ERP & MES Integration — Industry 3.0/4.0 Approaches
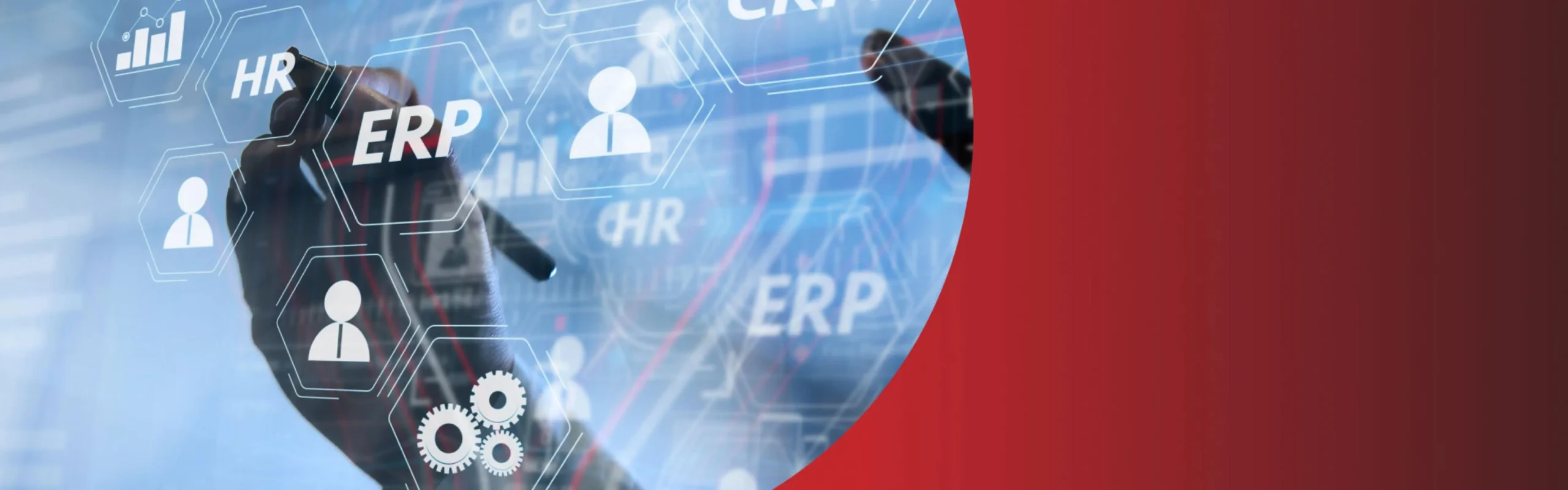
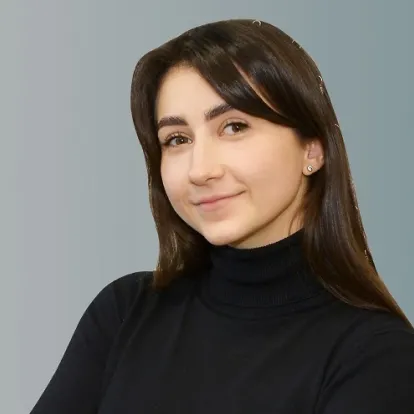
An enterprise resource planning (ERP) system enables organizations to manage business processes. A manufacturing execution system (MES) is responsible for managing production processes in industrial companies.
The MES & ERP integration provides a centralized view of all the processes in a defined:
- enterprise
- site
- area
- production line
Stakeholders can access all the business and manufacturing data using the MES and ERP integration. The seamless flow of information between systems helps achieve:
- real-time visibility
- data-baked decision-making
- improved collaboration
- optimized quality control
- reduce errors
MES & ERP Integration Approaches
The foremost ways to connect ERP and MES systems are categorized by Industry 3.0 and 4.0 approaches.
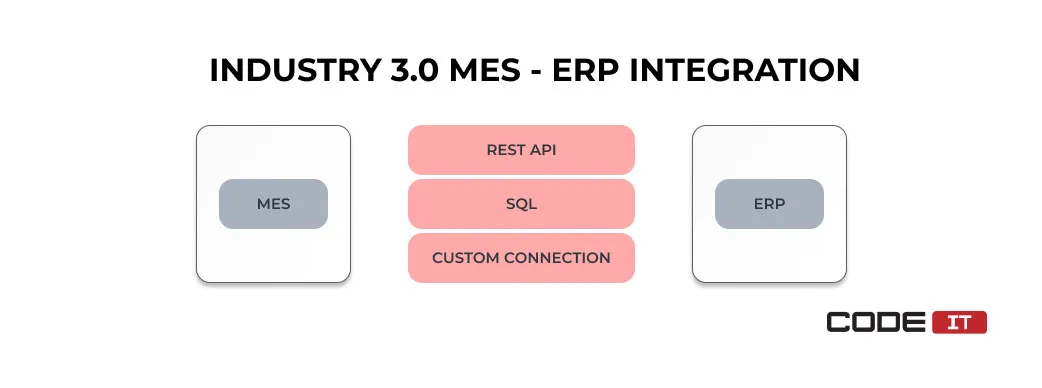
Industry 3.0 Integration
The industry 3.0 integration approach heavily relies on creating custom connections between ERP and MES systems, including:
- REST API. Trigger-driven calls for information from an MES system via REST API interface.
- SQL request. Custom SQL connections should be developed using Microsoft Open Database Connectivity (ODBC), Java Database Connectivity (JDBC), or any other interface.
- Custom connection. A point-to-point connection for information transfer via FTP. The ERP system needs to request and the MES systems have to reply providing the requested data.
The main drawback of the Industry 3.0 approach for MES integration with ERP is that all the connections are created manually. They are built to conduct specific actions and must be updated if any parameters change. It makes the architecture complicated and inflexible.
Moreover, software engineers must clearly understand the ERP and MES integration architecture. They must know how tables are structured, what they are looking for, and where they are located.
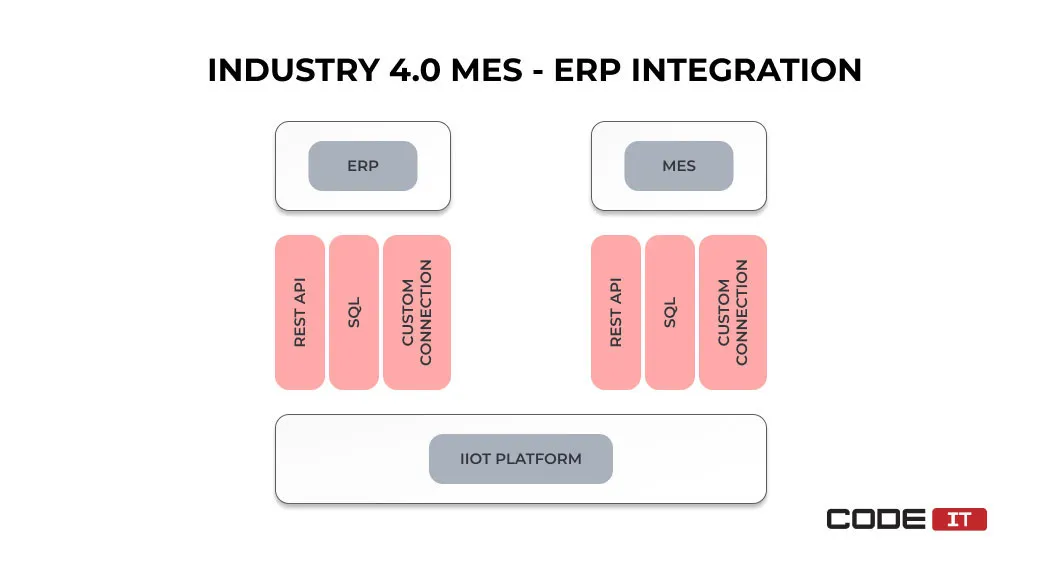
Industry 4.0 Integration
The Industry 4.0 MES system integration approach promotes the creation of a functional namespace, a shared directory for ERP and MES data.
An IIoT platform connects ERP and MES software and fetches all the information. The ERP and IIoT software are integrated using REST API, SQL request, or any other connector. When the data model in an ERP extends, the IIoT-driven connection is automatically retrieved and put into the namespace. Besides, the collected data can be pre-processed or transformed upon a need.
The usage of a namespace enables the opportunity for an ERP to monitor for changes by setting a subscription. Both ERP and MES systems are not limited to custom connections. They get access to the full data collected by each solution in a unified namespace.
Also, software engineers can develop custom functions to automate manufacturing processes. For instance, when an MES starts a new program, it fetches product information from the ERP data in the namespace.
Hire CodeIT to pick best approach for your business
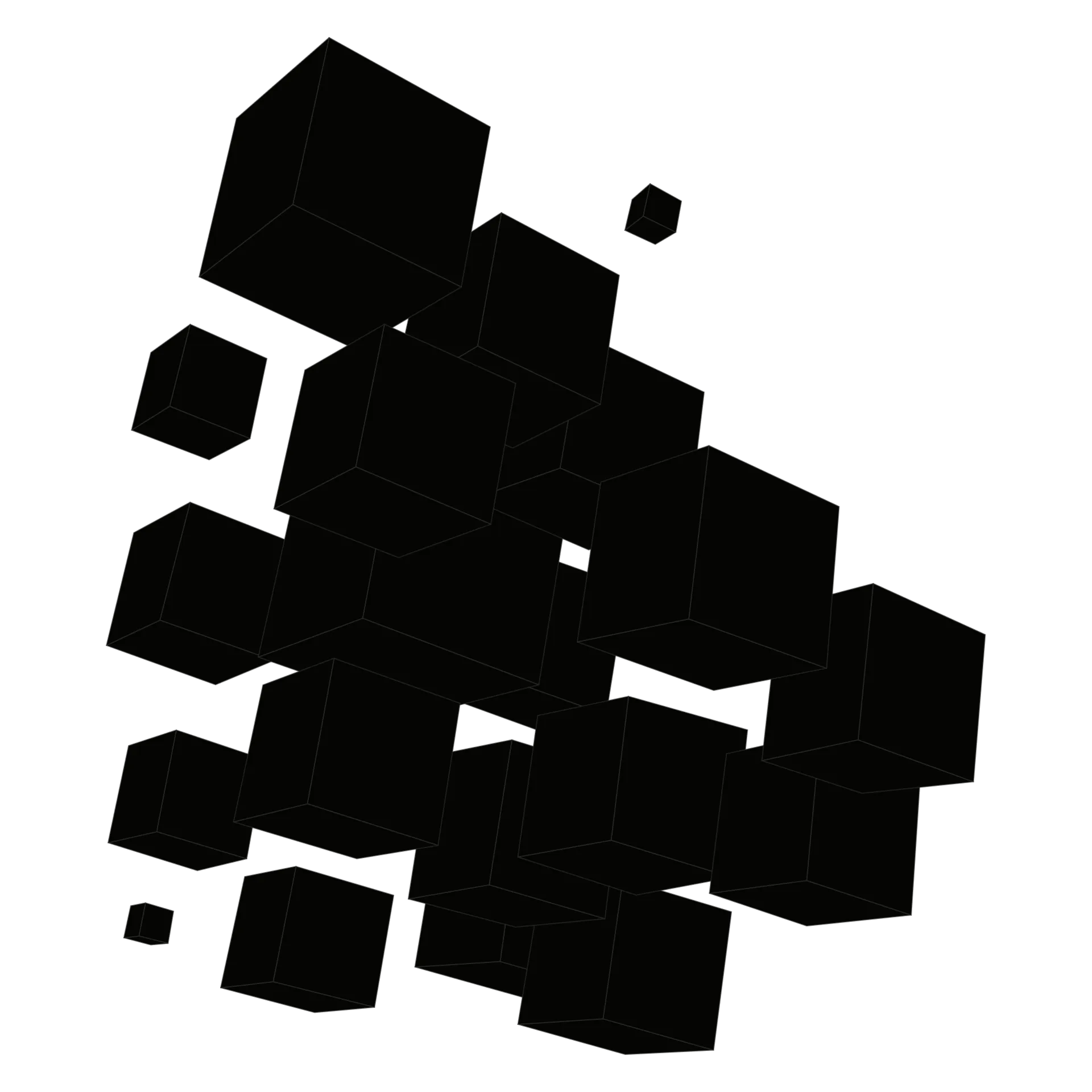
Business First
Code Next
Let’s talk
ERP, PLM & MES Integration Steps
The integration of MES, EPR, and other operational technologies is a custom process that depends on many factors, with the following key steps.
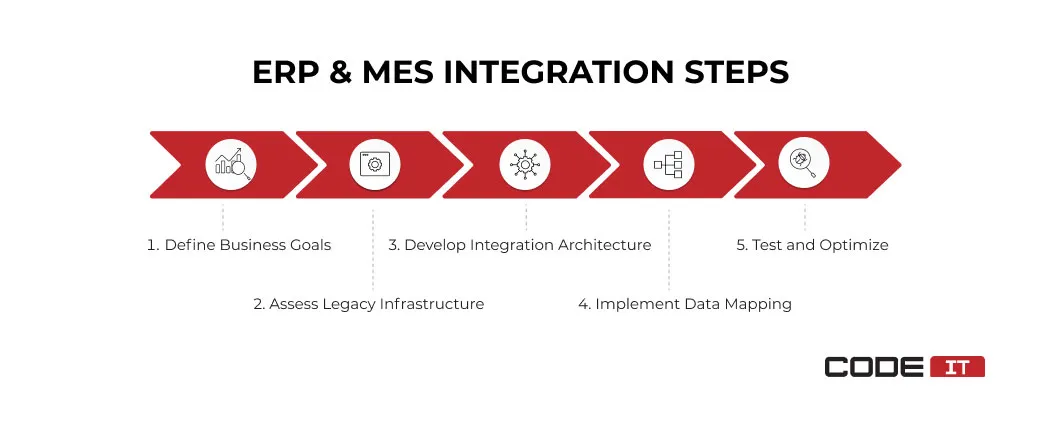
1. Define Business Goals
Clearly outline business requirements to understand what you want to achieve. Understand what information needs to be shared between MES and ERP systems. Also, define what processes should be improved/automated as a result of cross-system data pipelines development.
2. Assess Legacy Infrastructure
You need to assess the existing infrastructure to understand technical limitations. Check out the supported technologies to understand if additional middleware should be developed.
3. Develop Integration Architecture
Create the architecture of the MES & ERP integration and choose the best technologies to implement. Select the integration approach by considering the legacy architecture.
Develop custom connections for Industry 3.0 or implement an IIoT infrastructure along with a functional namespace for the Industry 4.0 approach.
Note that it’s crucial to enable users to create custom KPIs using the MES/ERP integration. Hence, stakeholders can test new manufacturing process optimization strategies and measure outputs in real time.
The infrastructure should comprise record-keeping functionality to check any parameter at any recorded time.
4. Implement Data Mapping and Transformation
The development of additional middleware and infrastructure is required for enabling communication between ERP and MES systems. Create custom data mapping tools for validating and transforming transactional and event-based data received from MES/ERP systems.
5. Test and Optimize MES & ERP Integration
Launch the MES integration with ERP in a real production environment and check the performance of custom connectors or functional namespace. Check the fetched/shared data to ensure it is transformed correctly.
Optimize data-sharing pipelines to reduce the bandwidth and amount of computing power required to process all the information.
The implementation of event subscription is one of the most effective ways to optimize the performance of ERP, PLM, MES integration. New data is sent and recorded only when the value is changed.
Benefits Of ERP & MES Integration
The implementation of product lifecycle management (PLM), ERP, MES integration helps streamline processes and automate operations by creating custom functions.
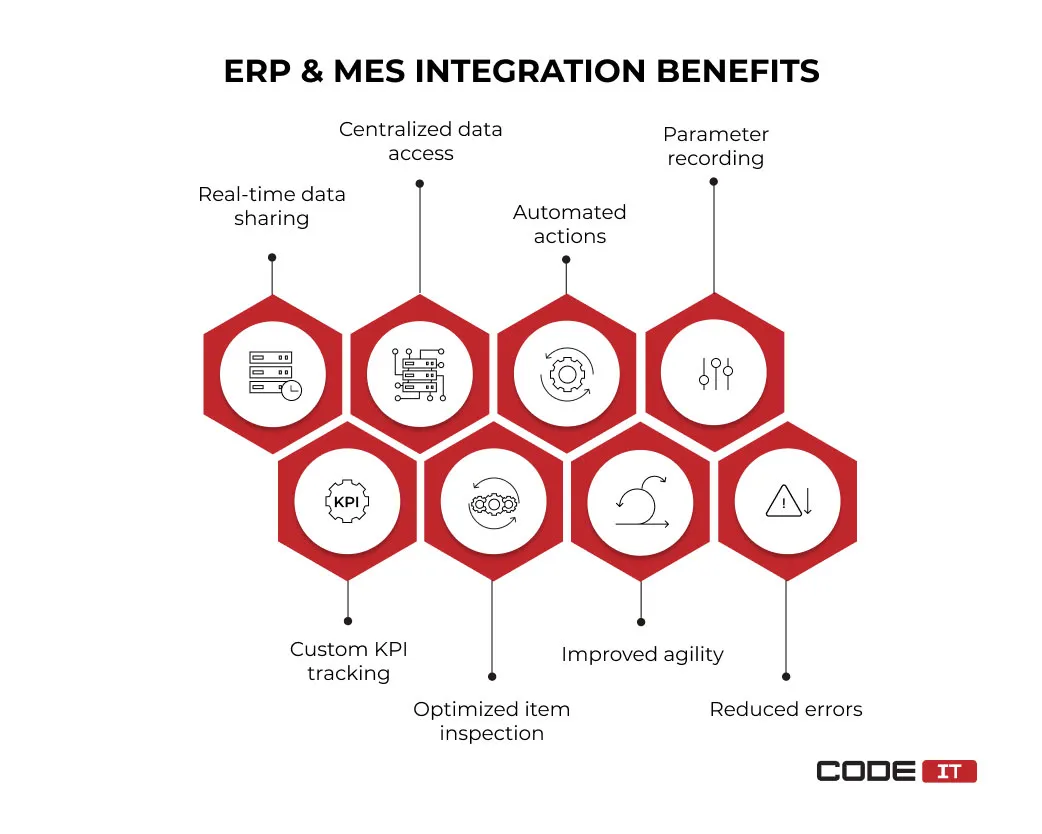
The core benefits and ROI gains are the following:
- Real-time data sharing. 20% increase in inventory and material control.
- Centralized manufacturing data access. 70% increase in the accuracy of shift KPIs.
- Automated actions. 85% reduction in manual data collection and analysis.
- Parameter recording and analysis. 70% reduction in planning and research challenges.
- Custom KPI tracking. 17.5% increase in efficiency of work sequence control.
- Optimized item inspection. 75% reduction in manual QA inspection efforts.
- Improved agility. 17.5% improvement is setup time.
- Reduced errors. 40% reduction in manufacturing data errors.
Let’s check the positive outcomes of implementing MES and ERP integration by comparing manufacturing operations with and without integration.
No ERP/MES Integration | ERP/MES Integration | |
---|---|---|
Data Visibility | Isolated solutions should be used to get shop floor and business information. | Real-time data is collected and transferred to the central server. Business intelligence (BI) systems help visualize manufacturing data. |
Production Scheduling | Labor force gets information from isolated solutions and schedules production manually. | All the available production data is collected in a central repository. Production planning & scheduling is conducted automatically. |
Machine Program Configuration | All the parameters, product codes, and other data should be input manually by the labor force. | Automated machine program configuration using ERP-MES data-sharing pipelines. |
Order Processing | Manual coordination between sales, manufacturing, distribution, and other departments. | Sales information is automatically transferred to manufacturing and distribution departments via the MES-ERP integration. |
Quality Control | Produced items are inspected manually, or quality data is processed with a delay using an isolated solution. | Automated data collection, sharing, and processing enables real-time item quality monitoring. Shop floor staff are notified in real time when defects are detected. |
Reporting and Data Analysis | Data is fetched manually from isolated solutions and proceeds using third-party software. | Manufacturing and business data is automatically collected and processed by business intelligence (BI) solutions. Custom reports can be composed and shared automatically. |
CodeIT Expertise
Our team has implemented a comprehensive solution for monitoring machine uptime. Also, we’ve integrated it with the existing MES solution.
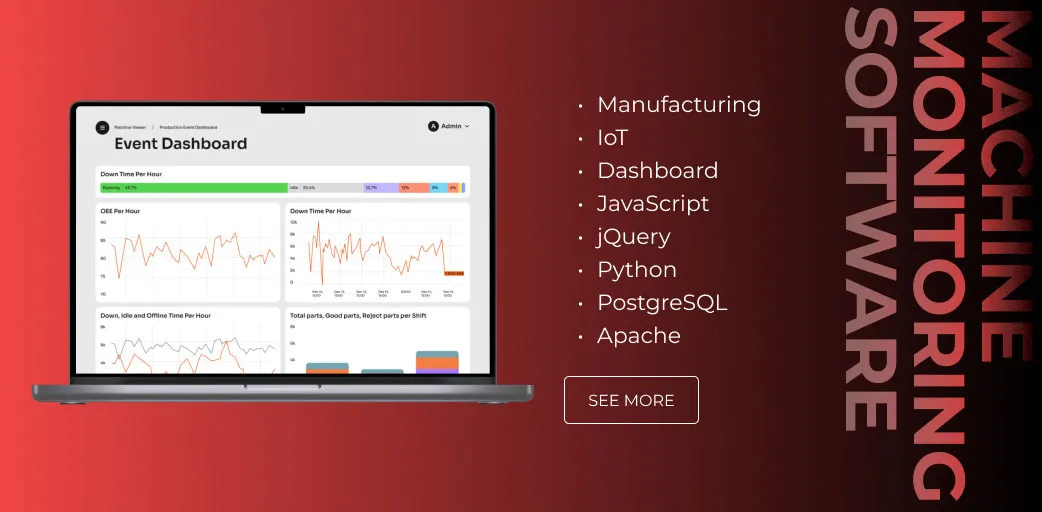
Problem
The client lacked visibility of manufacturing processes and shop floor control. He wanted the information to be automatically processed and visualized. Moreover, the client wanted to enable centralized control over operator permission control.
Implementation
Our team has started from the very beginning and delivered a fully functional solution. The core system implementation stages included the following:
- Analysis and tech stack selection
- Product development planning
- Team onboarding
- Solution development
- Testing and optimization
- Software integration
Result
Our team of software engineers, BAs, QA specialists has developed a fully functional machine uptime monitoring software comprising the following features:
- Dashboard with detailed machine information
- Live-time manufacturing data visualization
- Custom report generation
- Machine status viewer
- System permission configuration
Machines Uptime Monitoring Software
Conclusion
The MES & ERP integration defines the connections between two systems that enable seamless data flow.
The integration can be implemented via two approaches:
- Industry 3.0 — the development of custom connections between systems. The connections need to be manually updated when new changes in data structure are made.
- Industry 4.0 — the creation of a shared data integration repository. It enables the opportunity to create custom functions to implement new changes efficiently.
The ERP-PLM-MES integration can be implemented in five key steps that are:
- Business goals identification
- Legacy infrastructure assessment
- Integration architecture development
- Data mapping and transformation implementation
- Testing and optimization
The key benefits of MES and ERP integration include:
- Real-time data sharing
- Centralized manufacturing data access
- Automated actions
- Parameter recording and analysis
- Custom KPI tracking
- Optimized item inspection
- Improved agility
- Reduced errors
FAQ
The MES integration with ERP defines the data flow between the systems and custom algorithms that trigger actions. It enables improved processes visibility and automation.
The ERP, PLM, MES integration can be enabled via different ways, depending on legacy infrastructure limitations and business requirements.
The most popular ways to implement MES-ERP integration are as follows:
- custom connections
- API integration
- SQL request
- Functional namespace
The five foremost steps of MES system integration are:
- Business goals identification
- Legacy infrastructure assessment
- Integration architecture development
- Data mapping and transformation implementation
- Testing and optimization
The return on investment for the MES and ERP integration are:
- 20% increase in inventory and material control
- 70% increase in the accuracy of shift KPIs
- 85% reduction in manual data collection and analysis
- 70% reduction in planning and research challenges
- 17.5% improved efficiency of work sequence control
- 75% reduction in manual QA inspection efforts
- 17.5% improvement is setup time
- 40% reduction in manufacturing data errors
The benefits of MES integration include the following:
- Real-time data sharing
- Centralized manufacturing data access
- Automated actions
- Parameter recording and analysis
- Custom KPI tracking
- Optimized item inspection
- Improved agility
- Reduced errors
Build your ideal
software today
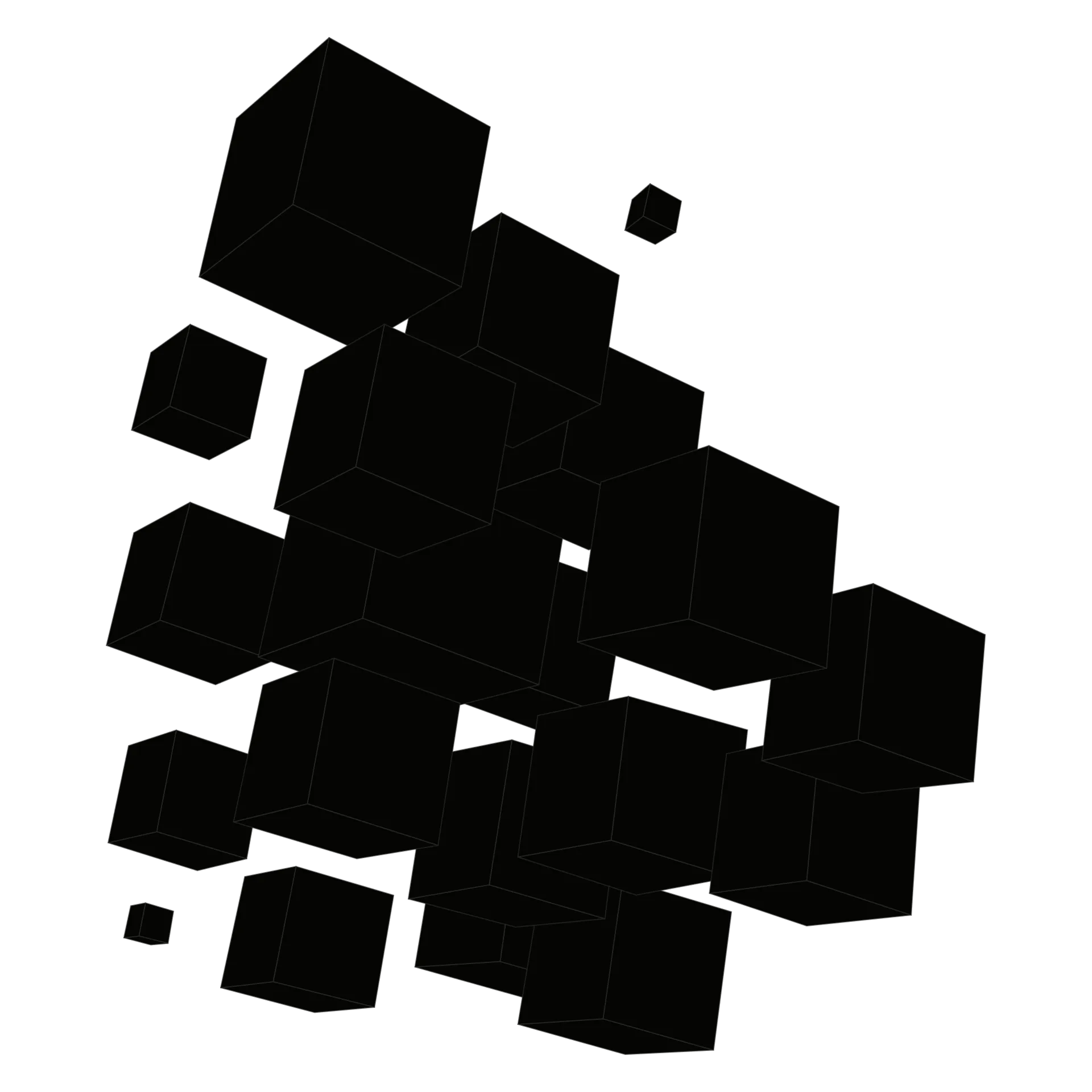