Industrial IoT For Manufacturing
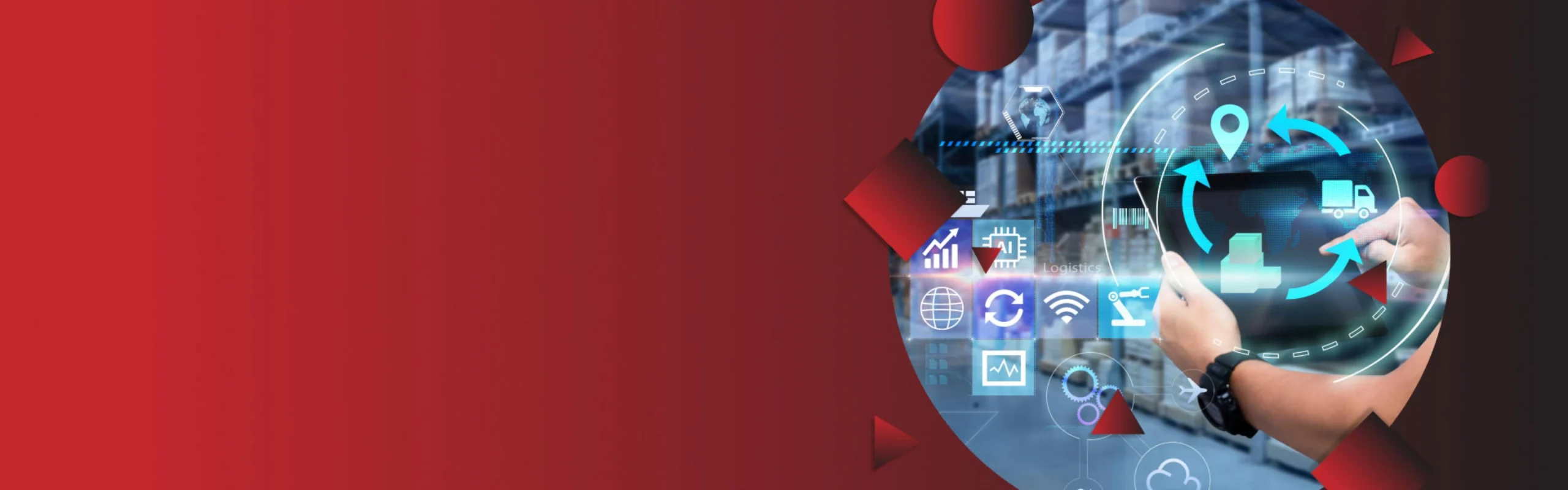
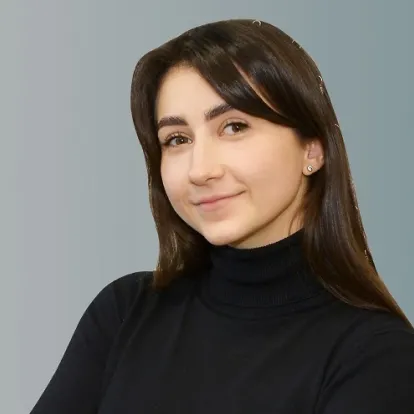
Internet of Things (IoT) describes a network of smart devices capable of capturing, preprocessing, and sharing data.
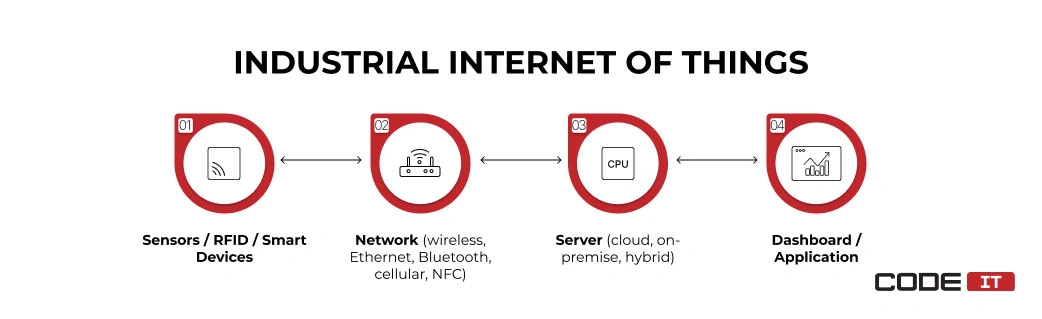
Industrial Internet of Things (IIoT) is an umbrella term that describes the narrowed list of IoT devices—applicable in manufacturing only.
IoT solutions for manufacturing help control shop floor operations in real time, issue commands, analyze collected data, predict machine downtime, and more. The most popular IIoT devices are as follows.
IIoT Devices | Applications | Device Example |
---|---|---|
Industrial controllers | – Control of event sequence – Task automation and command issuing – Data collection | – Nano PLCs – Safety PLCs – Modular PLCs – Micro PLCs |
Sensors | – Physical properties check – Gas/liquid detection – Environmental conditions monitoring | – Temperature sensor – Pressure sensors – Flow/speed sensors – Level sensors – Position sensors – Scales |
Scanners | – Barcode/RFID scanning – Defect detection – Surface/composition inspection – Item dimension and placement check – Asset tracking | – Barcode scanner – RFID scanners – CT scanners – X-ray scanners – Ultrasound scanners |
Cameras | – Object detection – Package identification – QR code scanning – ML-driven scanning – Product line monitoring – Surveillance | – Smart cameras – Thermal imaging cameras – Low-light cameras – High-speed cameras |
Actuators and smart robots | – Repetitive tasks automation – Item picking and transportation – 24/7 operations – Collaborative work | – Programmable valve – Programmable actuator – Robotic arm – Automated guided vehicles |
Application of IoT for smart manufacturing
IIoT devices help enable real-time process visibility and optimize workflows. Read about the IoT applications for manufacturing and real-world cases.
1. Real-Time Data Collection
Shop floor data can be gathered from sensors and delivered to a centralized repository in real-time—with minimal (10ms-100ms) delay. The information is displayed on a dashboard that can be accessed from any location via the Internet. Furthermore, the data can be pre-processed, transformed, and visualized upon request.
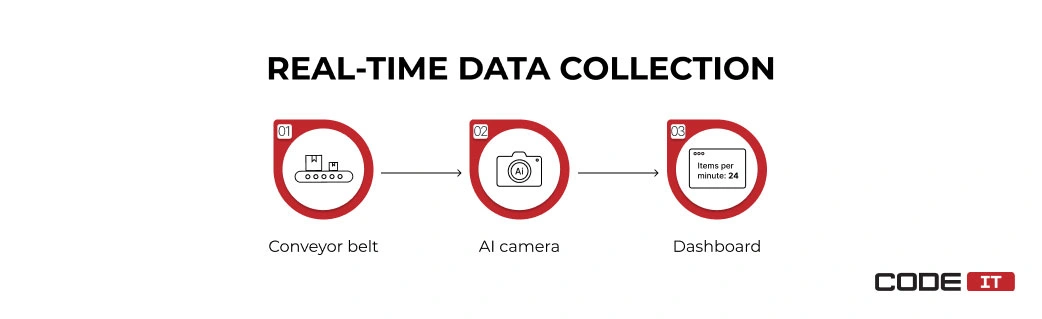
Real-world application:
The Boeing Company collects real-time data from over 500 welding machines in one facility. This information helps detect bottlenecks and monitor machine performance in real time.
2. Data Analysis and Forecasting
The large amounts of inventory data fetched from IIoT devices for manufacturing help discover useful insights. The baseline functionality of business intelligence modules helps visualize collected data, summarize it, and generate charts. Besides, stakeholders can discover anomalies and forecast trend changes by applying machine learning technology to data analysis.
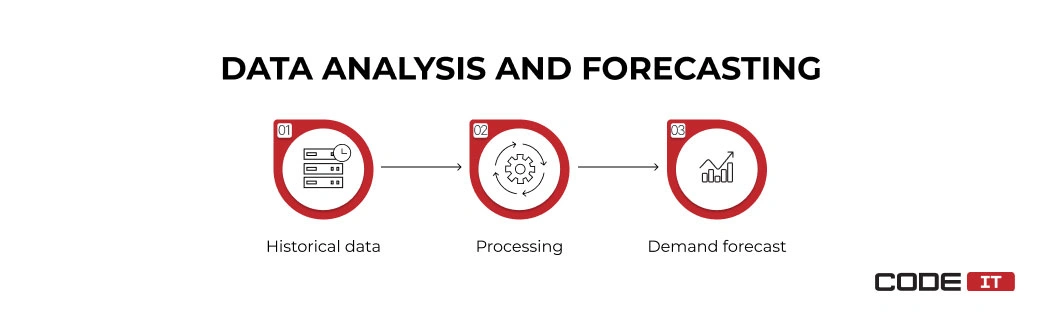
Real-world application:
The Ford Motor Company collects data from product line machines and applies ML-driven algorithms to analyze it. The deep analysis of factors like cycle times and robot performance has helped the company to increase production efficiency by 10%.
3. Workflow Automation
PLCs and IoT solutions for manufacturing in a product line help automate tedious tasks by developing custom user agents. The sensor technology in manufacturing can count the number of produced items and raw materials consumed. The usage of collaborative robots and robotic arms helps move items and materials.
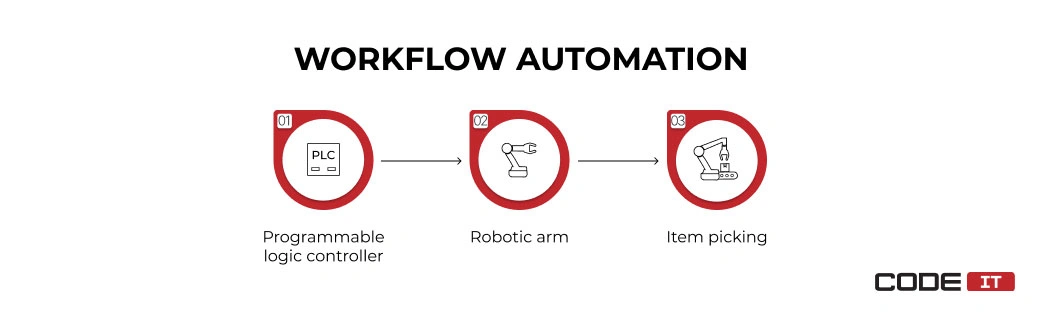
Examples of manufacturing automation in the manufacturing industry include:
- automated conveyor belt adjustment
- material handling and replenishment
- automated quality control
- data analysis and automated alerting
Real-world application:
Siemens has installed over 1,000 automation controllers in its electronics manufacturing plant in Amberg, Germany. The use of PLCs has helped the company automate up to 75% of operations.
4. Energy Consumption Optimization
The use of IoT solutions for smart manufacturing helps thoroughly analyze energy efficiency and discover ways to eliminate unnecessary spending. It also helps identify the sources of abnormal energy consumption.
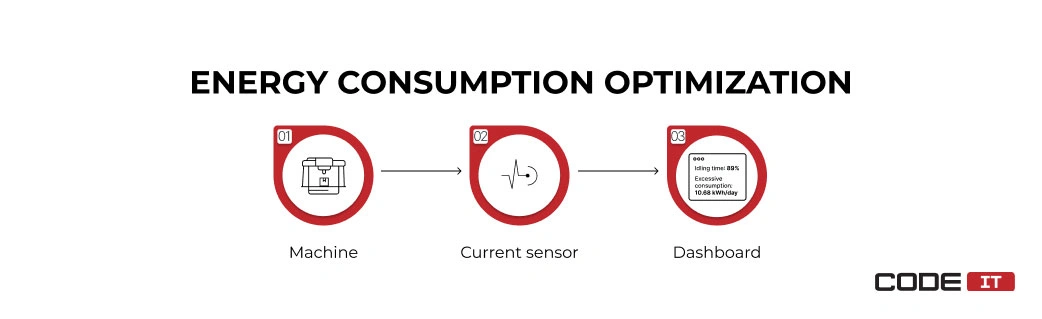
Real-world application:
BMW’s production plant in Spartanburg (SC, USA) uses IoT-based energy management. IoT devices to constantly meter energy consumption. Real-time data analytics helps identify anomalies and predict energy consumption trends. The solution has helped to achieve the savings of 100,000 kWh per year.
5. Production Quality Control
Cameras, scanners, and smart devices help automatically control the quality of produced items. The examples of product quality control enabled by IoT devices are:
- visual body/surface inspection with ML-enabled machine vision
- temperature check with thermal sensors
- defect identification with CT/x-ray/ultrasound scanning
- visual inspection of item assembly using smart cameras
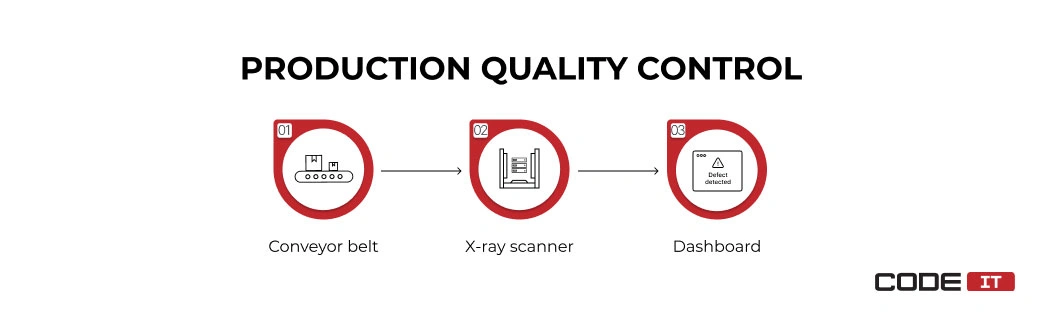
Real-world application:
Schneider Electric, the electrical equipment manufacturer, uses AI-driven cameras to inspect created products and automatically identify defects. Moreover, sensors embedded in production lines help monitor environmental conditions like temperature and humidity.
6. Inventory Management
Unique device identification (UDI) scanners and RFID readers help track inventory locations in real time. Moreover, computer vision uses images captured by cameras to identify packages.
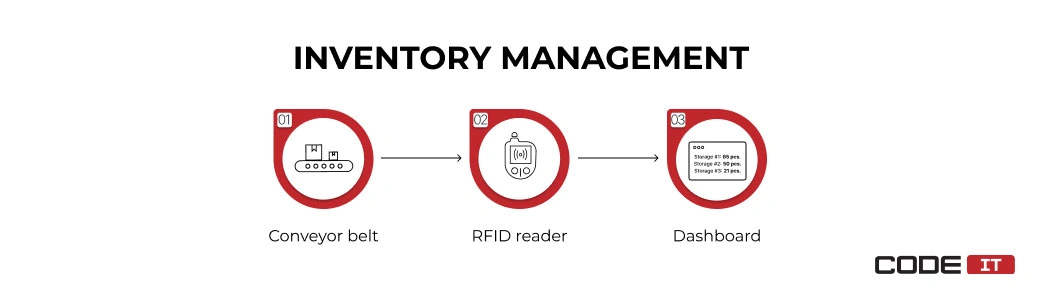
Real-world application:
Amazon uses RFID tags and barcode scanners to track the location of packages manually or electronically. Furthermore, the company used machine vision technologies to identify packages by analyzing camera videos.
7. Predictive Maintenance
Industrial IoT for manufacturing helps continuously monitor equipment conditions. For instance, vibration sensors can detect equipment imbalance or misalignment. Machine Learning, which analyzes data from IoT sensors, helps identify anomalies and predict possible machine failures.
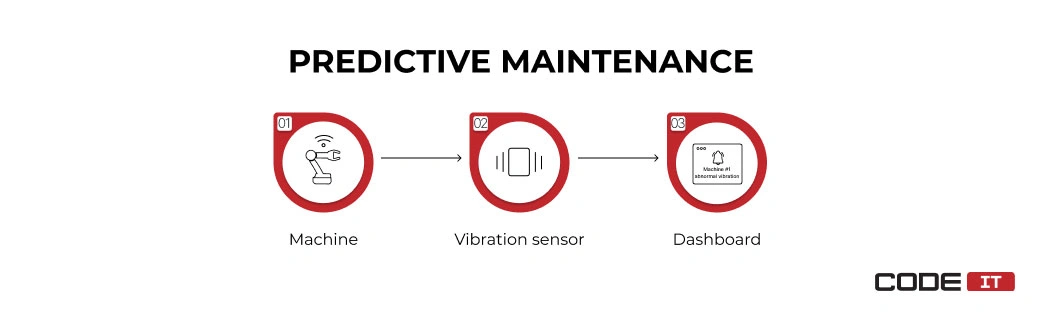
Real-world application:
General Electric collects more than 30,000 operating hours of data per day from its IoT-enabled wind turbines. The data on rotor speed and weather conditions help create predictive maintenance models, which result in savings of more than $70 million per year.
8. Environment Monitoring and Control
IoT solutions for the manufacturing industry help monitor environmental conditions in production facilities. Smart devices help adjust HVAC systems remotely by issuing commands from the central server. Furthermore, user agents help control and adjust automated environmental conditions.
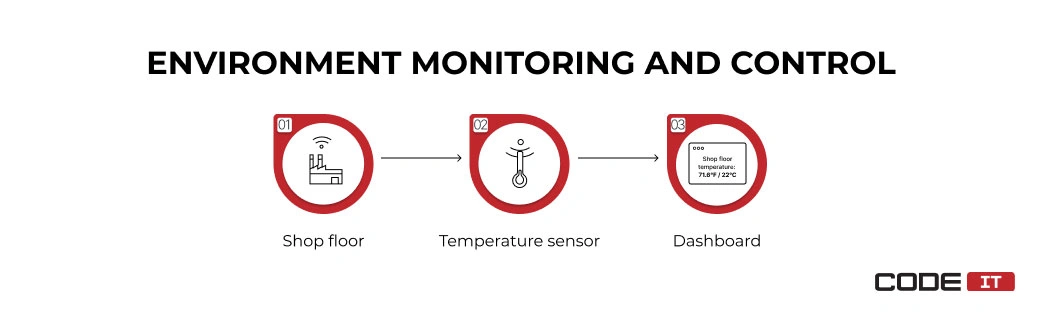
Real-world application:
Unilever uses sensors and user agents to control automated environmental conditions in production facilities. The installed and interconnected smart sensors monitor the temperature, humidity, and air quality to maintain the required quality for managing perishable products.
IoT In Warehouse Management
Smart vs traditional manufacturing
As per the research, IIoT is the #1 solution implemented by Industry 4.0 adopters. Smart devices help enable real-time visibility, optimize workflows, and make data-baked decisions.
Check the comparison of smart and traditional manufacturing below.
Traditional Manufacturing | Smart Manufacturing | |
---|---|---|
Data | Not fully captured and analyzed | Read time data, visualization, and predictive analysis |
Operations | Labor-intensive input and manual operations | Automated workflows and full operations control |
Downtime | Unforeseen technical issues | Predictable and planned |
Maintenance | Machines monitored by technicians | 24/7 machine monitoring enabled by sensors |
Supply Chain | Manual cycle counting using spreadsheets | Automated inventory tracking and full visibility |
Energy Consumption | Lack visibility | Idling machines and excessive consumption identification |
Quality | Manual item inspection | Items are inspected by AI cameras or industrial scanners automatically |
Decision-Making | Professional experience and poor data | Decisions based on insights and predictions delivered by smart algorithms |
Digitize your production with CodeIT
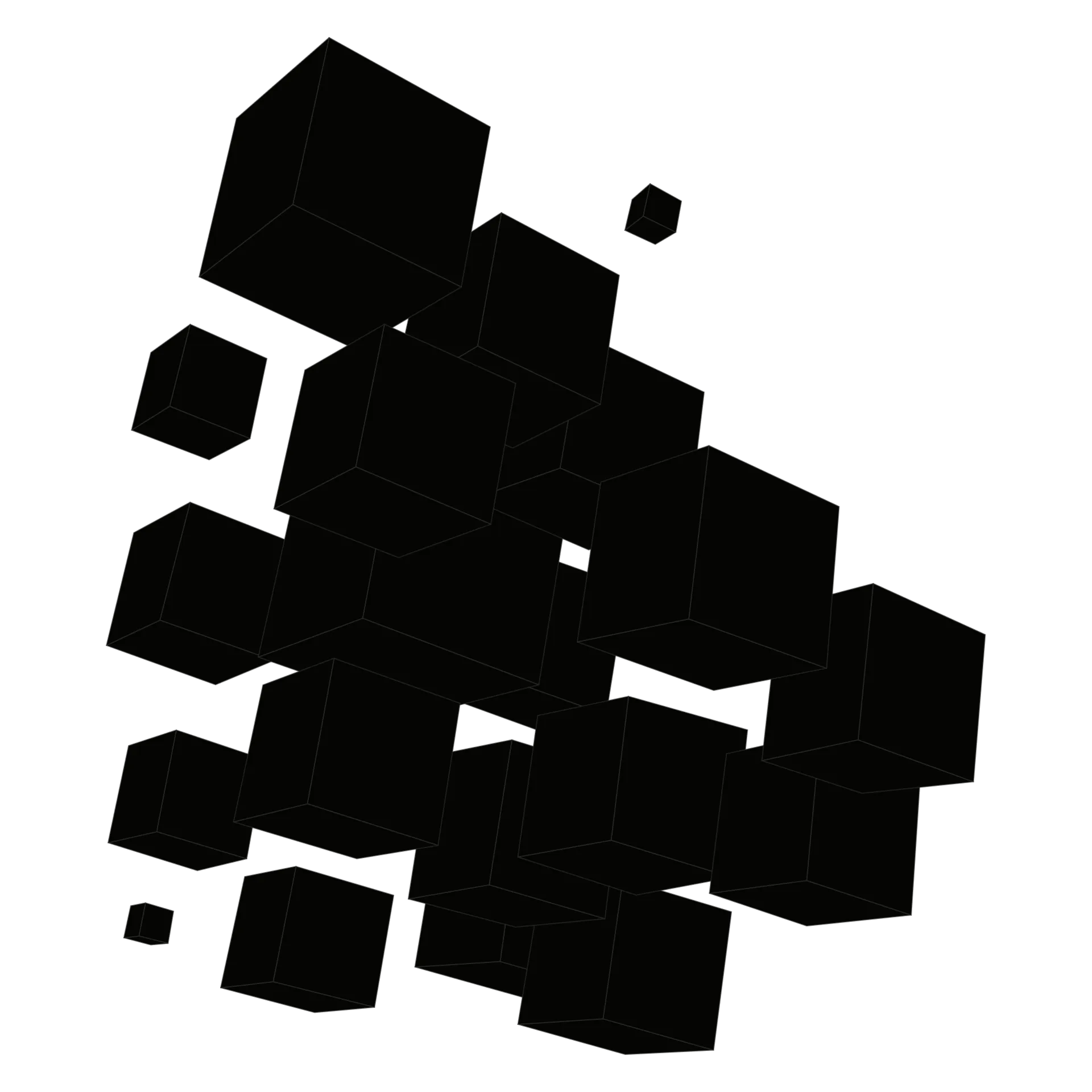
Business First
Code Next
Let’s talk
Benefits of IoT for manufacturing industry
Connected manufacturing helps optimize workflows and cut operational costs.
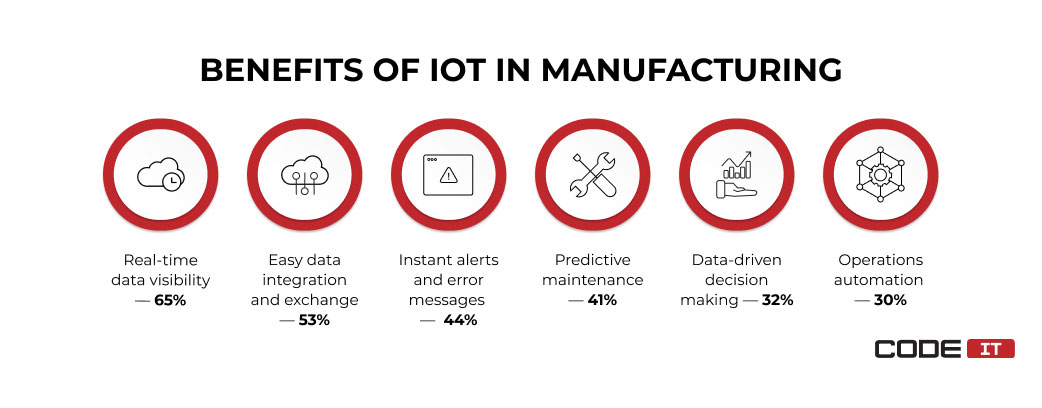
The core benefits of IoT for the manufacturing industry are displayed as observed positive outputs. The benefits are arranged by the average importance highlighted by industry leaders.
1. Real-Time Data Visibility — 65%
Smart devices capture, pre-process, and share data in real time. Hence, stakeholders manage to access information in real-time via a dashboard, including:
- machine status and current program
- production output
- in-stock materials level
- defect rates
- energy consumption
All the data is collected in a centralized repository and visualized for more convenient consumption. Moreover, real-time data can be accessed from any location using cloud-based infrastructure.
2. Easy Data Integration and Exchange — 53%
Cross-system data pipelines enable the opportunity to collect all the data from different sources into a centralized repository. Moreover, the shared database of unified data helps create integrated solutions by connecting software systems from different vendors.
3. Instant Alerts and Error Messages — 44%
Real-time data access and instant analysis help monitor production processes and receive notifications without delay. The error messages and alerts stakeholders can receive include the following:
- machine downtime
- identified defects
- low stock alerts
- safety incidents
- production delays
4. Predictive Maintenance — 41%
IoT solutions for the manufacturing industry help enable proactive machine maintenance. Smart sensors analyze shop-floor equipment, forecasting possible machine failures. Moreover, this approach helps create well-thought-out maintenance schedules to achieve minimum production process disruptions.
5. Data-Driven Decision Making — 32%
The usage of smart algorithms helps receive valuable insights. Businesses can apply AI technology to large datasets for:
- production bottlenecks identification
- demand forecasting
- hidden patterns detection
- optimization strategies development
- improving customer data visibility
6. Operations Automation — 30%
IoT solutions for the manufacturing industry streamline automation because of the opportunity to fetch data from smart devices and issue commands. The development of user agents helps manufacturers to automate bothersome tasks and increase production efficiency.
Enabling IoT for smart manufacturing
Implementing new technologies is the core requirement for integrating IoT devices for manufacturing.
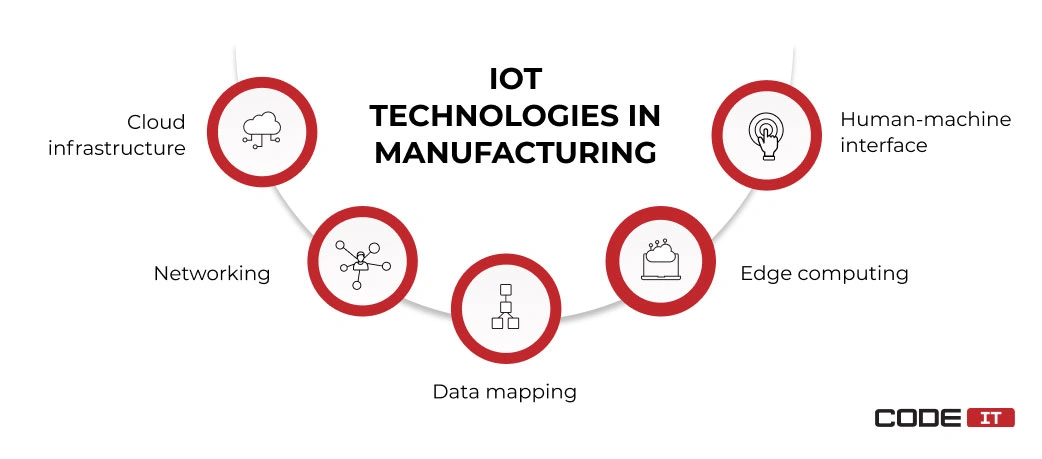
The top five tech solutions businesses need to implement to enable smart production are:
- Cloud infrastructure.
Dedicated servers installed in a remote location and maintained by a third-party vendor. The servers can be accessed remotely from any location via the Internet only. The usage of cloud-based infrastructure helps use resources wisely. Moreover, it enables the opportunity to easily adjust the computing power and storage capacity in a few clicks.
- Networking.
Implementing wired, wireless, or hybrid networks is the core requirement for enabling connected manufacturing. The top technologies used for creating connected factories include Ethernet, WiFi, Bluetooth, and cellular.
- Data mapping.
Machines and IoT devices from different vendors may share data in different formats. Hence, the integration of IoT devices for manufacturing may need to develop and implement additional middleware responsible. It should analyze and transform data in real-time to improve unification and device interconnection.
- Edge computing.
An edge point is a small computing device installed near machines on a shop floor. Edge computing devices preprocess, transform, and filter collected data. The technology helps optimize network traffic by reducing the data transferred to the main server.
- Human-machine interface.
It enables the opportunity for the labor force to effectively communicate with IoT devices. HMI devices help access real-time data, charts, and reports. Moreover, they enable the opportunity for controlling machines and adjusting settings.
Challenges of implementation IoT for manufacturing
The research published on ScienceDirect highlights the business and technical challenges of implementing IoT devices in manufacturing.
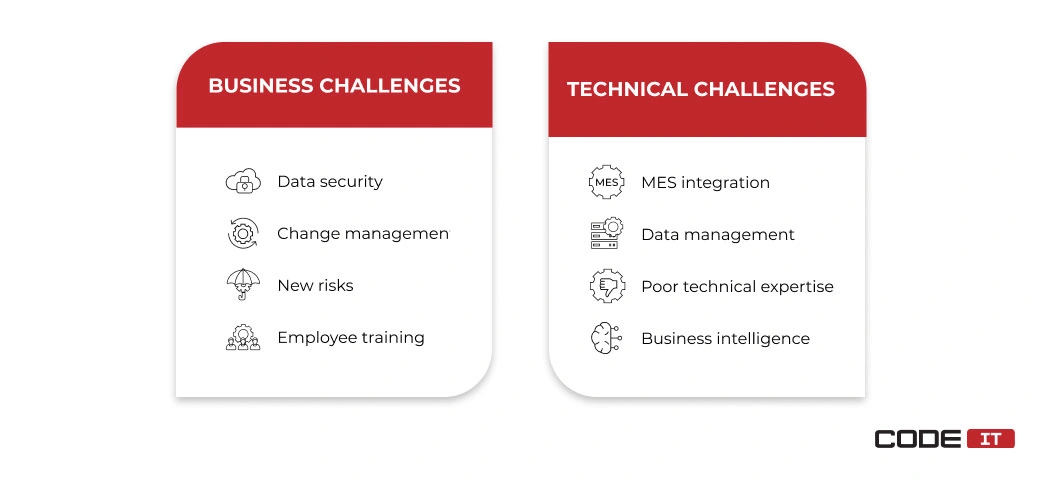
Business Challenges
- Data security.
Many manufacturers are concerned about sharing manufacturing data collected from their shop floors with third parties. Hence, the architectural design should comprise on-premise data processing.
- Change management.
Stakeholders need to develop and introduce new workflows. Moreover, they should create a detailed plan for digital transformation in manufacturing. It can help avoid unplanned downtime when switching to smart manufacturing.
- New risks appear.
The transition to using industrial IoT for manufacturing unleashes the risks of facing new challenges and unforeseen issues. Hence, it’s advisable to develop response plans to the most common risks that occur in the smart manufacturing industry.
- Employee training.
Staff should be educated on the new technologies that have been implemented. Stakeholders must conduct workshops and create a personal learning schedule for each employee. The skills grasped by the staff should be assessed to avoid unplanned production downtime.
Technical Challenges
- MES integration.
IIoT devices and third-party machines should be integrated with a manufacturing execution system (MES). Hence, the developed solution should enable the integration of IoT devices from diverse vendors that share data in different formats.
- Data management.
A business needs to enable an efficient solution for sharing and storing data to use disk space and bandwidth efficiently. Moreover, the implementation of data marts and cross-system data-sharing pipelines may be required.
- Poor technical expertise.
Integrating IoT solutions for the manufacturing industry and developing middleware requires top-tier technical expertise. Skilled specialists need to develop the architecture of a smart shop floor, select the most optimal technologies, and integrate them into an MES.
- Business intelligence.
Large datasets of collected data should be turned into useful insights. Hence, the tech specialists need to implement custom data analysis and visualization algorithms, depending on your business needs.
Wrapping up
The implication of IoT for manufacturing enabled the opportunity to control most processes using a centralized solution. Furthermore, all the data is collected in one repository to extract insights.
The top industrial IoT solutions for the manufacturing industry are:
- Industrial controllers — receive data and issue commands.
- Sensors — monitor environments and detect items.
- Scanners — read barcodes, inspect item surface and composition.
- Cameras — detect objects and packages, monitor production processes.
- Actuators and smart robots — repetitive tasks automation and human assistance.
The foremost applications of IoT for smart manufacturing include the following:
- Read time data collection
- Data analysis and forecasting
- Workflow automation
- Energy consumption optimization
- Production quality control
- Inventory management
- Predictive maintenance
- Environment monitoring
Hire us to revamp your production with IIoT
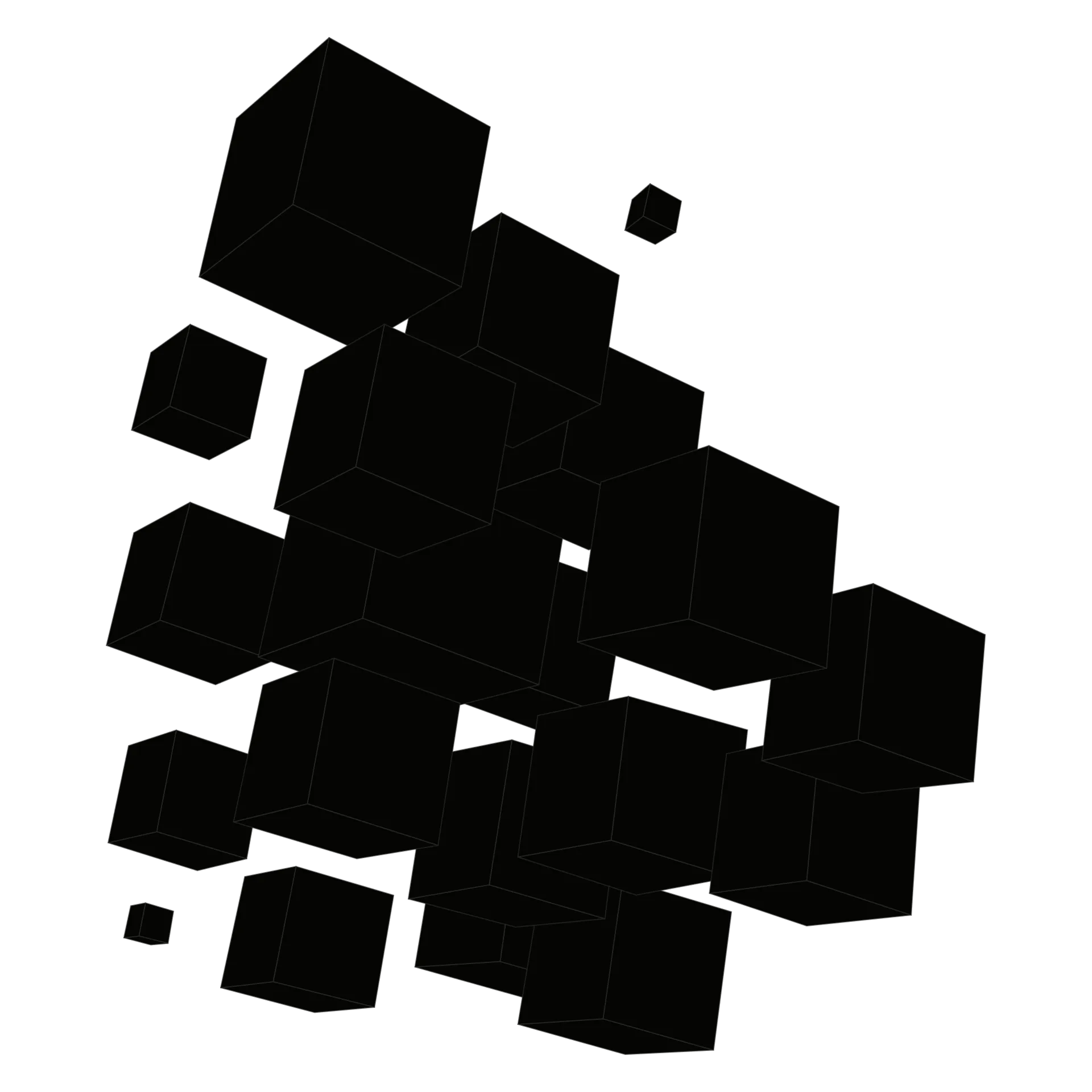
Business First
Code Next
Let’s talk
FAQ
The Industry 4.0 term defines the usage of smart devices and digitalization. In Industry 4.0, everything is connected. Interconnected smart (IoT) devices help collect and share data in real-time.
Real-time visibility is the #1 application of industrial IoT.
Example: a manufacturing company collects data from machines and smart devices. All the data is displayed on a dashboard in live time.
Industrial IoT for manufacturing helps automate bothersome and repetitive tasks. Moreover, smart devices help reduce the number of errors and detect defects accurately.
For example, Siemens has installed more than 1,000 manufacturing automation controllers and managed to automate roughly 75% of operations at its electronics manufacturing plant in Amberg, Germany.
The deep analysis of collected data helps identify bottlenecks and points of growth.
For instance, Ford Motor Company has increased production efficiency by 10% by applying ML-driven algorithms. These algorithms analyze data about cycle times and robot performance.
Schneider Electric is an electronics company that utilizes AI-driven cameras that visually inspect produced items to detect defects automatically. All the information is transferred to the main server in real-time and displayed on a dashboard.
Business challenges:
- Data security
- Change management
- New risks appear
- Employee training
- MES integration
- Data management
- Poor technical expertise
- Business intelligence
Technical challenges:
- Data security
- Change management
- New risks appear
- Employee training
- MES integration
- Data management
- Poor technical expertise
- Business intelligence
Build your ideal
software today
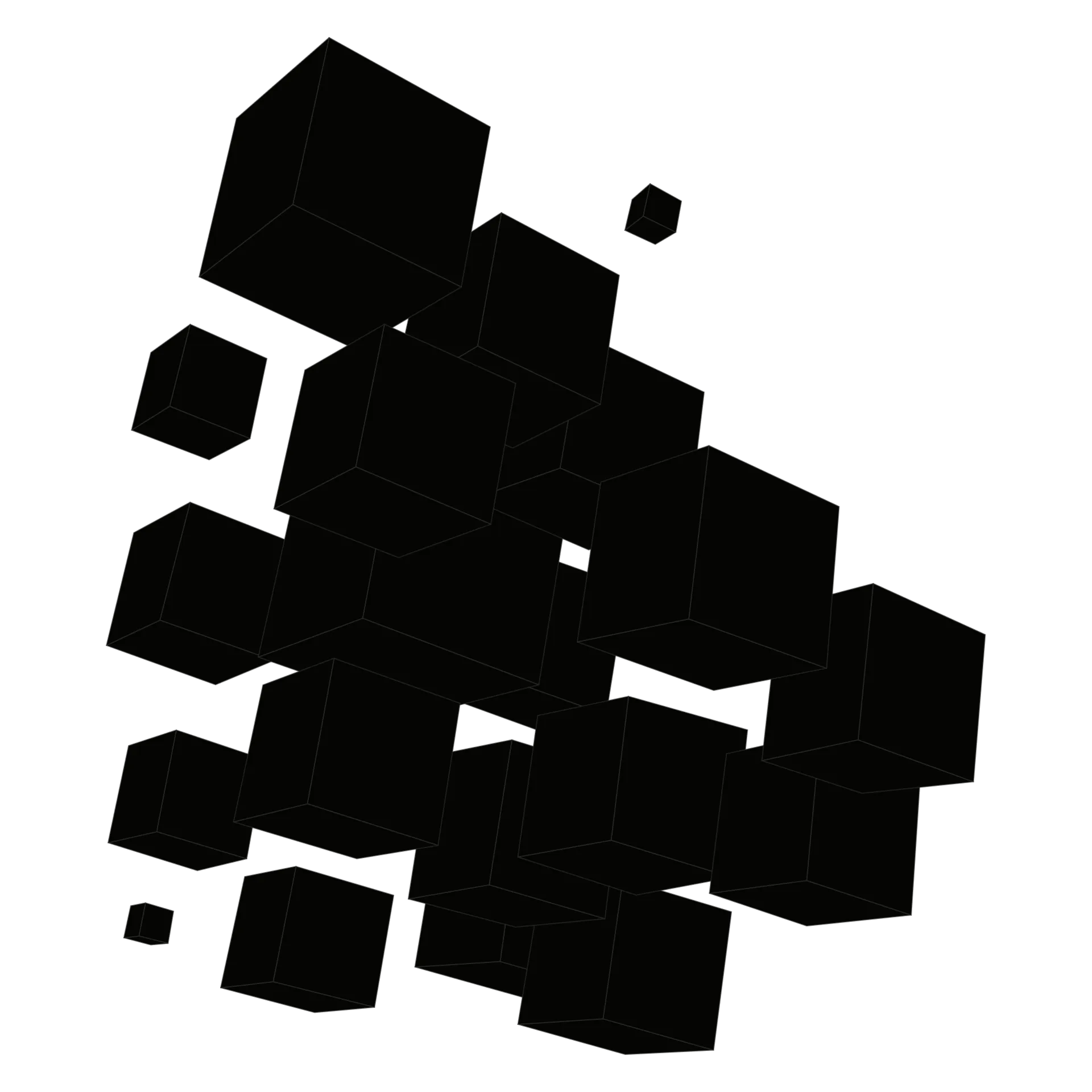