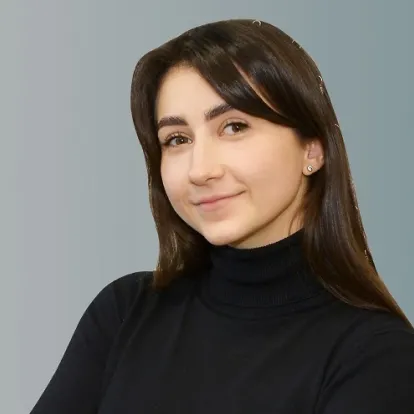
A manufacturing execution system (MES) is a digitized solution that comprises software and hardware components that enable full visibility and production control, connecting the business planning and operations control layers.
A 45% reduction in production time, a 50% decrease in paperwork, and a 15% drop in machine downtime are the foremost gains reported by manufacturers using MES.
But none of these results are achievable without one essential element: a solid MES architecture.
In the article below, you will learn more about the key components, architecture types, key considerations, and more.
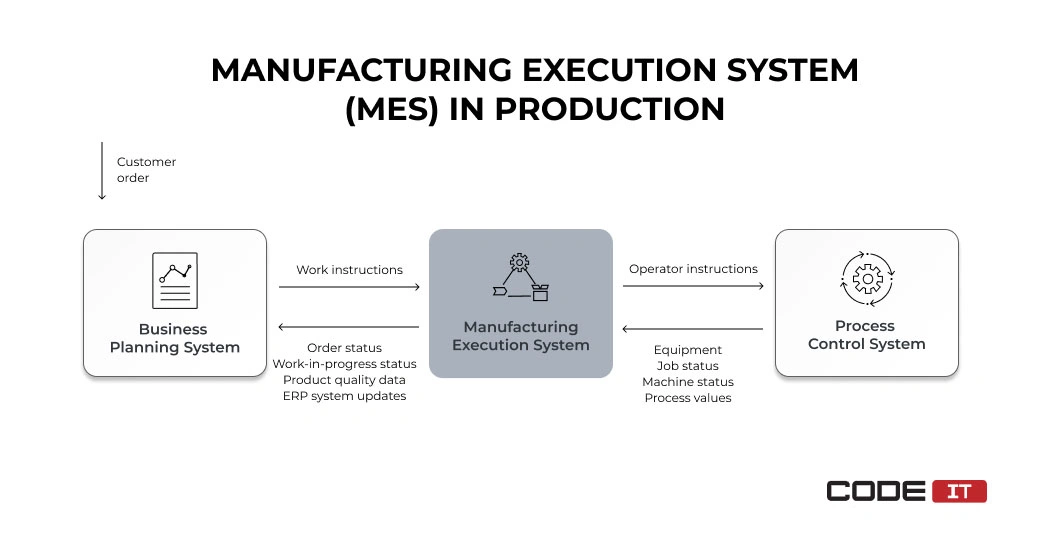
The functionality of an MES can be extended by connecting external modules for analyzing data, making reports, developing forecasts, etc.
Key components: hardware and software
The MES architecture comprises hardware and software components united into one system for monitoring and controlling manufacturing processes.
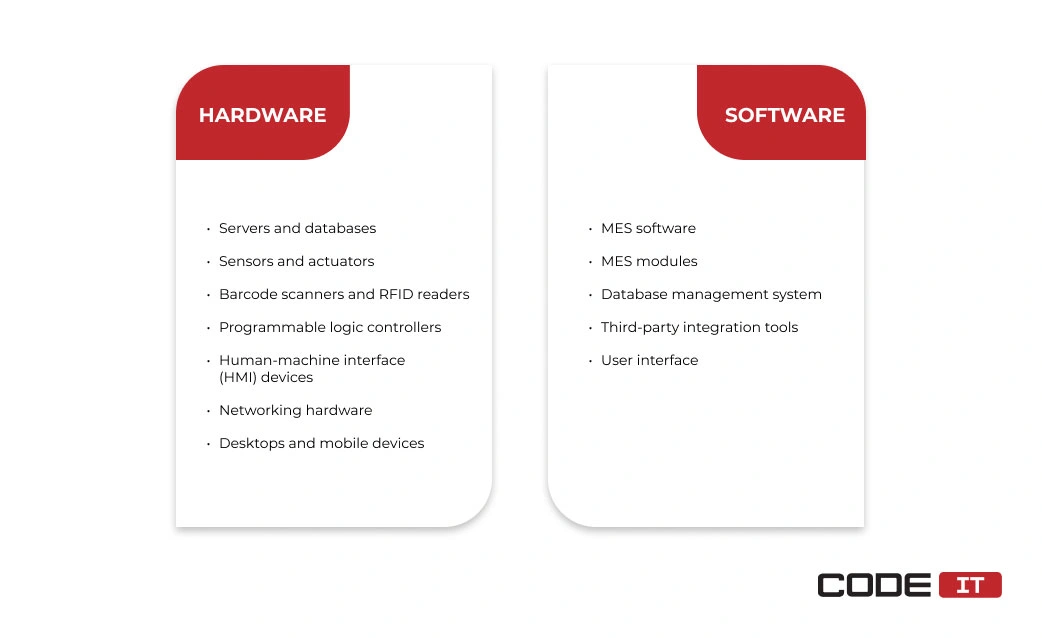
Hardware Components
The core hardware components that help interconnect production line machines and integrate them into an MES are as follows.
- Servers and databases.
On-premise or cloud-based servers host manufacturing execution software. Databases store the manufacturing data collected from machines.
- Sensors and actuators.
Gather information about crucial parameters like temperature, weight, speed, etc. Actuators perform machinery production processes.
- Barcode scanners and RFID readers.
Automatically collect data from scanned codes and tags to monitor inventory in real time.
- Programmable logic controllers.
Collect data and issue commands serving as a communication link between MES and shop floor machines.
- Human-machine interface (HMI) devices.
Touch screens and control panels used by staff to operate production machines.
- Networking hardware.
Routers, switches, wires, hotspots, and other devices create a local network and connect all the components.
- Desktops and mobile devices.
Equipment that is used for accessing collected data and using MES software.
Software Components
The core software components help enable the functionality of the manufacturing execution system.
- MES software.
Performs the manufacturing processes and operations management.
- MES modules.
Software components that enable additional functionality. The most popular modules are analysis, reporting, quality management, downtime management, maintenance, etc.
- Database management system.
Stores data retrieved from production floor machines.
- Third-party integration tools.
Additional software from third-party vendors that are connected via APIs.
- User interface.
The visual representation of MES software features tailored to the specific needs of users.
Launch digital transformation with CodeIT
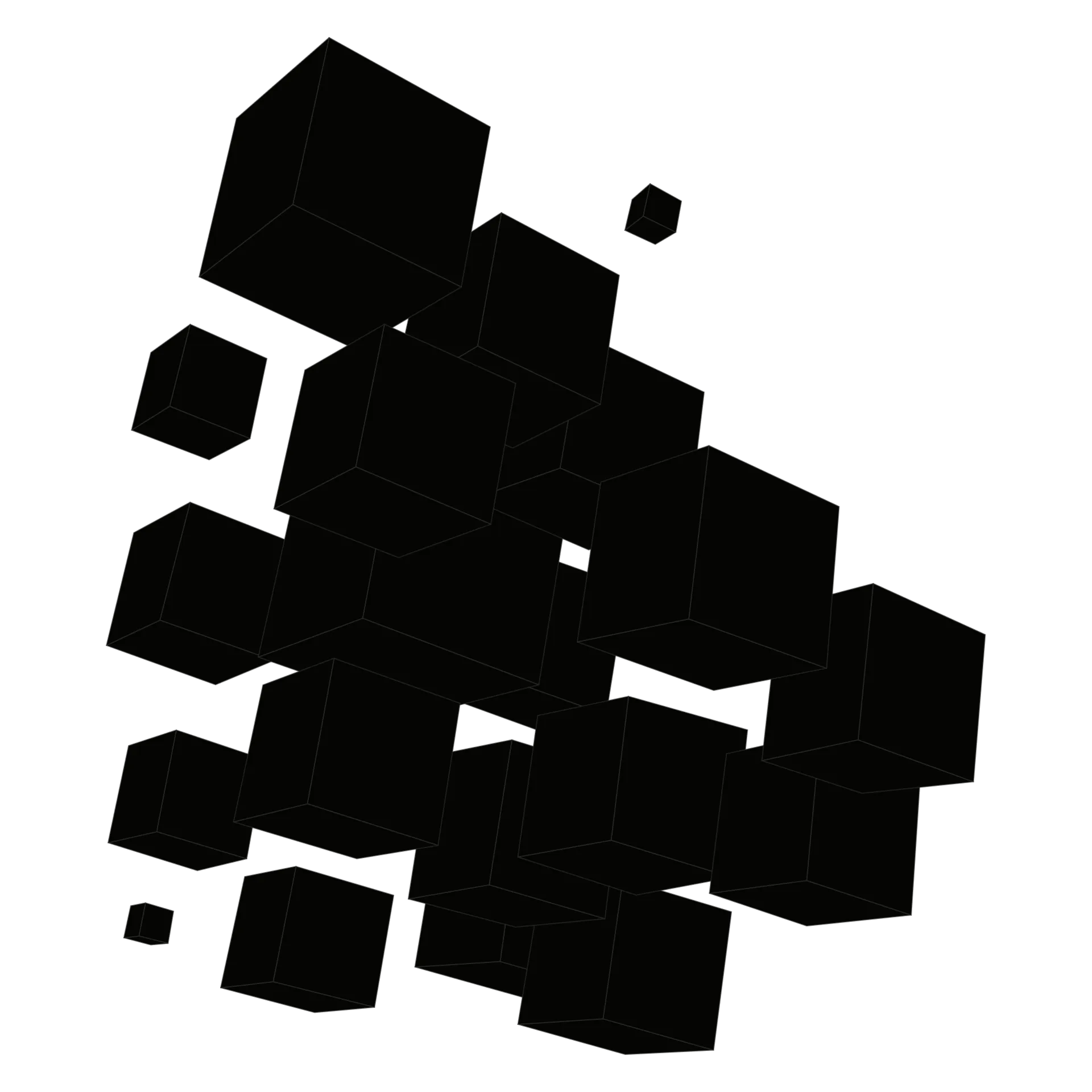
Business First
Code Next
Let’s talk
Types of MES architecture
The hardware and software components of a manufacturing execution system can be combined in different ways to achieve the maximum output. The most popular MES system architectures are listed below.
Monolithic
The manufacturing execution software is developed as a single component comprising all the required features. It is perfectly tailored to the needs of a specific production.
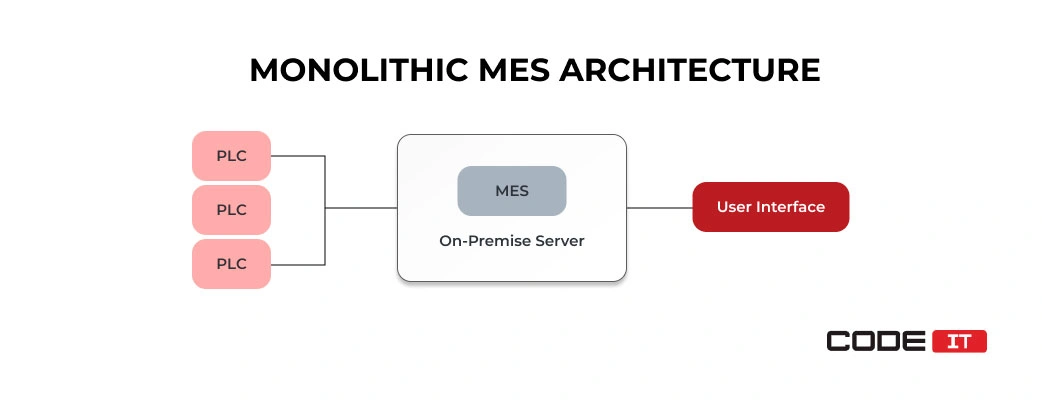
However, due to the monolithic approach, scaling up the existing monolith application and implementing new features upon demand may be challenging.
Module-Based
The modular MES architecture comprises diverse components interconnected into a single system. Each component of the system may use software from different vendors and can be developed using diverse technologies.
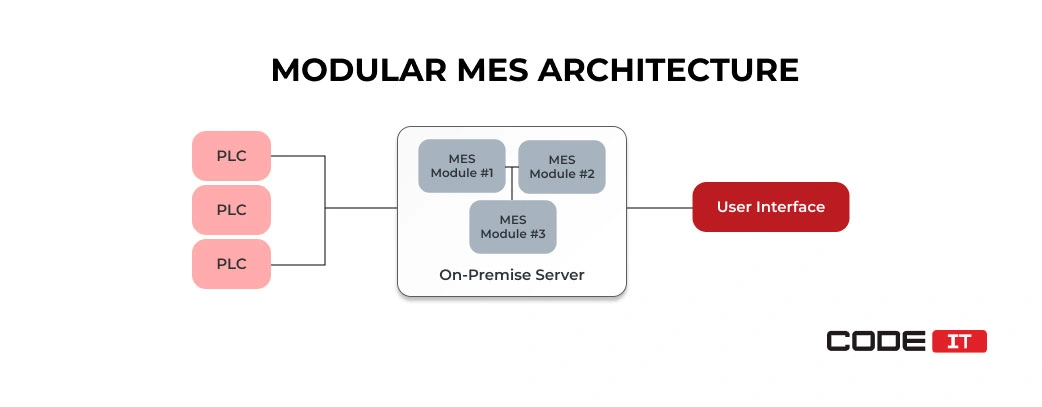
The module-based architecture enables top customization opportunities. The functionality of a MES can be enhanced by connecting additional modules, including the following:
- scheduling
- work-in-progress and inventory tracking
- quality management
- business intelligence
- machine utilization monitoring
Cloud-Based
The manufacturing software is hosted on remote servers that a third-party vendor manages. Cloud servers enable the opportunity to seamlessly scale up storage capacity and computing power upon a need. The software installed on a remote server can only be accessed via the Internet.
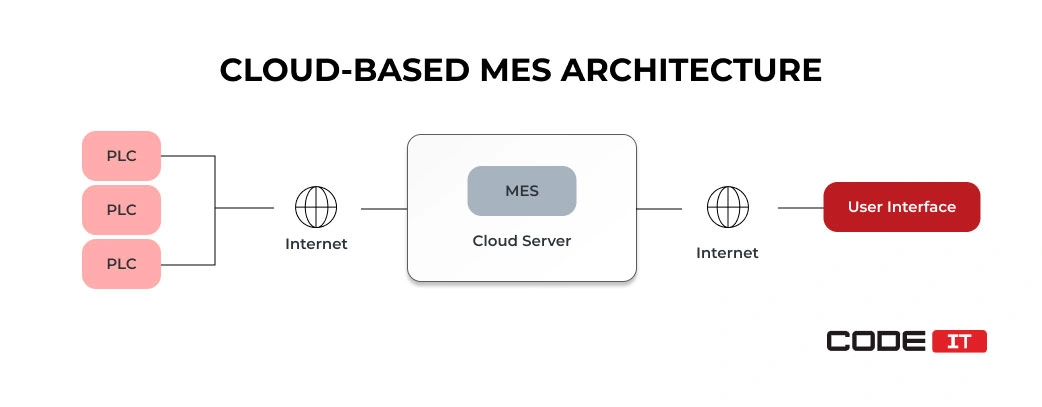
Hybrid
The hybrid MES architecture incorporates software components installed on cloud and local-based servers. It enables the opportunity to achieve the benefits of cloud-based infrastructure. Furthermore, this architecture of a manufacturing execution system helps maintain top system resilience and offline accessibility of its core components.
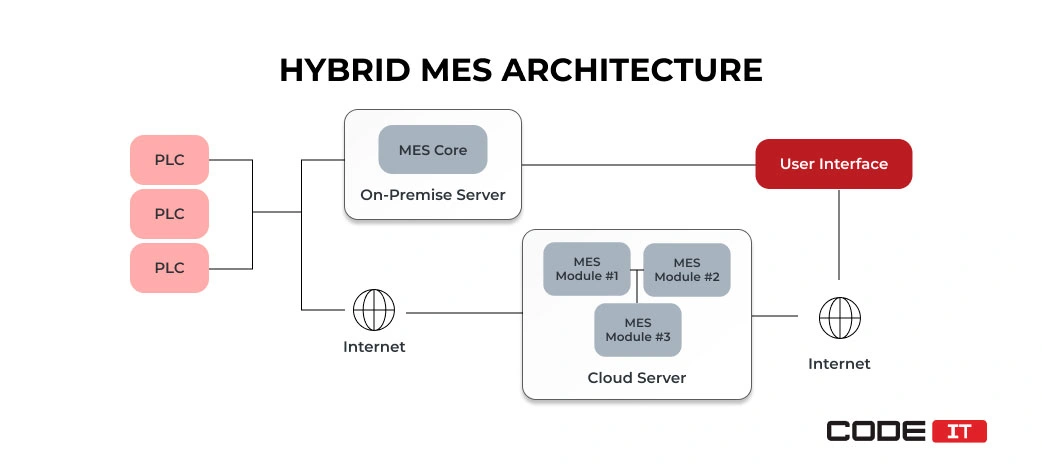
Edge-Based
The implementation of edge computing in an MES system architecture helps decrease the amount of data to be processed by the main server and transferred over a network. Edge nodes are small data processing units installed close to the manufacturing floor machines.
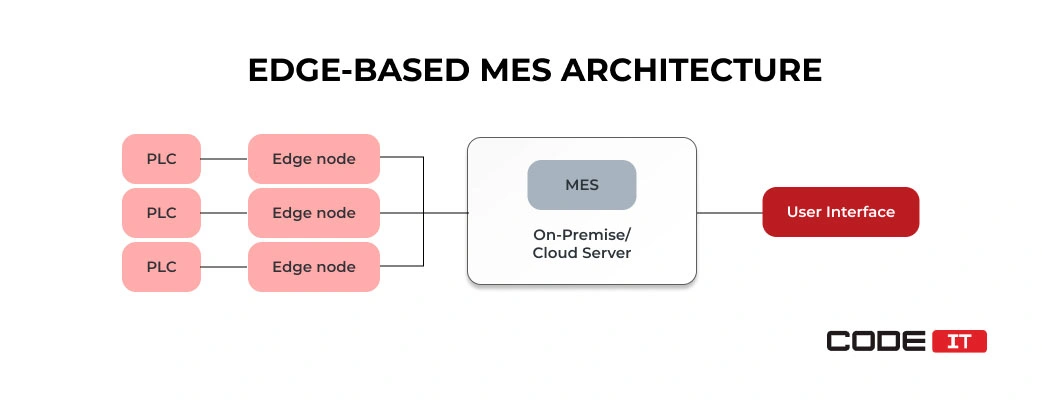
They collect and pre-process data. Hence, only summarized or critical information is transferred to the main server. Also, edge nodes can transform and validate collected data.
Integration with ERP systems and PLC
As per the ISA-95 framework, the MES architecture is a part of Level 3 (MES) of the industrial automation pyramid. It connects the machine control and business logic layers.
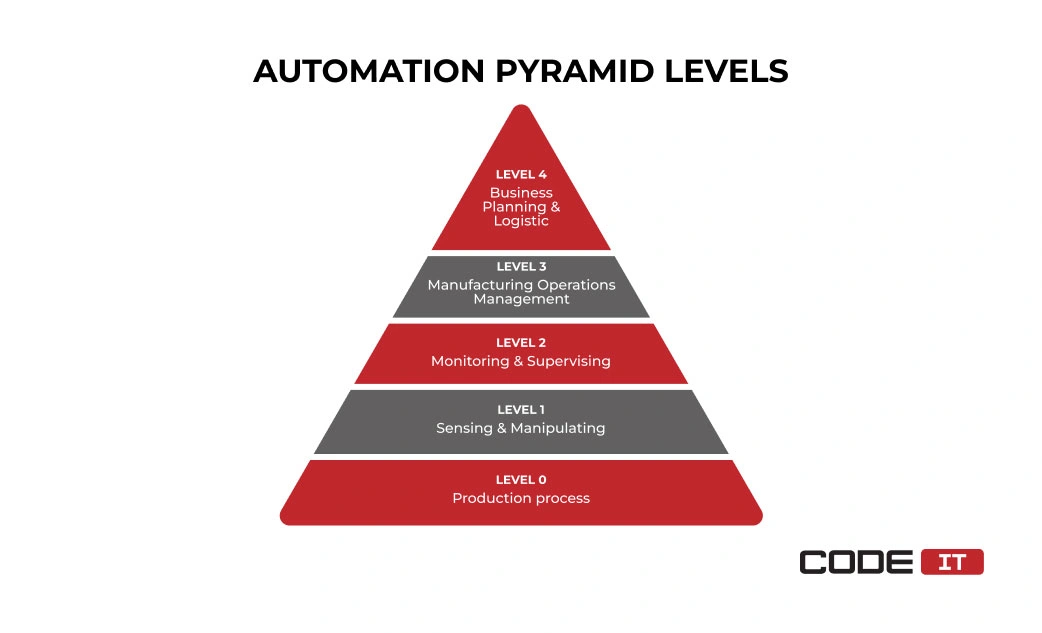
Level 0 (Production process) describes the overall manufacturing processes, materials, equipment, etc.
Levels 1,2 (Sensing, monitoring, and control) are represented by:
- programmable logic controllers (PLCs)
- sensors (scales, optic readers, scanners, thermometers, etc.)
- actuators and automatic guided vehicles (AGVs)
- transmitters and network devices
- human-machine interface (HMI) devices
The devices help enable real-time manufacturing control and monitoring.
Level 3 (Manufacturing operations management) is represented by MES software. It helps coordinate and control manufacturing processes using a centralized system.
Level 4 (Business planning and logistics) is represented by enterprise resource planning (ERP) software. It helps ensure that production operations are perfectly aligned with business goals.
MES Implementation Guide
Benefits of a robust MES system
The implementation of a manufacturing execution system enables process management and optimization and digitized manufacturing. The five core benefits of MES software integration are as follows.
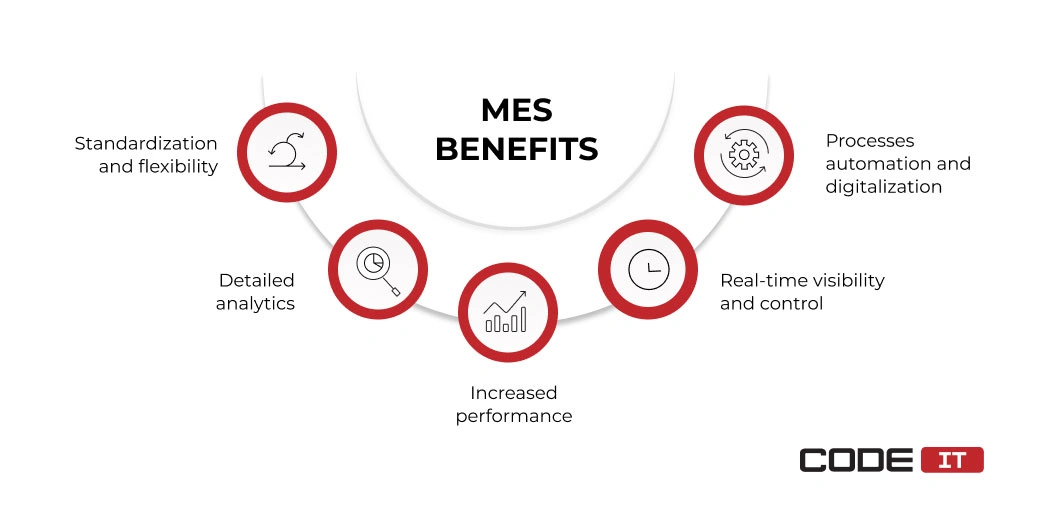
Workflow Automation and Digitalization
Integrated MES solutions enable automation of business operations. Programmable logic controllers can be fully and autonomously managed by MES software. It can collect sensor data and issue commands to PLCs based on pre-developed algorithms.
Developing custom user agents helps create custom rules to automate manufacturing processes, including production scheduling, quality control, or supply chain management. All the data can also be processed and outputs presented as custom reports.
Real-Time Visibility and Control
Data-sharing pipelines in a MES architecture enable real-time data collection and command issuing. Hence, responsible managers can monitor and control in-progress processes with minimal delay. It can range from 10ms to several seconds, depending on the implemented MES system architecture and process optimization.
Increased Performance
Adopting smart manufacturing and shop floor management helps reduce the manual input required to run processes. Moreover, automated data processing and input help reduce the number of errors and lower the administrative burden on the labor force, promoting continuous improvement.
Performance Analytics
Business intelligence (BI) modules in a MES architecture help analyze, summarize, and visualize collected data. Also, BI solutions can automatically generate custom reports.
Advanced technologies like Artificial Intelligence (AI) help streamline data collection and analysis by turning large raw information into valuable insights, forecast changes, and run predictive maintenance.
Standardization and Flexibility
Data mapping and standardization are a crucial part of a robust MES architecture. It enables the opportunity to build cross-system pipelines and integrate third-party solutions. Hence, stakeholders can rapidly enhance or adjust the functionality of existing systems, making change management smooth.
Key considerations for MES architecture design
The MES system architecture design and implementation require a business to clearly understand the following.
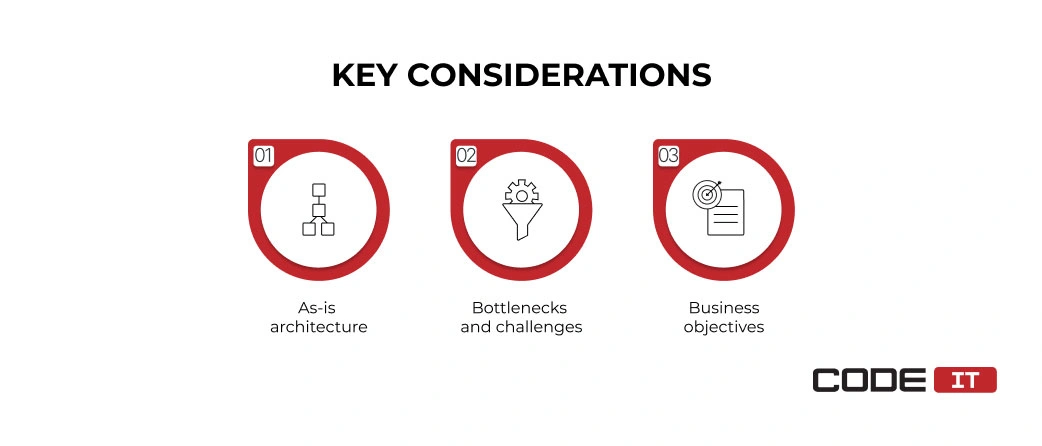
1. As-Is Architecture
Examine the existing design of the manufacturing environment. The as-is design helps outline the existing hardware and software solutions used for monitoring and managing production processes. Define technical boundaries to consider when designing a MES architecture.
2. Bottlenecks and Challenges
Identify the bottlenecks in existing processes and workflows that should be optimized. List all the challenges and boundaries that hold you back from implementing innovative solutions.
3. Business Objectives
Define and prioritize business goals to achieve. All the objectives should be described in detail. The MES architecture implementation outcomes should be defined considering the realistic budget and business capabilities. Also, it’s recommended to set clear “definition of done” characteristics for each business objective.
4. Integration Capabilities
Clearly understand the need for your MES to be integrated with third-party systems like ERP, CRM, or SCADA. Define the data formats the system uses that should be connected and integration compability requirements. In some cases, additional data transformation software is required to enable real-time data sharing across different departments.
5. Scalability
Analyze your business vision to understand if the functionality of your MES architecture will need to be expanded in the future. The scalability plan helps to ensure that new machines can be added, new features incorporated, and more third-party services integrated into the existing MES.
6. Regulatory Compliance
Map out all the industry-specific regulatory requirements and standards. It helps avoid change requests aimed at improving reporting capabilities and quality control procedures. Also, adherence to industry standards helps build a safe and compliant manufacturing environment.
7. Automation Capabilities
Assess workflows in your organization to enable automation of business operations. Streamline routine tasks, reduce manual intervention, and improve operational efficiency with data-sharing pipelines and automated activities.
8. Mobile Accessibility
Consider the need to have mobile access to your MES. Choose the best-fitting technologies for developing mobile applications and syncing all the data in real time. Also, choose additional features to incorporate into mobile applications, allowing managers, engineers, and operators to monitor and control processes remotely.
MES for operational digitalization
The implementation of manufacturing execution systems (MES) helps manufacturing businesses digitize operations, adhering to Industry 4.0 practices and automation.
The digital transformation promoted by MES development and implementation are:
- Production scheduling
Run effective production planning by aligning with digital batch records and production routings. Ensure all the processes are synchronized, maintaining smooth workflows.
- Work order management
Manage work orders and track production processes thoroughly, enabling transparency and traceability in a paperless environment.
- Real-time production monitoring
Collect manufacturing data from different sources in live time. Stay alerted about unforeseen issues that need immediate response.
- Data analysis and reporting
Gather machinery data and analyze it to get production insights. Make all the data convenient to consume by composing custom reports and charts on dashboards.
- Document management
Organize, store, and control all manufacturing and quality-related documents within a centralized digital system.
- Electronic signatures
Streamline processes and comprehensively track all activities on a shop floor with electronic signatures.
- Quality control
Monitor and maintain product quality through integrated quality control checks.
- Workflow automation
Create digital agents that help automate bothersome and repetitive tasks.
MES mobile applications
Mobile applications integrated with manufacturing execution systems help users access crucial information and functionality on the go. Moreover, mobile apps help improve the efficiency of the shop floor teams.
The foremost applications of MES-integrated mobile applications are:
- Daily task management
Run real-time tracking of production metrics. Get push notifications to stay alerted about production issues and performance drops.
- Labor management
Implement attendance tracker for shop floor workers and enable KPI monitoring.
- Quality assurance
Ensure top production quality by allowing operators to quickly identify and address defects and enable access to inspection documentation.
- Energy monitoring
Enable real-time energy monitoring with the help of mobile data collection. Track and analyze energy consumption to identify high-usage areas.
- Maintenance management
Use a maintenance calendar to schedule regular inspections and repairs, reducing the chance of unexpected breakdowns.
Statistics and future trends
As per statistics, the global manufacturing execution system market is expected to reach $42.2 billion by 2030, growing at a CAGR of 13.1%.
The other key statistics that highlight the high-paced growth of manufacturing execution system adoption are:
- Over 80% of manufacturing businesses use MES
- MES usage helps reduce the manufacturing time by 45% or more
- Manufacturers report that MES helps decrease paperwork by 50%
- 60% of businesses state that MES usage is a crucial component of success
- MES implication helps reduce the machine downtime by 15%
The future trends that shape the manufacturing execution system market are as follows.
- Cloud-based infrastructure.
The usage of remote servers that a third-party vendor manages.
- IIoT integration.
Smart devices that are interconnected by one network. The industrial Internet of Things, as a part of the MES system architecture, helps monitor and remote manufacturing workflows remotely.
- Edge computing.
Dedicated computing nodes help pre-process data collected from PLCs. Edge nodes help decrease the amount of data transferred over a network.
- Artificial intelligence.
AI algorithms help analyze large amounts of data and detect hidden patterns. Also, using AI helps enable computer vision and predictive machine maintenance.
- Modular design.
The integration of third-party services helps enrich the functionality of manufacturing execution systems. Modular-based SAP MES architecture combines solutions built using diverse technologies.
CodeIT expertise
Our team has developed and implemented many successful solutions for monitoring and controlling manufacturing processes.
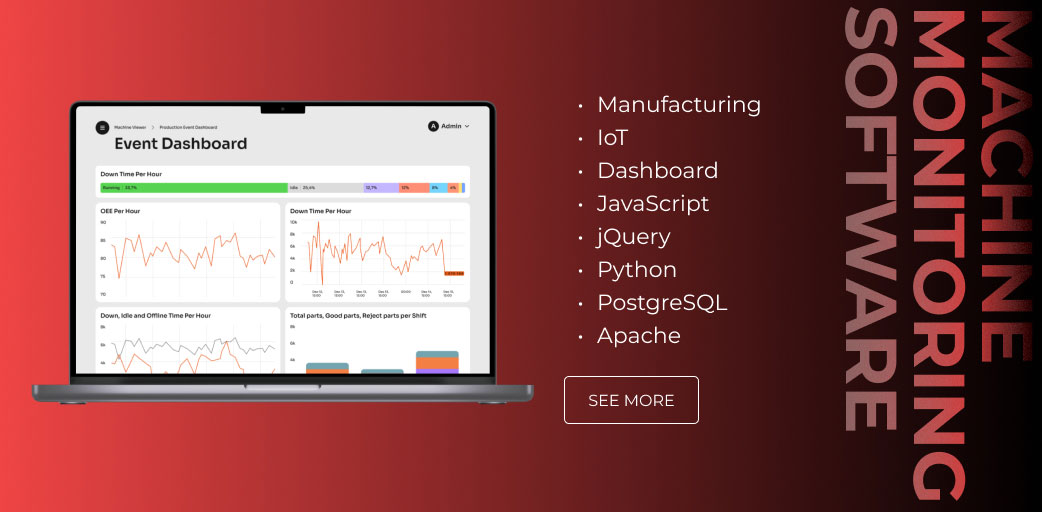
The machine uptime monitoring software is one of the completed projects. Let’s check the business problems and solutions delivered by the CodeIT team.
Problem
The client is a manufacturer that experienced a lack of work-in-progress control and monitoring. The CodeIT team was tasked with developing a new software solution that enables the opportunity to:
- monitor work-in-progress
- analyze manufacturing data
- create charts and custom reports
- present real-time data on a dashboard
- manage user roles and permissions
Solution
The business analysis expert has examined business goals and prepared a detailed software development plan. It included user stories, definition of done, KPIs, etc.
The team of front-end and back-end developers have designed the MES architecture and implemented all the features, following the prepared plan.
The software and dashboard can be accessed via the Internet from any location.
Summing up
The MES architecture combines hardware and software components to monitor and control production machines. It connects sensors and PLCs, offering the opportunity to manage production processes effectively and check work-in-progress data in real time.
The key components of an MES architecture are as follows.
Hardware Components | Software Components |
---|---|
Servers and databases | MES software |
Sensors and actuators | MES modules |
Barcode scanners and RFID readers | Database management system |
Programmable logic controllers | Third-party integration tools |
Human-machine interface (HMI) devices | User interface |
Networking hardware | |
Desktops and mobile devices |
Ideal MES architecture? Design with CodeIT!
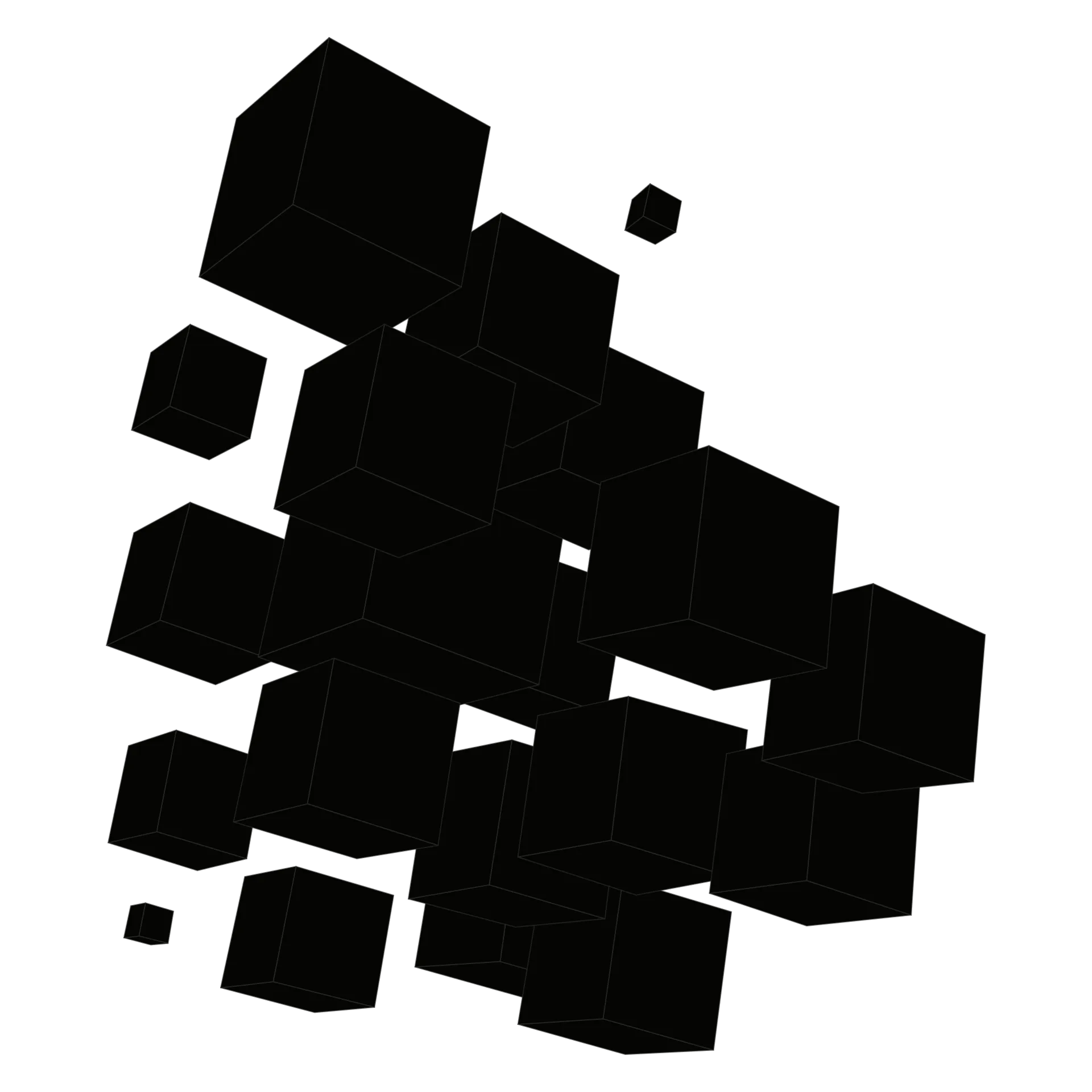
Business First
Code Next
Let’s talk
FAQ
The MES architecture is a combination of software and hardware components that form a unified system. All the elements are arranged in a certain order to enable the required functionality and workflow visibility.
It provides instant access to manufacturing data and provides the opportunity to issue commands in real time. The MES system is the integration layer between programmable logic controllers (PLCs) and enterprise resource planning (ERP) systems.
The core hardware components of a MES architecture are:
- servers and databases
- sensors and actuators
- barcode scanners and RFID readers
- programmable logic controllers
- human-machine interface (HMI) devices
- networking hardware
- desktops and mobile devices
- MES software
- MES modules
- database management system
- third-party integration tools
- user interface
The software components of a manufacturing execution system (MES) include the following:
- servers and databases
- sensors and actuators
- barcode scanners and RFID readers
- programmable logic controllers
- human-machine interface (HMI) devices
- networking hardware
- desktops and mobile devices
- MES software
- MES modules
- database management system
- third-party integration tools
- user interface
The five most widely used types of MES architecture are:
- Monolithic
- Module-based
- Cloud-based
- Hybrid
- Edge-based
According to statistics, a well-designed MES architecture enables reducing production time by 45% or more. Furthermore, it helps decrease the paperwork by 50%.
The three main Industry 4.0 goals are:
- increased automation and flexibility
- real-time workflow visibility
- advanced analytics
Implementing a MES architecture helps achieve these goals by enabling automation and complete visibility. Also, it helps turn large amounts of raw data into valuable insights. Integrated solutions enable real-time data sharing by using cross-platform pipelines.
The key future trends in the MES market are:
- cloud-based infrastructure
- IIoT integration
- edge computing
- artificial intelligence
- modular design
Related services and industries
Software Architecture Consulting
Build a solid architecture for your app
Manufacturing Software Development Services
Looking for MES implementation experts?
Business Analysis Services
Hire BA expert
Build your ideal
software today
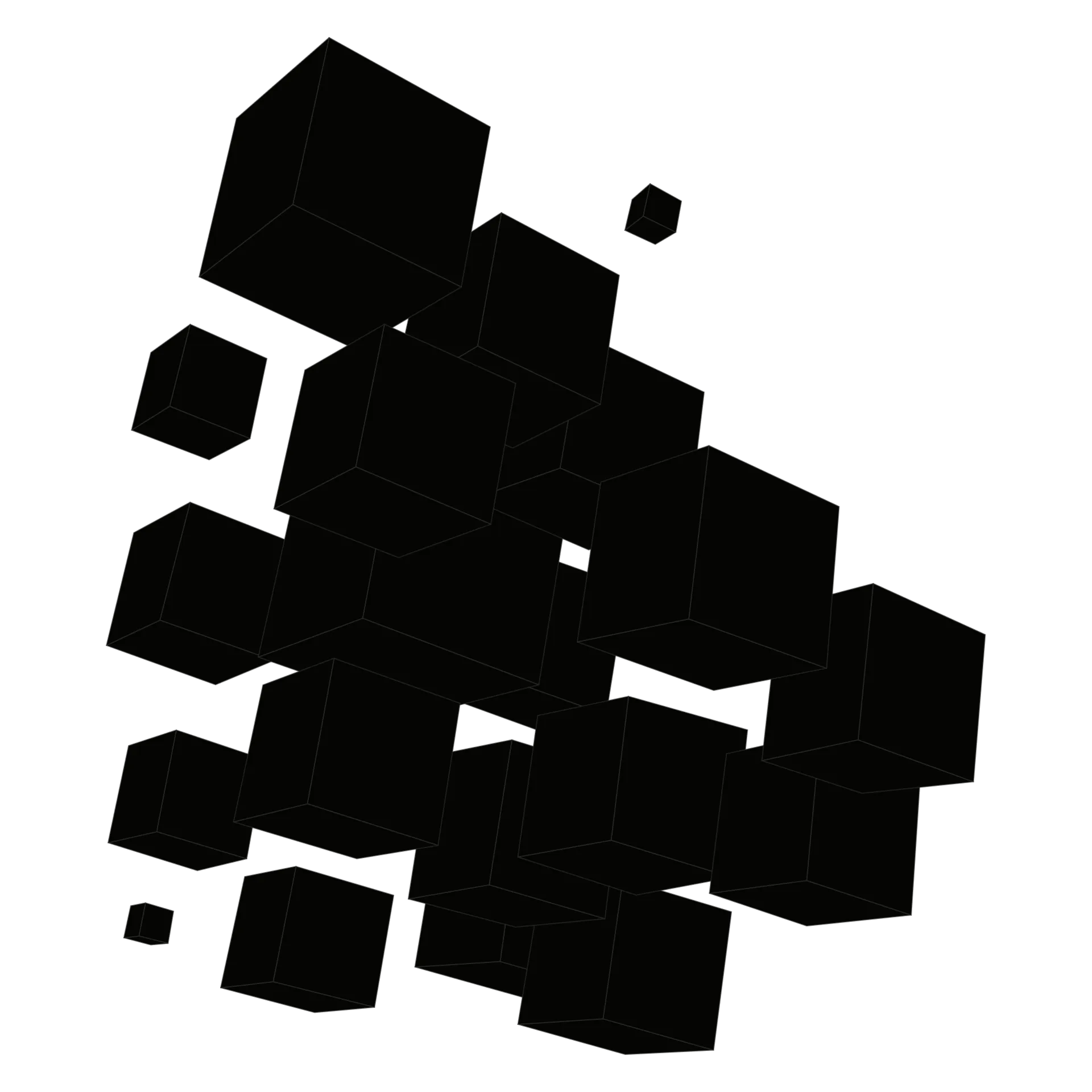