Warehouse Automation System Solutions and Technologies
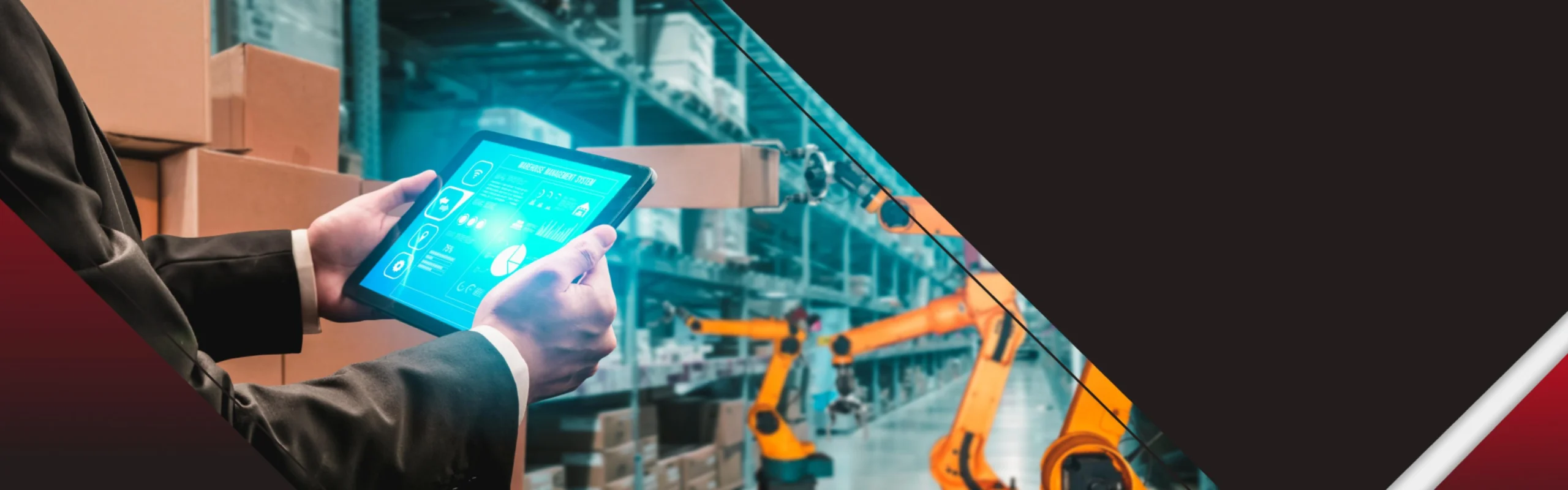
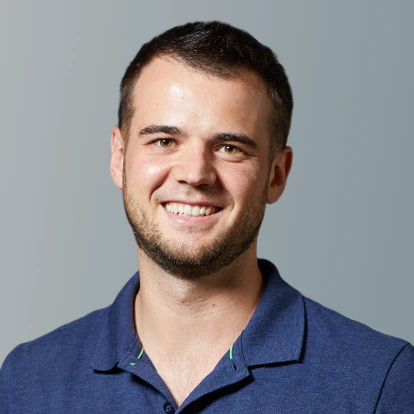
The primary aim of warehouse automation is to replace the labor force with machines. It is achieved by digitizing workflows, developing data-sharing pipelines, and integrating smart hardware.
The foremost solutions used for enabling warehouse automation are:
Software Solutions | Hardware Solutions |
---|---|
Warehouse Management System (WMS) | Pick-to-Light and Put-to-Light |
Business Intelligence | Automated Assets Tracking |
Machine Learning | Automated Sortation Systems |
Internet of Things (IoT) | |
Automated Guided Vehicles (AGVs) |
Basics of warehouse automation
Machines can perfectly perform monotonous tasks without any help to minimize the chance of errors or accidents. The two core components are:
- Digital — Software products that facilitate inventory management and offer the opportunity to monitor processes in live time. Warehouse management systems are the most widespread type of technology used for the digital transformation of storage facilities.
- Physical — Mechanical devices that reduce the need for workers to pick and move assets manually. The top physical warehouse automation solutions are robotic arms, conveyor belts, and automated guided vehicles.
In a nutshell, a warehouse automation system is a set of technologies that develop the industry 4.0 storage facility. In smart warehouses, most monotonous and repetitive tasks are performed by robots. Meanwhile, managers have comprehensive control over all the processes.
The three levels of automation in a warehouse are the following:
- Low or no automation — A business uses the labor force to store and move items in a warehouse. Inventory management is performed manually using spreadsheets.
- Systems and mechanized automation — It is the moderate automation level. A storage facility widely uses WMSs to track assets automatically and make automated decisions. Also, some processes are mechanized to automate tedious work or help move heavy items.
- Sophisticated automation — The advanced automation level. A business adopts the latest solutions, striving to build a 100% autonomous storage facility.
There is no one-size-fits-all warehouse automation technology. A large assortment of technologies offers the opportunity to build various storage facility automation systems.
Warehouse automation solutions
The development of automation warehouse systems has been growing for many years.
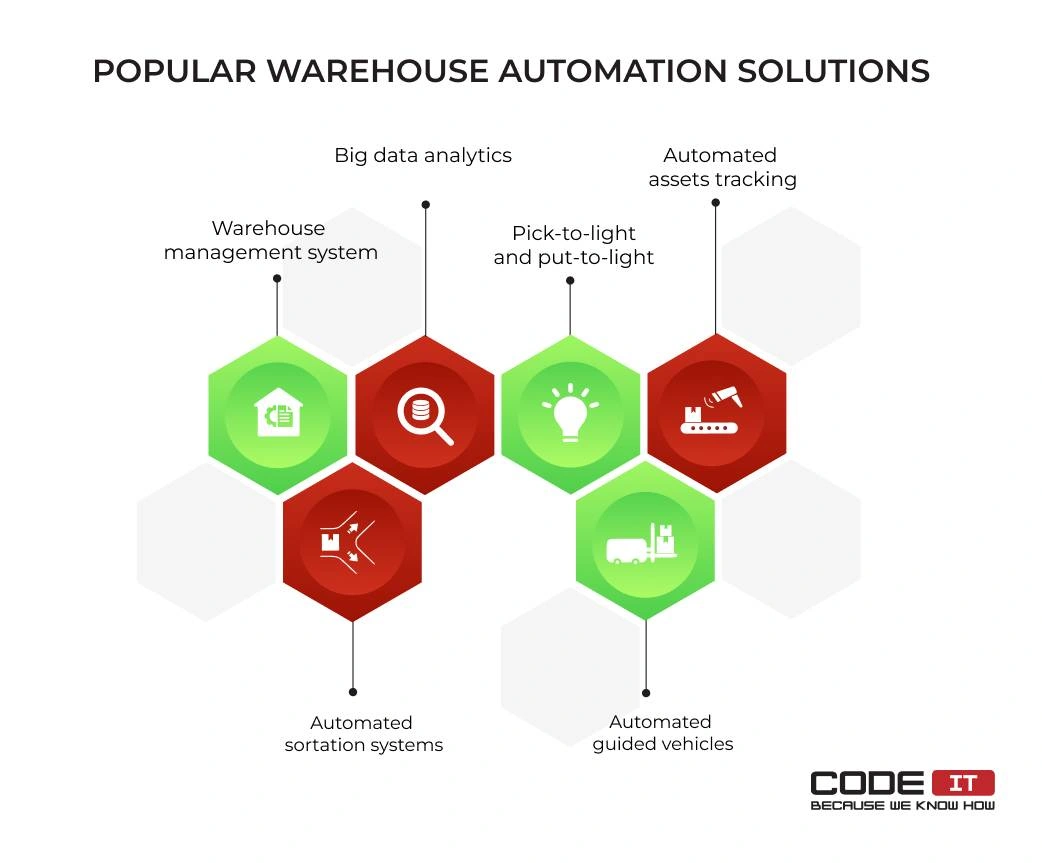
Below, you will find the most popular warehouse automation optimization technologies that were tried and tested by many companies.
1. Warehouse Management System
A warehouse management system (WMS) is a software solution that helps track all warehouse automation processes.
In a nutshell, it is an advanced enterprise resource planning tool. A WMS holds information about all assets that enter and leave a storage facility.
Warehouse Management System Benefits | ||
Inventory visibility | Reduced operational costs | Live-time tracking |
Optimized items storage | Improved customer experience | Transparent billing and invoicing |
Enhanced security | Efficient labor management | Workflow digitization |
The key features of a warehouse management system are:
- Import and export
- Inventory management
- Order details
- Real-time tracing of assets
- Dashboard
- Picking and packing information
- Billing and invoicing
- Labor management
- Reporting
Warehouse management systems are distinguished into two types that are:
- Cloud-based — Software is installed on a server that a third-party company maintains. All the data is transferred via the Internet. Therefore, a reliable network connection is required to reduce the risk of WMS downtime.
- On-premises — Warehouse management software is installed on a local server. Hardware should be managed and maintained by a business. It offers the opportunity to create a local network that does not rely on the Internet connection.
Also, warehouse management systems can be:
- Pre-built — A solution that a third-party company creates. Ready-made WMSs can be easily installed and configured. However, they may not completely meet the requirements of a business. Only a software provider can develop and release new inventory management system features. Also, most vendors charge monthly fees based on the number of features, managers, and items.
- Custom-made — A type of warehouse management solution that is created from scratch. They have the form of well-tailored solutions that help achieve all business goals. Custom software can be easily updated and scaled up. Developers can add new features upon request.
Custom WMS? Hire codeit team!
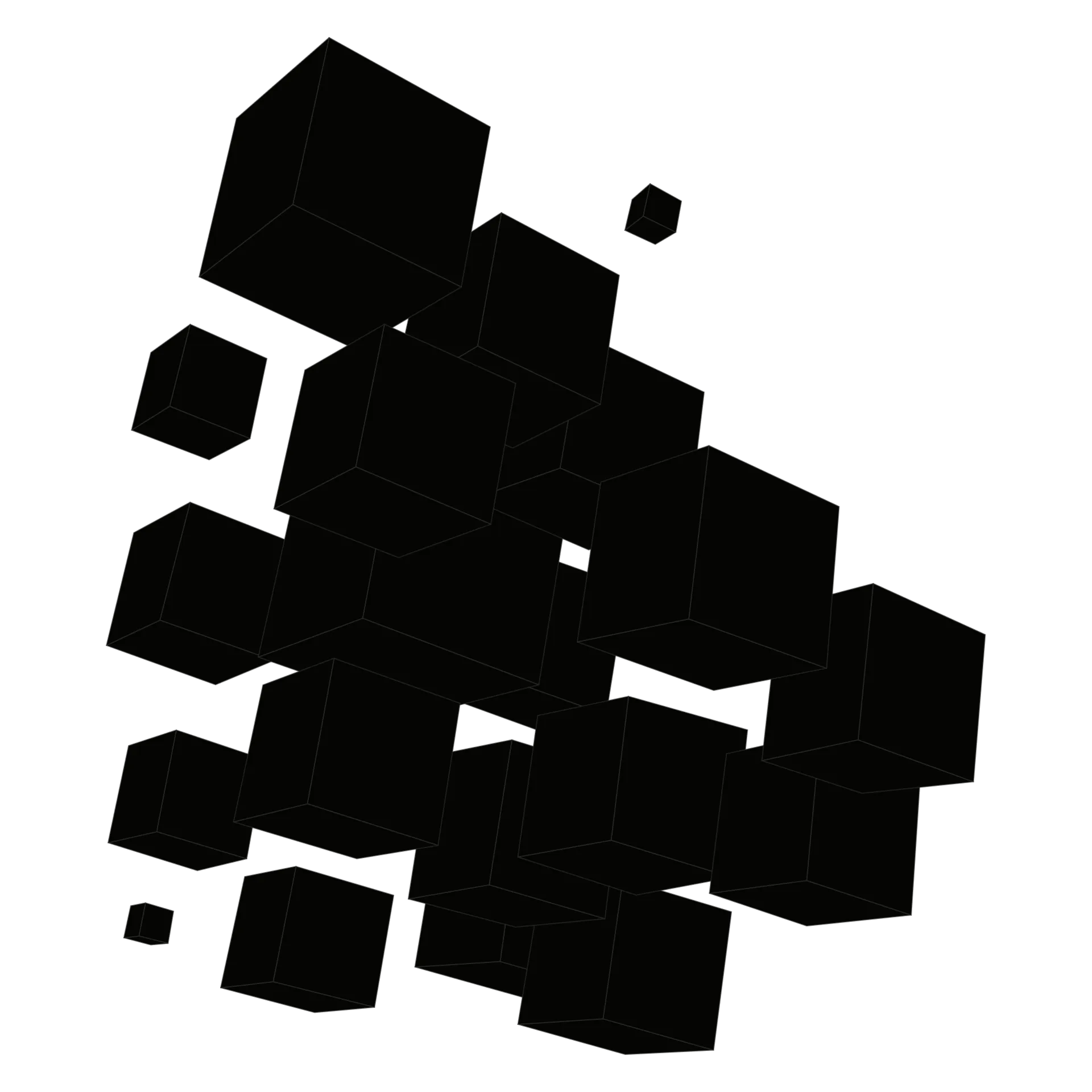
Business First
Code Next
Let’s talk
2. Pick-to-Light and Put-to-Light
This technology’s integration can help increase personnel’s performance by 40%, on average.
The system implies small light bulbs installed on racks. The bulbs identify items needed to pick and containers to use.
Workers need to scan a barcode when new assets arrive at a warehouse. Then, the system will guide workers by automatically highlighting containers where a new item should be put in.
Meanwhile, it is easier and cheaper to implement compared to other warehouse management automation solutions. It helps eliminate the need to find items on shelves manually.
Pick-to-Light and Put-to-Light Benefits | ||
Increased productivity | Enhanced accuracy | Reduced risk of item misplacement |
Fast and simple implementation | Quick staff training |
3. Automated Assets Tracking
Automated item tracking helps businesses find assets quickly and trace their location in real time.
Scanners that track signs attached to them enable automated inventory management. These scanners and sensors automatically detect items and update information about their location in a warehouse management system.
For instance, scanners can be installed on a conveyor belt to track the location of items in live time. Also, scanners can be installed on forklifts, palettes, racks, and lorries for efficient automation in warehouse management.
The most popular solutions used to track items automatically are:
- Barcodes — One of the most widespread solutions to track items. It requires installing barcode scanners, ensuring a short distance to codes, and providing good lighting conditions. Unfortunately, the scanning speed is low.
- RFID tags — An innovative alternative to barcodes. RFID tags use radio waves to send and receive data. They can hold a certain amount of data and update it. RFID tags are durable, can be attached to almost any material, and can be scanned in bulk. These features make them a preferred choice for automated scanning by many companies.
- Beacons — Small devices that have built-in batteries and sensors. Beacons can hold information about items they are attached to. This type of device emits the Bluetooth signal constantly. When paired to another device connected to the Internet, data gets transferred to the central server or the nearest edge processing unit. Also, Bluetooth technology offers the opportunity to measure items’ locations indoors precisely.
- Graphic signs — Businesses can use AI-driven cameras to track items, vehicles, and tools. Signs placed on items help smart cameras detect items accurately.
A business can also use the technologies and a fleet management system to track vehicles in storage facilities and sites.
Automated Assets Tracking Benefits | ||
Real-time tracking | High location detection accuracy | No involvement of workers |
24/7 assets tracking |
4. Automated Sortation Systems
It is one of the most widely used warehouse automation software that helps decrease the use of the labor force significantly.
An average automated sortation system consists of three major components:
- Conveyor belts — Assets are moved on a conveyor belt in a warehouse.
- Items identification system — Items get detected using barcodes, RFID tags, beacons, or other technologies.
- Separators — A sliding shoe sorter or a plastic separator moved by an actuator to change the direction of an item.
Automated sortation systems can facilitate asset storing and automate item packing. The modular design offers the opportunity to build custom systems for every warehouse, following defined business needs.
Automated Sortation Systems Benefits | ||
Reduced labor costs | Automated sorting and packing | Enhanced productivity of a warehouse |
Improved accuracy | Faster order processing | Efficient space utilization |
Reduced risk of error |
5. Automated Guided Vehicles
Enterprise-grade warehouses vastly use automated guided vehicles (AGVs).
AGVs are small robots that automatically move packages or racks in storage facilities. They deliver items to workers in the packing zone and return them to the storage zone. Consequently, they eliminate the need for workers to pick items manually.
The top features of AGVs:
- Automated items delivery
- Error-free packages placement
- Automated route planning
- Automated charging
- Great scalability
With the help of network connectivity and many different technologies used for precise positioning, they don’t crush each other.
Automated Guided Vehicles Benefits | ||
Reduced labor costs | 24/7 operation | Increased safety |
Improved efficiency | Improved scalability |
6. Internet of Things
The Internet of Things (IoT) term defines a set of smart devices and sensors that are connected to one network. They help enable supply chain visibility and control operations in a warehouse using centralized software solutions.
The most widespread applications of IoT for warehouse automation are:
- HVAC control — Environment data is gathered from temperature, humidity, and other sensors. The data is analyzed in real-time, and commands are issued to HVAC equipment.
- Equipment monitoring — Vibration, temperature, acoustic, pressure and other sensors collect machine health data and send it to the main server. The received information is analyzed for predicting machine failures.
- Inventory management — RFID sensors, beacons, UDI scanners, and other IoT devices help monitor the location of items in a warehouse.
- Safety monitoring — Internet-connected sensors detect gas/water leakage, fires, or other hazardous conditions, delivering instant alerts if any of them are detected.
- Energy management — Smart meters record energy consumption data and send it to the central server in real time.
Internet of Things Benefits | ||
Real-time tracking | Enhanced inventory management | Predictive maintenance |
Centralized control | Enhanced worker safety |
IoT in Warehouse Management — Extensive Guide
7. Business Intelligence
Business intelligence (BI) software solutions help visualize and analyze large amounts of raw data collected from smart sensors and other equipment. BI solutions are used to create custom dashboards that update data in real time and generate automated reports.
Also, algorithms help extract valuable insights from the raw data to optimize warehouse usage and minimize the risk of running out of stock.
Business Intelligence Benefits | ||
Real-time insights | Data visualization | Automated report generation |
Data-driven optimization | Improved warehouse layout and design | Enhanced resource allocation |
8. Machine Learning
Machine learning (ML) uses statistical algorithms capable of learning from data. ML models can process large amounts of data, enabling predictive maintenance, demand forecasting, storage space optimization, etc.
Machine Learning Benefits | ||
Demand forecasting | Autonomous robots management | Dynamic pricing and promotions |
Improved customer experience |
Develop a smart warehousing solution — tailored to your business
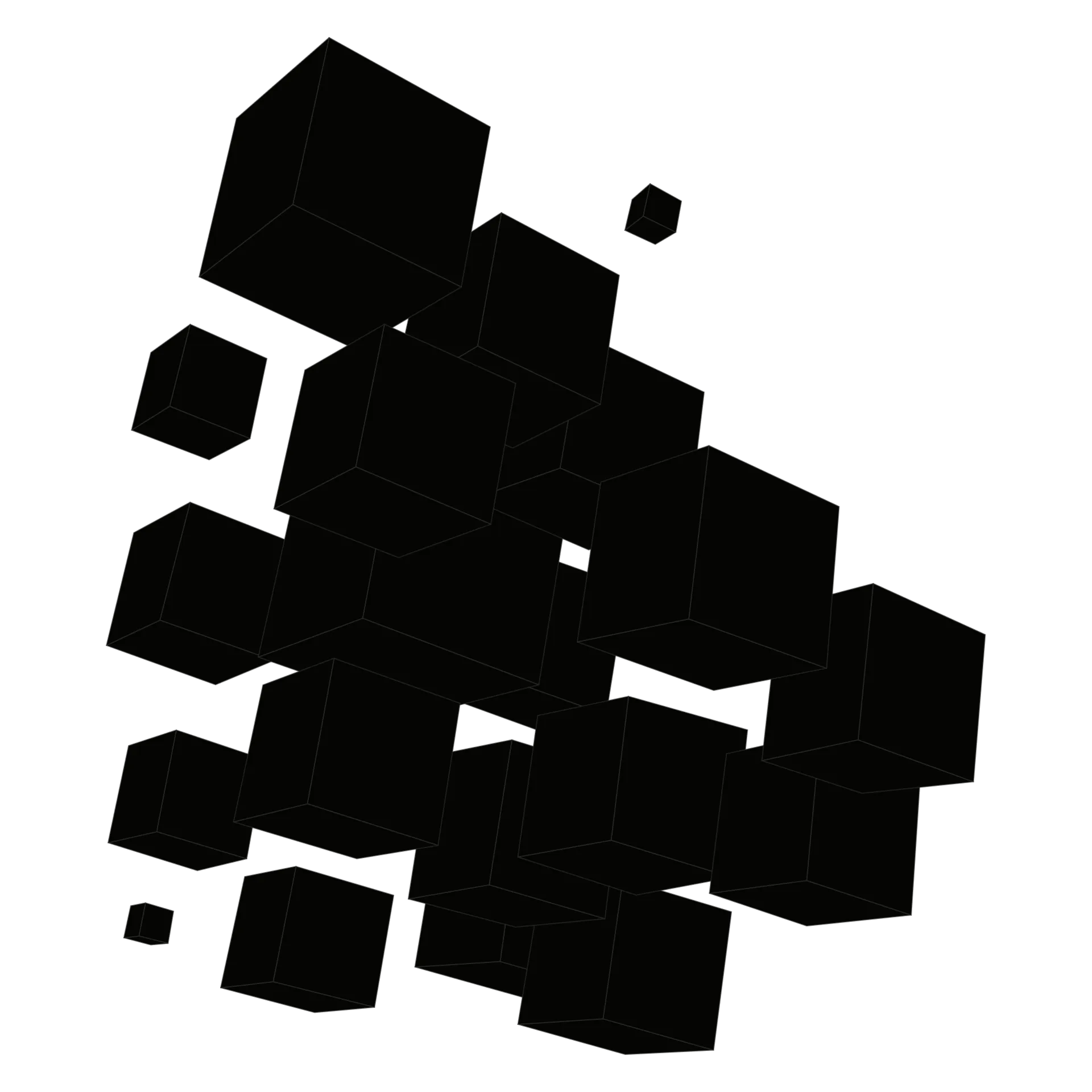
Business First
Code Next
Let’s talk
Reasons to adopt warehouse automation
Let’s check the reasons for adopting new technologies backed by real statistics.
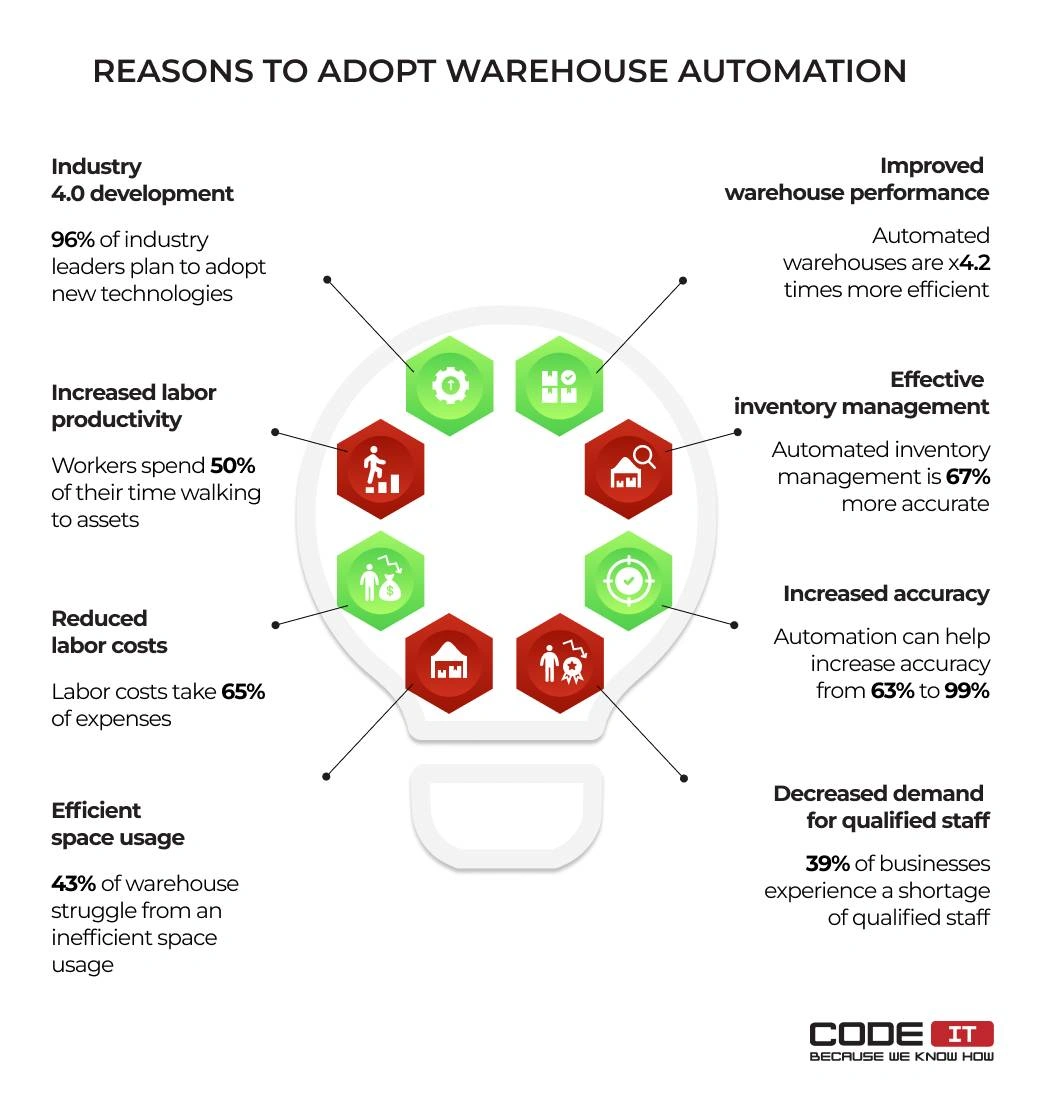
1. Industry 4.0 Development
96% of industry leaders are confident that adopting the latest technologies is the only way to grow. Moreover, it’s required to implement new warehouse automation solutions to overcome counterparts.
2. Improved Warehouse Performance
Automated storing, picking, and sorting solutions are 4.2 times more efficient than manual warehousing. Warehouse automation solutions can pick and deliver assets faster. Also, they are more accurate and can work autonomously without any supervision.
3. Increased Labor Productivity
Roughly 50% of the time spent by workers is allocated to traveling in a warehouse. The use of warehouse automation software helps move assets automatically. Items can be retrieved from the storage zone and automatically moved to the picking and packing zone.
4. Effective Inventory Management
Warehouse automation technologies help increase inventory management accuracy by 67%. RFID, pick-to-light, IoT, and other technologies reduce or eliminate manual input by automating repetitive tasks. Also, data-sharing pipelines help automatically collect and share automatically, reducing the chance of error.
Role of Technologies in Inventory Management
5. Reduced Labor Costs
The cost of labor takes over 65% of the operating budgets of warehouses. Moreover, the cost of the labor force is expected to increase shortly because of workers’ shortages and the continuous rise of minimum wages.
6. Increased Accuracy
Manual inventory management is accurate in 63% of cases only. The use of modern technology control helps reduce the chance of human error. Complete warehouse automation helps achieve 99.9% accuracy.
7. Efficient Space Usage
43% of businesses report the problem of insufficient storage space usage. Warehouse automation helps increase the efficiency of using space in a storage facility.
8. Decreased Demand for Qualified Staff
39% of businesses in the warehousing industry struggle to find qualified staff. By integrating robotic technologies, the need for qualified staff is reduced. It helps save money on scouting, hiring, and new personnel training.
Real-Time Inventory Management System
Real-world warehouse automation examples
Most industry leaders keep up with warehouse automation trends and integrate the latest technologies.
Let’s explore the read-world warehouse automation examples below.
Amazon
Amazon is the most prominent innovator in supply chain automation. The company keeps adopting new technologies to automate storage facility operations.
The primary warehouse automation technologies adopted by Amazon to improve its supply chain are:
1. Automated guided vehicles
Amazon has developed an advanced AGV named Proteus. It is a powerful device that helps automate or facilitate warehouse operations.
Also, it has unique features that make it stand out from other AGVs. With extensive industry expertise, Amazon managed to develop an automated guided vehicle fleet that helps overcome the significant challenges companies face when adopting the latest warehouse automation trends.
The key features of the Proteus model are the abillity to:
- Move around people in a warehouse
- Change routes to avoid collisions in live time
- Move heavy objects
- Tow wheeled items
Using automated guided vehicles has helped the company increase performance, reduce operating costs, and lower the number of injuries.
Amazon has already integrated more than half a million Proteus AGVs into its warehouses.
2. Automated sorting and picking
Amazon has launched an AI-driven package picking and storing technology. The Cardinal system helps automate tedious manual item identification and sorting tasks. It is one of the successful warehouse automation examples.
It implies the following technologies:
- Conveyor belts and separators
- AI-driven robotics arm
- Containers moved by AGVs
The intelligent robotic arm is one of the most crucial components of this automated sorting and picking system.
The Cardinal system can:
- Pick packages of different shapes and sizes
- Lift heavy boxes (up to 50 pounds)
- Read labels and scan barcodes
- Pick certain packages from a stack
- Place packages into required containers
3. Scanless packages identification
The automated scanning feature developed by Amazon helps workers increase their performance.
The system implies an advanced camera and AI-driven software. It can identify objects automatically when they appear in the vision zone of a camera.
It erases the need to pick scanners, find barcodes, and scan them manually. Workers simply need to move packages in a certain zone.
The inventory management process is performed in the background.
Need advanced IMS created from scratch?
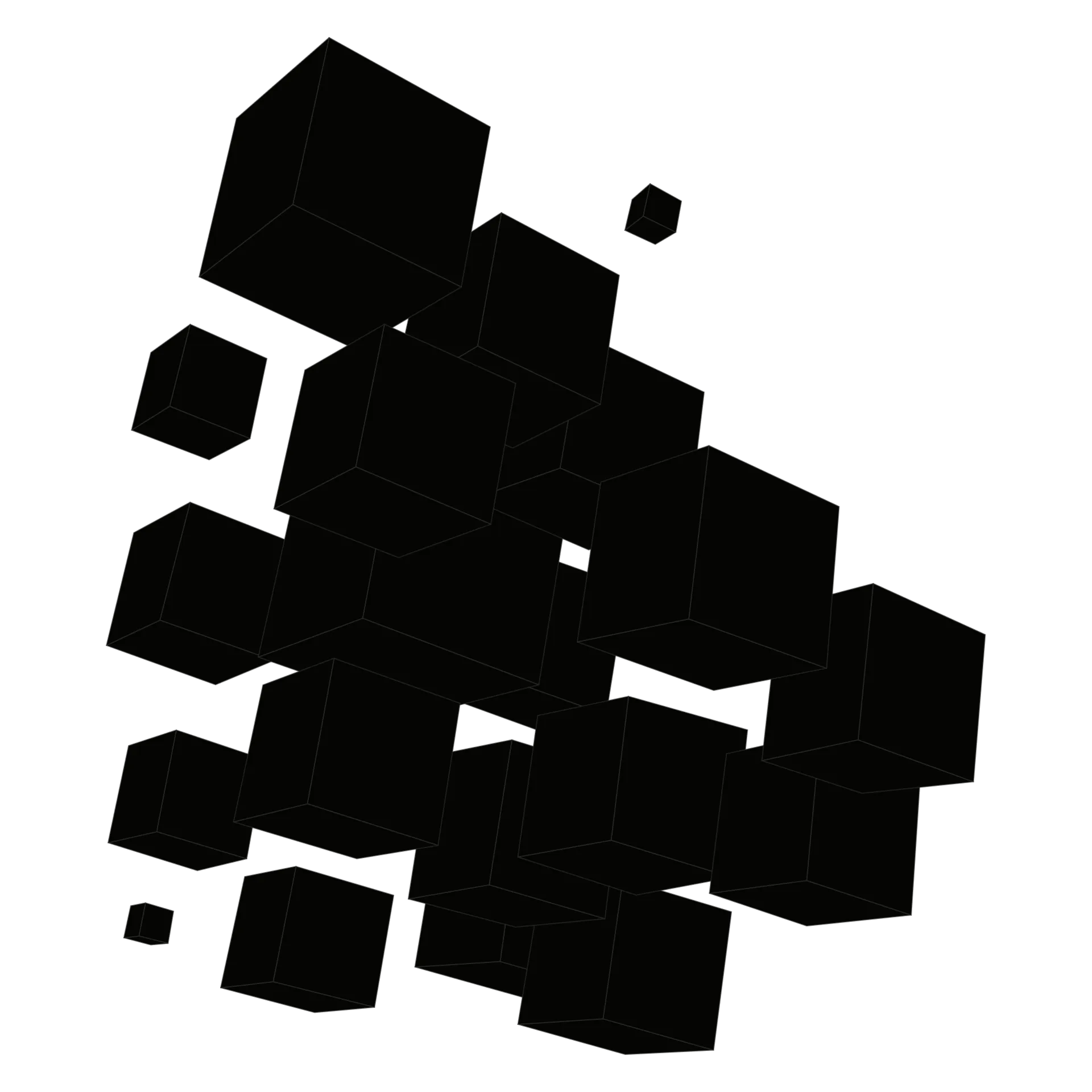
Business First
Code Next
Let’s talk
4. Containerized storage system
It is a system that helps develop an efficient automated storage facility with the help of unification.
The system implies plastic containers that are placed on racks moved by AGVs. Since all the containers are similar, robotic arms can easily pick and move them.
It helps overcome the challenge caused by the inability of robotic arms to pick small items of different shapes.
Ocado
Ocado is an online-only grocery store that operates in the United Kingdom. It processes an enormous amount of orders that need to be packed and delivered to customers.
In order to keep up with the rising number of orders and scale up their business efficiently, the company has developed one of the most innovative technologies that set modern warehouse automation trends.
The warehouse’s distinctive peculiarity is that it wasn’t designed for people and has an advanced warehouse automation control system.
Nowadays, most companies tend to integrate robots into environments designed for humans. However, the company has designed an utterly robot-centric warehouse.
No human assistance is required to pick up products and collect orders. There is only a team of mechanics and supervisors who maintain the facility. They help ensure a 100% uptime of the system and accurate order collecting.
The company has built an automated warehousing system that uses AGVs, conveyor belts, and robotic arms to collect orders automatically.
The system comprises two major components.
1. Storage and retrieval system
The system has the form of a grid made of rails. Storage containers are located under the grid.
AGVs move in different directions and find the required cells automatically. They can pick up or put storage boxes and move them to other zones.
The system implies roughly 200 AGVs that are united into one system. It helps them avoid collisions and work effectively together, even though the distance between robots in the grid is only 5 millimeters.
2. Order collection system
The system is designed to collect custom orders by picking the required items and putting them into bags that will be delivered to customers.
The order collection system implies a robotic hand, a set of cameras, and a conveyor belt. The robotic arm has a unique mechanism that foresees the opportunity to grab items of any size, shape, and material. Three-dimension cameras that use AI help the arm identify objects and their position.
When orders are collected, they get moved to the delivery department.
The warehouse management system tracks all the groceries automatically. Managers get notified simultaneously when some groceries are about to run out of stock or expire.
Main takeaways
The fast-paced development of modern technologies drives the warehousing industry to grow.
The top warehouse automation solutions are:
- Warehouse management systems
- Automated guided vehicles
- Automated sortation systems
- Automated assets tracking
- Pick-to-light and put-to-light technology
- Internet of Things
- Business intelligence
- Machine learning
Warehouse logistics automation technologies help automate manual processes. They offer the opportunity to build well-tailored warehouse automation solutions for businesses of any scale.
Build connected warehousing with automated workflows
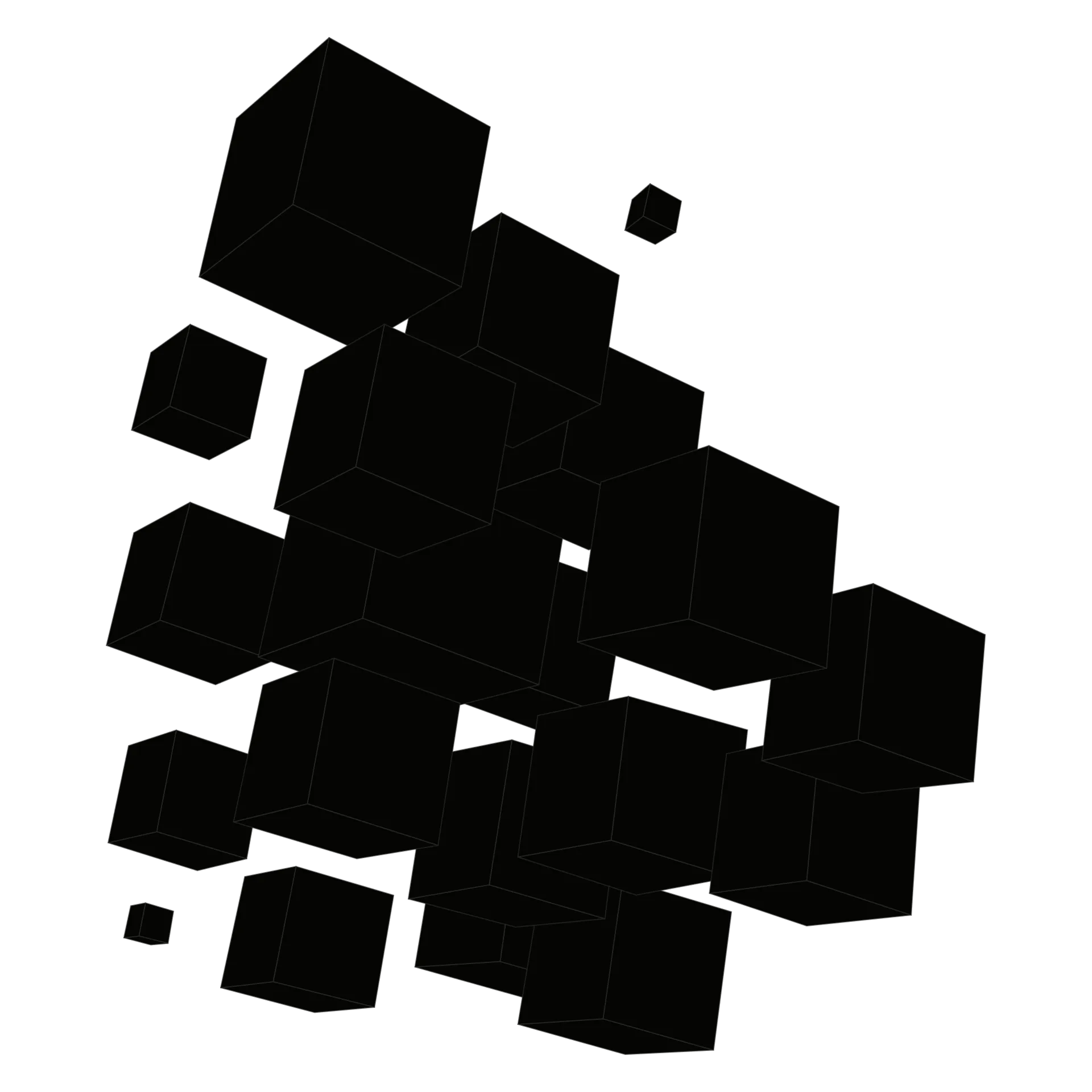
Business First
Code Next
Let’s talk
FAQ
The three levels of storage facility automation are:
- Low or no automation
- Systems and mechanized automation
- Sophisticated automation
Yes. Complete warehouse automation is the main goal for many industry leaders. 100% autonomous storage facilities are expected to appear by 2030. They will be called “dark warehouses” because robots don’t need good lighting conditions to perform their duties.
The price of warehouse automation depends on many factors. The scale of business and technologies to use are the main ones. The approximate cost of automating a storage facility ranges from $500,000 to $25 million.
Automation in warehousing aims to reduce the demand in the labor force by making different processes performed by machines and computers.
The two main advantages of automation in a storage facility are:
- Improved warehouse performance
- Reduced labor costs
- Industry 4.0 development
- Increased labor productivity
- Effective inventory management
- Increased accuracy
- Efficient space usage
- Decreased demand for qualified staff
An automated warehouse system combines software and mechanic tools that can move items in a storage facility and perform inventory management autonomously.
There are many versatile ways to automate processes in a storage facility. The main types of warehouse automation are:
- Warehouse management systems
- Pick-to-light and put-to-light
- Automated assets tracking
- Automated sortation systems
- Automated guided vehicles
- Robotic arms
- Automated storage and picking systems
- Drones
- Industrial IoT
- Automatic truck loading
- Predictive maintenance
Related services and industries
Logistics Software Development
Get solutions designed to streamline operations
Build your ideal
software today
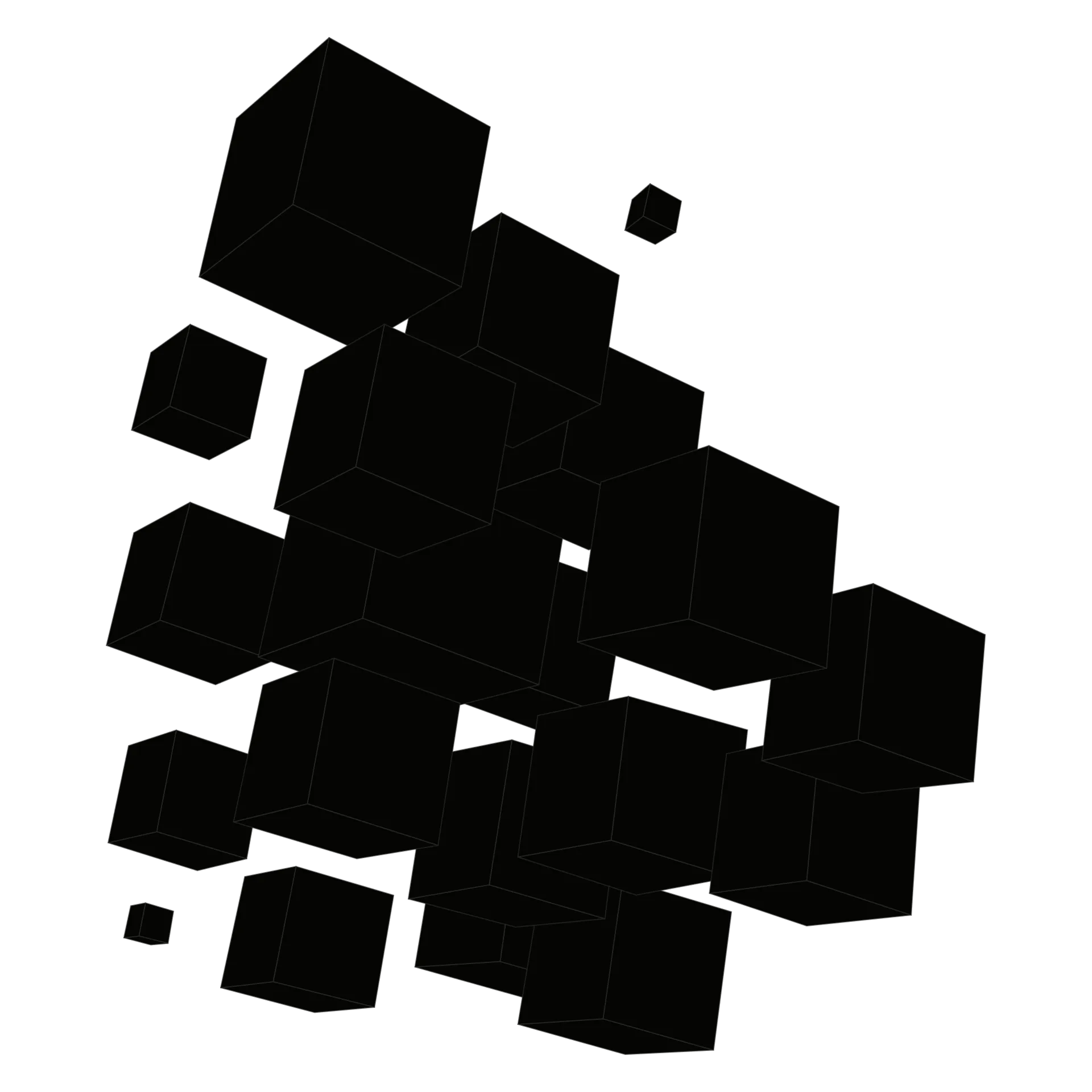