Inventory Management System Features
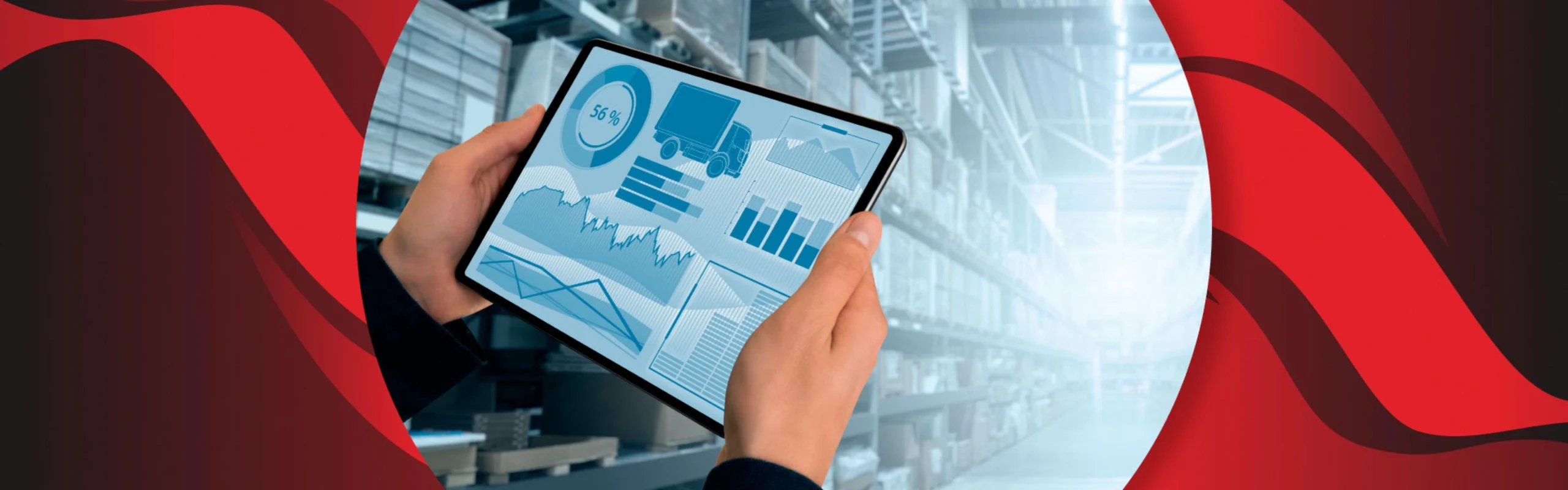
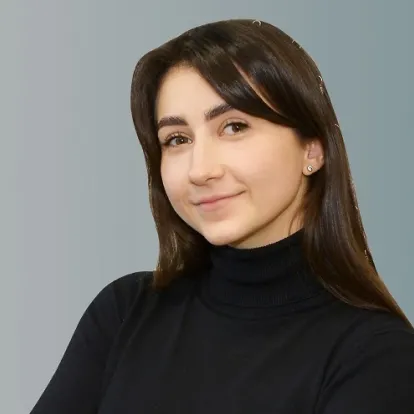
Inventory management software is a new-era replacement for spreadsheets. Feature-rich systems help run smart inventory management strategies and optimize processes.
There are tons of out-of-shelf systems with a wide assortment of features available. Yet, only about 60% of inventory management software features are used by an average business. Roughly 40% of functionality remains unused.
It’s vital to develop software that comprises the inventory management system features a business needs to avoid wasting resources when developing a new solution.
Find the selection of the key and advanced features to implement during inventory management software development below.
Key Features | Advanced Features |
---|---|
1. Inventory tracking | 1. Automated re-ordering |
2. Identifiers issuing and scanning | 2. Third-party software integration |
3. Order management | 3. Multi-location inventory management |
4. Item storage management | 4. Demand forecasting |
5. Reports and analytics | 5. IoT-driven inventory management |
6. Backup and data import/export | 6. Automated item quality check |
7. Automated workflows | |
8. Bundles and multiple price tiers |
Let’s elaborate on the core and advanced features to implement. Discover problems they help solve and how these features are applied.
Six key features of inventory management system
The vital inventory management software features help enable the basic functionality of new software. They help track items in a warehouse, manage orders, and access analytics.
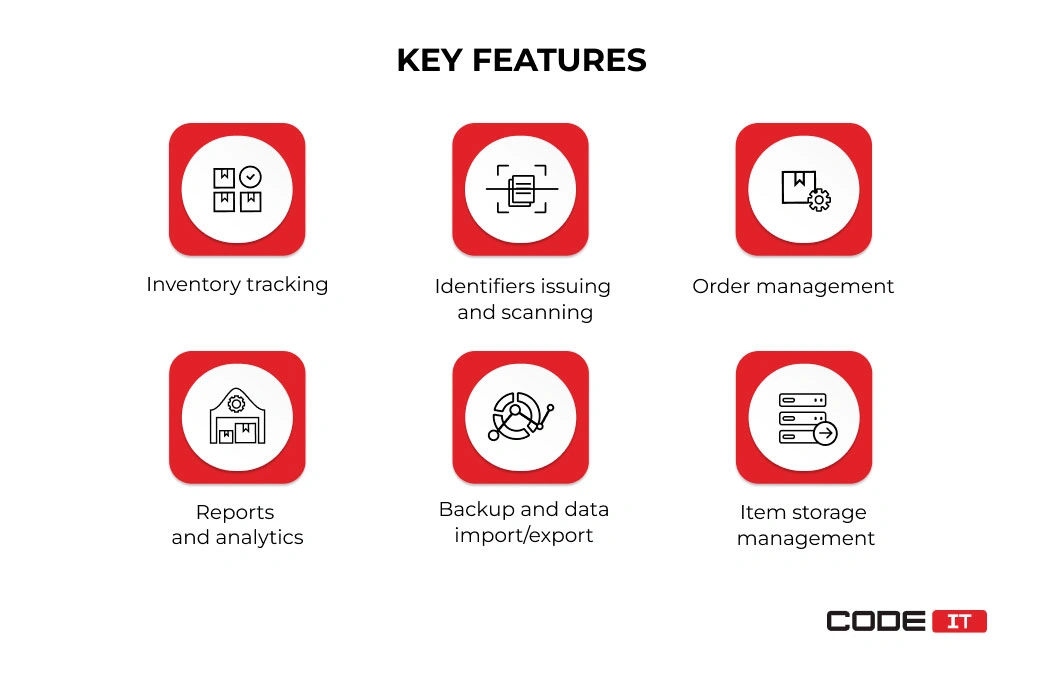
1. Inventory Tracking
Track the location and movement of items in a warehouse. The feature enables an inventory management system to record information about the placement of items, their quantity, and transfer history.
By updating items’ location data in live time, you can trace work-in-progress (WIP) products. An inventory management system alerts responsible managers when the in-stock level reaches a defined minimum value. Also, this feature of an inventory management system helps track the expiry date of perishable products.
Statistics: 95% of businesses consider inventory tracking as a critical feature.
Feature applications:
- Real-time serial number tracking—track the movement of each item in a warehouse, providing instant updates on their location, status, and movement.
- Stock level monitoring—stay updated about the actual inventory levels updated in real time. Helps prevent overstocking or stockouts by eliminating cycle counting and information update delay.
- Location tracking and movement history check—access the movement history of each item, gaining detailed insights on inventory flow across multiple sites.
- Missing items identification—get missing or misplaced items highlighted to rapidly resolve inventory discrepancy issues.
- Expiry date tracking—ensure perishable products are processed timely to reduce waste and identify items needing disposal.
Problems solved:
- Poor inventory visibility
- Manual item counting
- Stockout and overstocking
- Erroneous inventory data
- Increased product wastage
2. Data Backup and Import/Export
Ensure data safety and enable fast recovery after unforeseen data losses. Import/export inventory data in bulk to rapidly migrate information between different systems in a supply chain. Validate and transform data to ensure its integrity for creating information exchange pipelines.
Statistics: 90% of businesses define data backup and import/export as the baseline functionality.
Feature applications:
- Full and incremental backup—save all the data in bulk or backup only the new records, saving the last changes made.
- Data check and validation—automatically analyze the integrity of backup files, ensuring no records are broken or comprise missing data so that backed up data can be successfully recovered in the future.
- Automated data backup and recovery—schedule automated backup creation and streamline data recovery processes to eliminate the need for technicians to be involved in running manual activities.
- Inventory data import and export—transfer backed-up data between systems and import records from other systems or isolated solutions in bulk.
- Data transformation—Convert inventory data into compatible formats during backups or transfers, ensuring smooth integration with various systems and applications.
Problems solved:
- Data loss
- Manual backup creation and management
- Poor information integrity
- Insufficient data-sharing capabilities
- Manual product information entry
3. Identifiers Issuing and Scanning
Create identifiers in the form of barcodes, QR codes, RFID tags, or SKU codes. Quickly scan packages to discover detailed information about items. Various equipment like barcode scanners, cameras, or smartphones can be used for scanning labels.
Data encoded into barcodes can be automatically fetched and input into an inventory management system. It helps enhance order fulfillment accuracy and performance.
Statistics: 87% of businesses identify efficient product identification as an important feature.
Feature applications:
- Product scanning and information update—use barcode or QR codes to check-in items in a certain location or instantly retrieve information about product details and update relevant inventory information in real-time.
- Automated data entry and data forms pre-population—make all the available data automatically filled by a computer. It helps reduce the need for manual input and increase the accuracy of entered data.
- Identifier code generation and label printing—generate unique codes for each item to make custom databases to avoid using isolated solutions from different vendors.
- Item movement tracking—get real-time updates on items’ location by implementing automated barcode scanning.
- Product identification for order collection—instantly get data about items and it to third-party systems to locate products for order fulfillment fast.
Problems solved:
- Data entry errors
- Time-consuming or inaccurate order fulfillment
- Insufficient product identification
- Poor item traceability
- Manual inventory audit
4. Order Management
Use a centralized system to collect and fulfill orders. The feature enables the opportunity to check in-stock inventory and discover the location of items to pick and pack rapidly. Trace the delivery of packages and manage returns effectively.
Also, this inventory management system software feature enables the opportunity to reserve items in a warehouse and track the status of orders.
Statistics: 84% of businesses state that order management is an obligatory-to-have feature.
Feature applications:
- Order processing—streamline the handling of incoming orders, from placement to fulfillment, ensuring efficient and accurate processing.
- In-stock inventory check and reservation—automatically verify all the requested items are available before you accept an order and start fulfilling it.
- Order confirmation and tracking—automate workflows to provide clients with instant order confirmations and real-time tracking updates.
- Customer communication—keep customers informed about order fulfillment by automating processes and sending automated updates and request responses.
- Automated returns processing—seamlessly manage product return processes by automatically updating records.
Problems solved:
- Time-consuming order processing
- Order processing delays caused by stockout
- Return-handling mistakes
- Manual order status tracking
- Human errors
5. Storage Management
Organize storage space and enable smart item placing to minimize the efforts and time required to pick and pack items. Easily discover the physical location of inventory. Besides, this inventory management system feature helps meet storage environment conditions requirements.
Statistics: 82% of businesses identify asset tracking features as critical functionality.
Feature applications:
- Storage rules and policy creation—optimize space utilization and inventory flow by integrating instructions for employees and checking if all the requirements are met.
- Space reservation for production—hold storage space for items that are in production to avoid any issues with the lack of storage space.
- Guided item placement—provide clear instructions and issue live-time recommendations to help employees pick the right items.
- Items’ physical location identification—quickly identify and locate stored items by tracking their exact physical position.
- Smart stock rotation—enable automatic stock rotation practices like “first in, first out” to minimize wastage.
Problems solved:
- Insufficient storage space utilization
- Item location challenges
- Improper storage conditions
- Time-consuming order picking and packing
- Inventory misplacement
6. Reports and Analytics
Collect all the data across a supply chain and extract valuable insights. Automatically create reports and visualize raw data. Also, the feature enables the opportunity to create data analysis pipelines to check inventory data in live time.
Statistics: 81% of businesses state that analytics is a key functionality of an inventory management system.
Feature applications:
- Data collection and storage—collect data from multiple sources and store it in one place. Avoid using isolated solutions and diverse data analysis tools.
- Information analysis—turn raw data into actionable insights for decision-making and optimize operations.
- Data visualization and custom report generation—create customized dashboards to quickly access the most relevant data and alerts.
- Dashboards and live-time data update—enable live-time data sharing to instantly get important alerts and monitor changes in real time.
- Trend and error identification—automatically detect errors in the data, helping identify potential issues and optimize performance over time.
Problems solved:
- Poor supply chain management and visibility
- No real-time data
- Lack of data-driven decisions
- Improper inventory replenishment planning
- Manual report creation
Let’s build MVP with baseline features
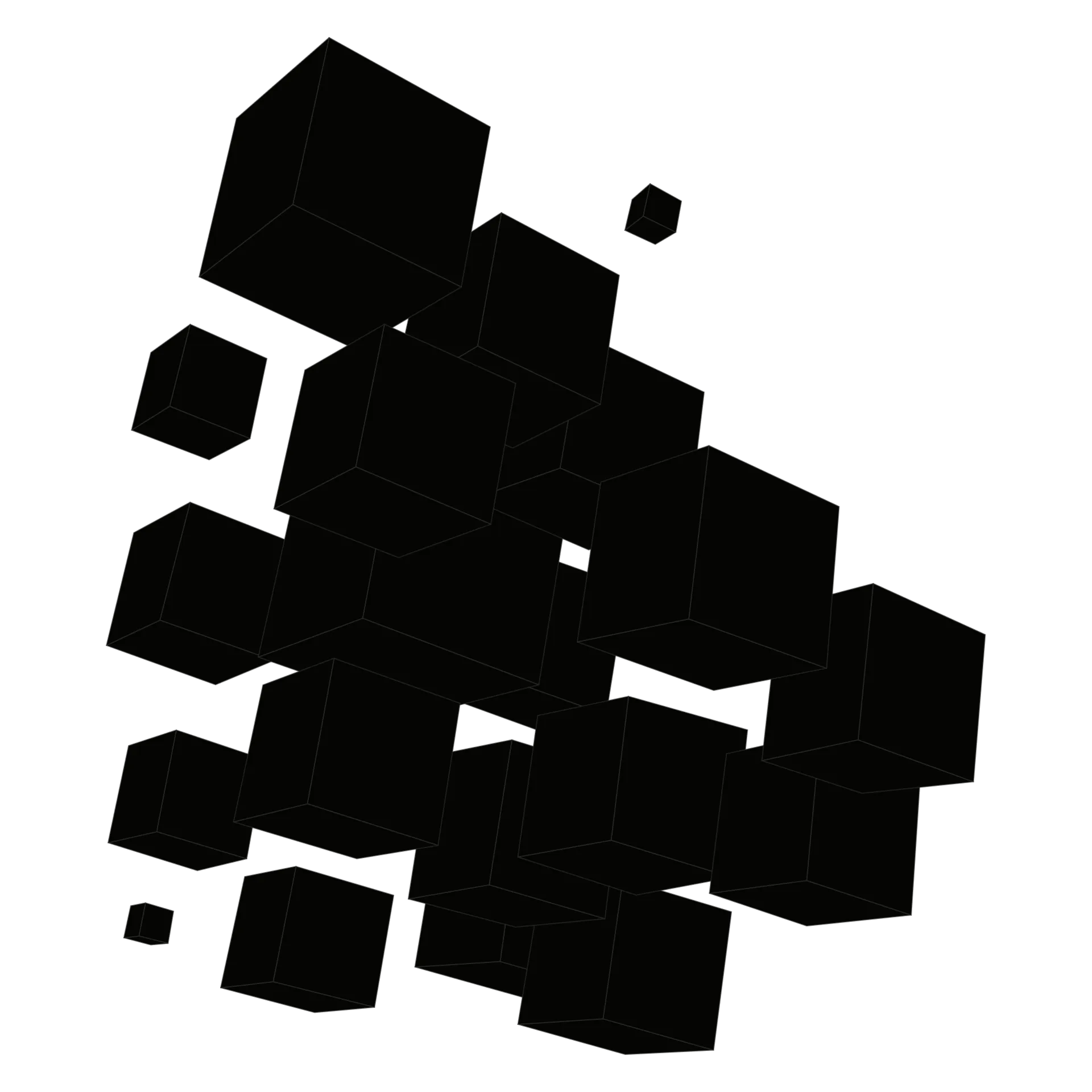
Business First
Code Next
Let’s talk
Eight advanced inventory management system features
Improve your inventory management system by supplementing it with top-tier inventory management software features.
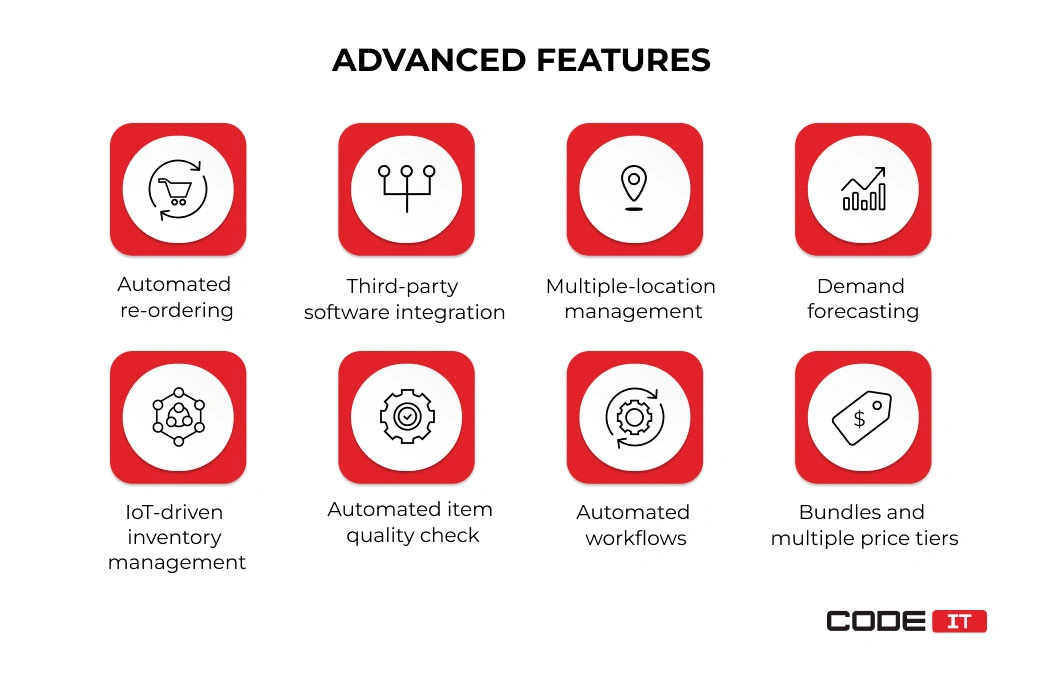
1. Automated Re-Ordering
Replenish items automatically to maintain the optimal level of inventory in a warehouse. The feature monitors in-stock inventory and triggers automatic product re-ordering. It helps create replenishment requests that are sent to suppliers once approved by executing managers.
Also, the feature helps enable a vendor-managed inventory replenishment system. A supplier monitors the level of in-stock inventory. When it reaches the minimum required value, a vendor automatically delivers a new batch of products.
Feature applications:
- Re-order points configuration—set custom rules that trigger notification issuing when a certain threshold is met.
- Automated stock level monitoring—automatically initiates re-orders when the stock falls below predefined thresholds.
- Order review and approval—manually review and approve each new order created by an automated system or employees.
- New orders tracking and management—check the status of each order, ensuring timely updates and smooth processing.
- Vendor communication—streamline vendor communication by developing tailored tools and automated data-sharing pipelines.
Problems solved:
- Stockout and overstocking
- Manual new order submission
- Data entry errors
- Manual stock-level monitoring
- Poor supplier management
2. Demand Forecasting
Apply algorithms or use machine learning models to forecast trends and demand changes by analyzing historical data. Avoid stockout by preparing for demand spikes and seasonal changes in advance. Smart adjustments of inventory replenishment strategies help decrease the wastage of perishable products.
Feature applications:
- Demand change forecasting—analyze historical data to predict future demand that may depend on seasonality, holidays, and other external factors.
- Identification of trends and repeating patterns—adjust your inventory strategy by identifying trends and hidden patterns.
- Risk identification—detect potential risks, such as supply shortages or overstocking, to proactively address inventory management challenges in advance.
- Market insights discovery—access market insights by analyzing external factors to prepare your business for future changes.
- Replenishment strategies optimization—align stock levels with forecasted demand to optimize your replenishment strategies.
Problems solved:
- Stockout and overstocking
- Insufficient item replenishment strategies
- Lack of information on seasonal and repetitive demand changes
- Increased product wastage rate
- Faulty market analysis
Forecasting In Supply Chain: Methods, Examples, and Instruction
3. Third-Party Software Integration
Develop an integrated inventory management system by connecting software from different vendors. Fetch orders and inventory data from different platforms and process it in live time using this inventory management system feature. Besides, you can enhance the functionality of a system by connecting additional modules.
Feature applications:
- Inventory management system functionality extension—extend the functionality of your existing software solutions by integrating third-party software.
- Centralized inventory data fetched from multiple systems—gather inventory data from various sources into a single, centralized platform, getting a unified view.
- Automated data pipeline creation—automatically transfer data between systems and collect records from various sources in one place.
- Real-time information synchronization—ensure inventory data updates in one system get automatically reflected in other connected solutions to avoid possible misunderstandings.
- Centralized order processing and tracking—use a single solution to track all the operations, monitor orders, and update data.
Problems solved:
- Ineffective workflows
- Isolated data in disparate platforms
- Manual data collection from different systems
- Limited functionality of inventory management software
- System scaling up challenges
4. Multiple Storage Facilities Management
Manage inventory stored in multiple warehouses. Choose the most optimal storage facility to fulfill and deliver orders fast, based on clients’ locations. Enable full visibility across multiple facilities using a centralized warehouse inventory system.
Besides, the functionality enables easy submission of transfer requests and automated multi-storage inventory management operations.
Feature applications:
- Cross-docking stock transfer requests—facilitate quick stock transfers between warehouses or locations without long-term storage.
- Centralized inventory visibility—collect inventory data from multiple locations on one server and access it whenever you need from any office.
- Multi-location items picking, packing, and replenishment—enable smart coordination of order fulfillment activities across different storage locations to avoid delays and ineffective item traveling.
- Multiple storage facilities management—manage inventory across several storage facilities from one platform.
- Optimized order fulfillment—enhance order fulfillment by strategically choosing the most efficient locations for picking and shipping.
Problems solved:
- Poor order picking and packing efficiency
- One storage-focused inventory management
- Inefficient item storage and distribution
- Lack of centralized visibility across disparate facilities
- Excess inventory turnover
5. IoT-Driven Inventory Management
Internet of Things (IoT) describes a set of smart devices connected to one network. The most popular smart devices supply chain businesses use are sensors, scanners, thermostats, cameras, and robotics. They foresee the opportunity to track inventory and maintain warehouses.
Implementing robotic actuators and automatic guided vehicles enables the opportunity to move items automatically or create dark warehouses, 100 %-automated storage facilities. Also, smart sensors can alert you about emergencies like leakage, fire, or unauthorized access.
Feature applications:
- Real-time data collection from sensors—continuously gather inventory data from sensors and real real-time insights on a dashboard.
- Item tracking and automated scanning—scan items using sensors or RFID automatically to ensure accurate updates on inventory movement and location.
- Centralized warehouse control and management—get comprehensive control over operations with access to warehouse operations from a single system.
- Automated item picking, packing, and transportation—integrate automated guided vehicles and robotic arms to perform repetitive tasks in a warehouse.
- Smart storage environment control—automatically monitor and regulate storage conditions like temperature, humidity, lighting, and more.
Problems solved:
- Insufficient inventory traceability
- Manual storage facility environment check and management
- Lack of real-time data on work-in-progress inventory
- Manual item scanning, picking, packing, and transportation
- Increased level of errors
IoT In Warehouse Management — Extensive Guide
6. Automated Item Quality Check
Ensure received and distributed items have no defects and match defined quality standards. To inspect inventory, incorporate diverse devices like cameras, weight scales, temperature sensors, or computerized tomography (CT) scanners.
Feature applications:
- Custom item inspection workflow creation—create customized item quality inspection workflows for different types of products to maximize the efficiency of QA teams.
- Automated inventory inspection—implement machine vision and other sensors for automated item inspection to run more efficient checks on inventory without manual intervention.
- Inventory quality check results collection and analysis—gather inspection results and create charts. Analyze data to identify trends and repetitive patterns.
- Alerts on items that haven’t passed an inspection—set automatic alerts that keep you alerted about failed inspections or detected defects.
- Regulatory compliance standards check—ensure all items meet required regulatory compliance standards by incorporating automated checks into the inspection process.
Problems solved:
- Delivery of damaged or defective items
- Increased wastage or return rates
- Regulatory compliance standards violation
- Ineffective manual random sampling inspection
- Time- and resource-consuming quality control process
7. Automated Workflows
Optimize the performance of the labor force and decrease the number of errors by implementing automation. Create custom rules that trigger actions when specific conditions are met. The feature implementation helps automate a lot of processes like item scanning, barcode creation, data update, transfer request creation, and others.
Feature applications:
- Automated order processing and transfer request creation—eliminate bothersome tasks from your workflows by making your IMS automatically process orders and generate transfer requests.
- Automated Inspection and return of defective items—inspect items for defects automatically and trigger immediate returns for any that fail.
- Documents and form pre-population—automatically fill documents with the data that is already present in a system, eliminating the need for employees to manually re-enter data.
- Automated picking and transfer of expired items to a disposal unit—remove expired products from our stock, dispose of them properly, and ensure that only fresh items are available to customers.
- Automated message delivery to customers and vendors—keep customers and suppliers informed about order progress, returns, or stock changes by sending automatic messages.
Problems solved:
- Manual data entry, order management, and document creation
- Increased manual error rate
- Timely item sourcing and order fulfillment
- Manual customer and vendor communication
- Manual item sorting and return
8. Bundles and Multiple Price Tiers
Create custom offers and implement loyal customer price tiers. Using this feature, you can create product kits by bundling a group of items into a single unit. Also, the feature foresees the opportunity to set custom discounts or multiple price tiers to enable adjustable pricing strategies.
Feature applications:
- Product kitting—combine multiple products in single kits and set different prices when products are purchased together.
- Quantity-based discount—adjust prices or automatically apply discounts based on the quantity of items purchased.
- Custom discount creation—enable the opportunity for sales representatives to create and issue custom discounts to negotiate with new customers and engage existing ones.
- Customer segmentation—categorize customers based on criteria like purchase history or demographics to make custom offers.
- Item cross-selling suggestions—provide automated recommendations for related products to encourage customers to purchase additional items.
Problems solved:
- No membership or loyalty programs
- Inflexible pricing strategies
- Insufficient upselling and cross-selling
- Decreased customer satisfaction
- No bulk sales opportunity
Take your IMS to the next level with advanced features
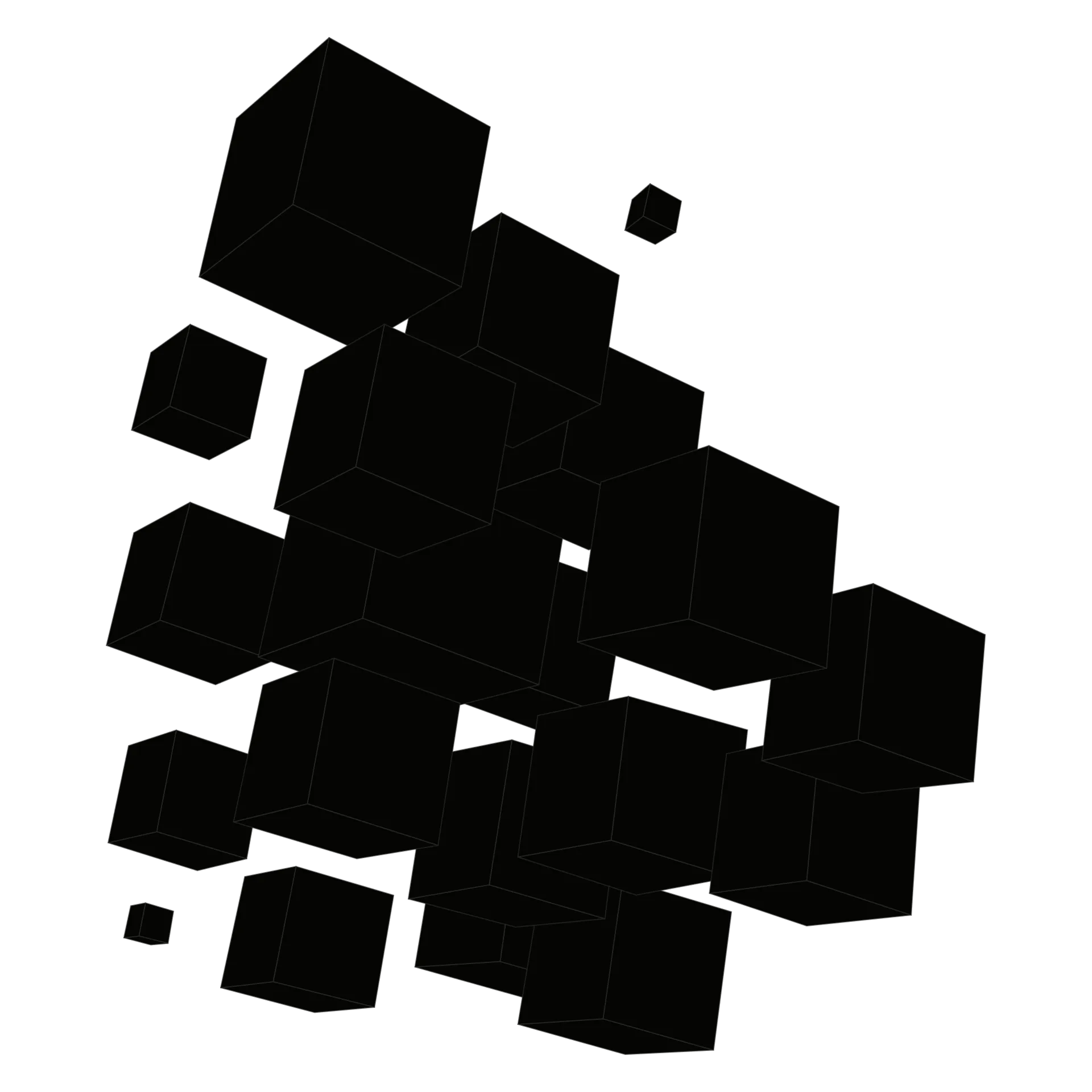
Business First
Code Next
Let’s talk
ConnetSx — medical inventory management system
The CodeIT team has hands-on experience in creating software with advanced inventory management system features.
Learn more about ConnectSx, the solution created by our team from scratch.
Problem
The client was unsatisfied with the internal processes’ inefficiency. Medical staff used spreadsheets to track and manage inventory manually. The processes were time-consuming, with a high risk of making an error.
The client has hired the CodeIT team to develop an efficient digital solution.
The client has hired the CodeIT team to develop an efficient digital solution.
Solution
Our team has tapped into the existing solution development. Providing custom software development services, we’ve analyzed it and prepared a detailed project reboot plan.
Our team has created three standalone applications:
- Web inventory management app
- Mobile inventory management app
- Mobile UDI scanning app
Using the developed web and mobile applications, users can:
- Manage and trace all the inventory items
- Import data from external sources
- Track medical product expiration dates
- Collect inventory data and analyze it
- Search lost items
- Submit transfer requests
- Scan barcodes to discover detailed information
Deep dive into the project and discover the application development processes with every step highlighted in our case study.
Inventory management software development — best practices
Take the guesswork out of inventory management development with best practices.
Pick Optimal Tech Stack
It’s vital to pick the right tech stack for developing a new system due to the limitations of technologies used in inventory management. Choose the most optimal solution to:
- implement inventory management system features
- stay on track with budget
- release features within a defined timeline
- enable the opportunity to scale up and upgrade
For example, by considering the native app development approach, a business needs to create two distinctive applications involving two teams of software engineers. However, by opting for a cross-platform system, they may develop an app that works on different platforms using one codebase.
Cross-Platform vs Native Mobile Development
Understand Business Challenges and Bottlenecks
Focus on implementing inventory management software features that solve the most critical business challenges. Unlock the true potential of your business by eliminating bottlenecks in workflows.
New features of an effective inventory management system should deliver feasible outcomes or solve business problems.
Define Inventory Management System Features List
For starters, you have to consider the key features of an inventory management system to implement. Focus on critical functionality to create a system’s MPV. It can be further enhanced with other less critical but helpful features.
Create a list of the most important features that should be presented in a product’s MVP. Other features should be prioritized to develop and release the most valuable functionality first.
Enable Real-Time Data Sharing
Real-time data sharing helps create centralized software that fetches data from multiple sources. Also, it helps manage inventory across multiple facilities.
The most popular ways to enable real-time data exchange between systems is by using:
- API integrations. The application programming interface comprises a set of rules that enable developers to connect software from different vendors.
- Centralized data repository. An on-premises or cloud-based server can collect all the data across a supply chain and share it with other systems in live time. Besides, data can be preprocessed to improve the performance.
- Point-to-point synchronization. A direct TCP/IP connection between two software applications for real-time data exchange.
The development of additional data mapping tools may be required to connect third-party systems.
Consider Scalability
Having a long-term strategy is important when developing a new solution from scratch. The two software architecture options to choose from are:
- Monolith: Easy to build core functionality. However, the more solutions’ complexity increases, the more challenging it is to add new features.
- Microservises: Requires more effort to build an inventory management system with the baseline functionality. New features can be easily added as distinctive microservices, even if they are built using different technologies.
Monolithic Architecture vs Microservices: Strengths and Weaknesses
Conclusion
The key features of an inventory management system that help enable the baseline functionality are:
- Inventory tracking
- Identifiers issuing and scanning
- Order management
- Item storage management
- Reports and analytics
- Backup and data import/export
The advanced inventory management system features that help enhance the functionality of the existing software are:
- Automated re-ordering
- Third-party software integration
- Multiple-location management
- Demand forecasting
- IoT-driven inventory management
- Automated item quality check
- Automated workflows
- Bundles and multiple price tiers
Need IMS with a custom feature set?
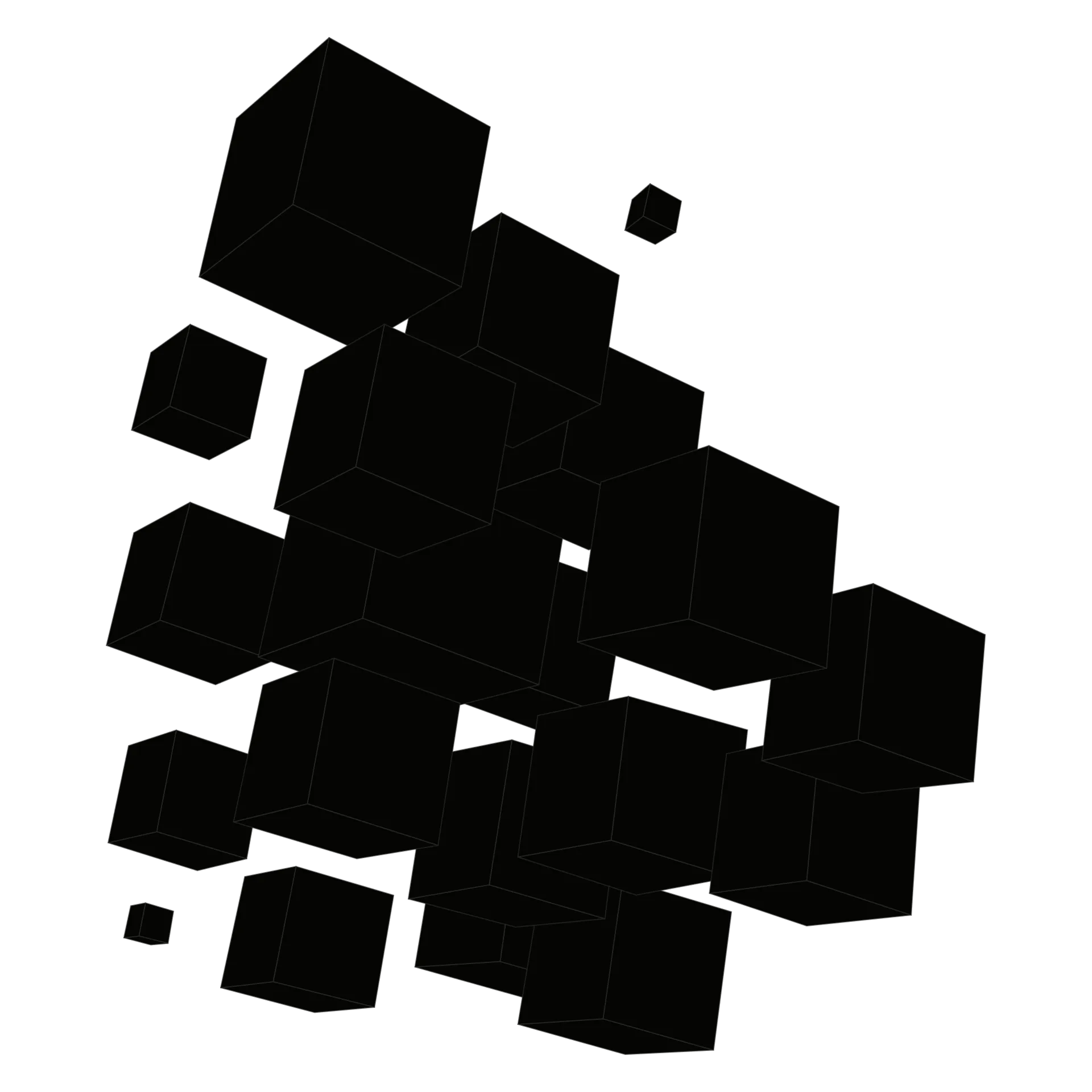
Business First
Code Next
Let’s talk
FAQ
The real-time inventory tracking and control software enables continuous visibility across a supply chain. Trace the movement of items in live time. Receive instant updates on in-stock/out-of-stock inventory, detected issues, processed orders, etc.
The feature helps enable automatic order fulfillment capabilities by checking in-stock inventory before accepting a new request. Also, the feature helps reserve items, track their processing statuses, and automate workflows.
This inventory management system feature helps avoid stockout and overstocking by creating data-baked product sourcing strategies. Demand forecasting features help predict seasonal demand spikes and trend changes or detect repetitive patterns in customer behavior.
Barcode scanning helps increase item sourcing, picking, and management efficiency and speed. Also, it reduces the risk of human error and eliminates the need to enter data manually. A barcode or QR code can contain encoded detailed information about a product.
Inventory reporting tools help pre-process collected data and deliver useful insights. Businesses can use detailed analytics to define bottlenecks and track the results of their strategy adjustment decisions.
Automation helps optimize inventory management processes by reducing the amount of manual input required. The main activities that can be automated are:
- Barcode scanning and label issuing
- Inventory tracking
- Order processing and management
- Item picking and packing
- Inventory receiving, replenishment, and returns
- Item inspection
- Vendor and customer communication
The best practices for implementing an inventory management system that matches 100% of business needs are:
- Optimal tech stack selection
- Business challenges and bottlenecks identification
- Inventory management system features list creation and prioritization
- Real-time data-sharing functionality development
- Product scalability opportunities identification
Related services and industries
Inventory Management Software
Take inventory control, optimize your supply chain, and achieve sustainable growth.
Build your ideal
software today
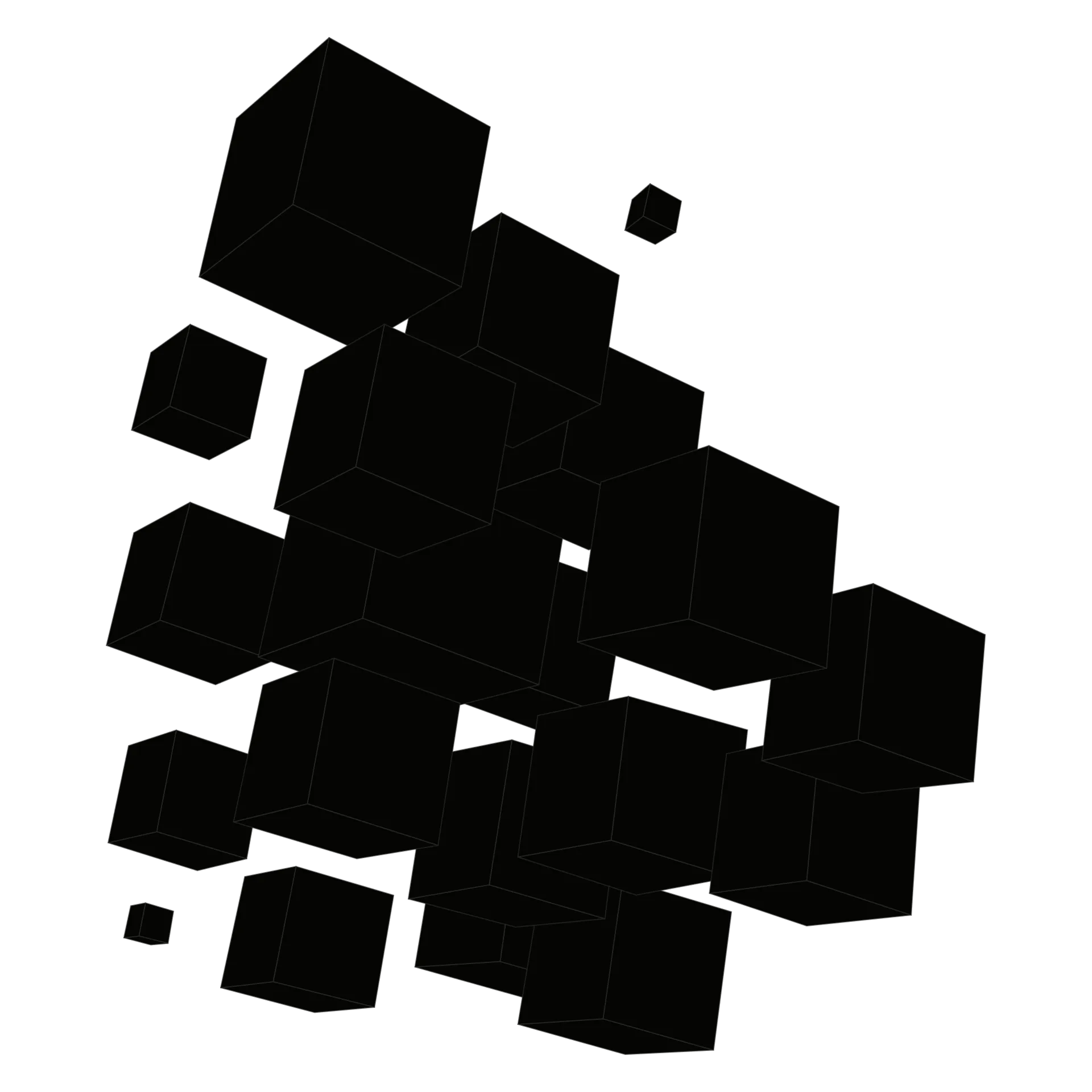