Warehouse Automation Trends in 2025
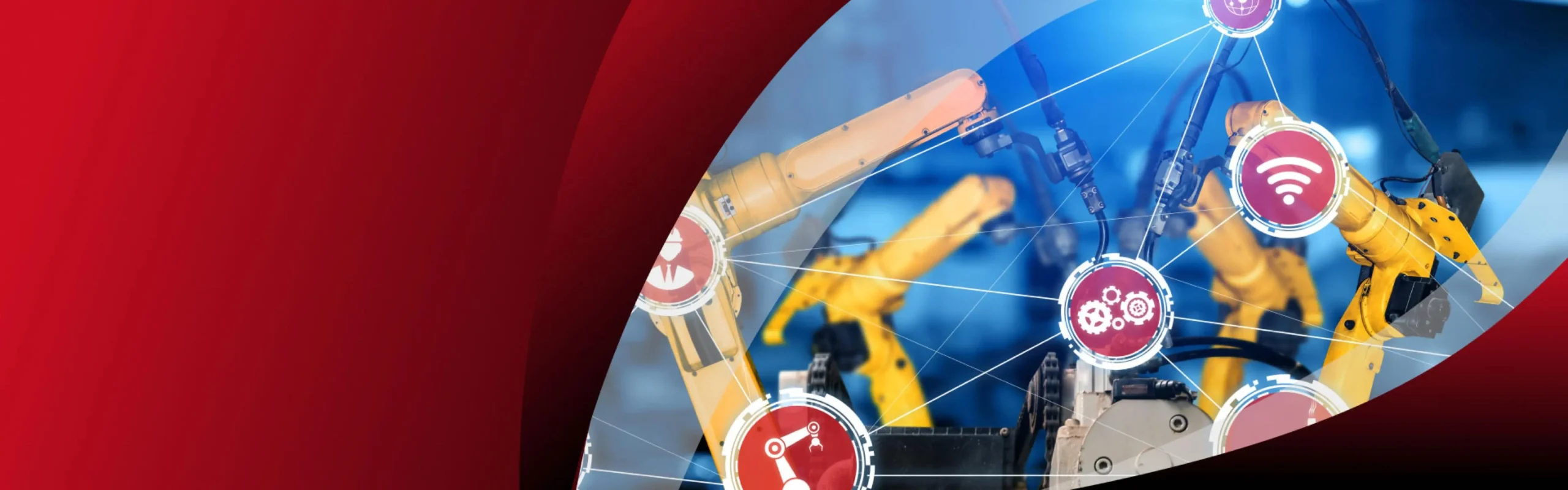
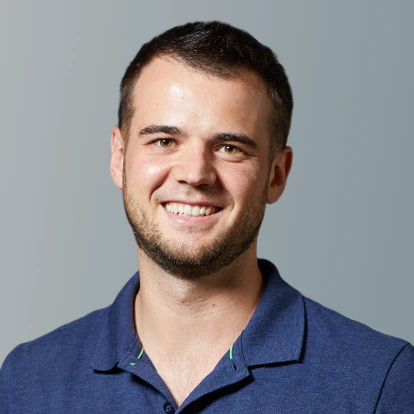
Warehouse automation is a rising trend in the supply chain industry. Steve Banker, a Forbes contributor, states that automation is the feasible future of warehousing.
McKinsey & Company reports that the fast-paced development and adoption of new technologies make many companies enhance warehouse and inventory management processes significantly.
Top Ten Trends In Warehouse Automation
The fastest-growing warehouse automation technology trends are as follows.
- Robotic Arms
- Automated Storage and Picking
- Drones
- Industrial IoT
- Automatic Cleaning
- Automatic Truck Loading
- Wearables
- Predictive Maintenance
- Voice Picking
- Sustainable Warehousing
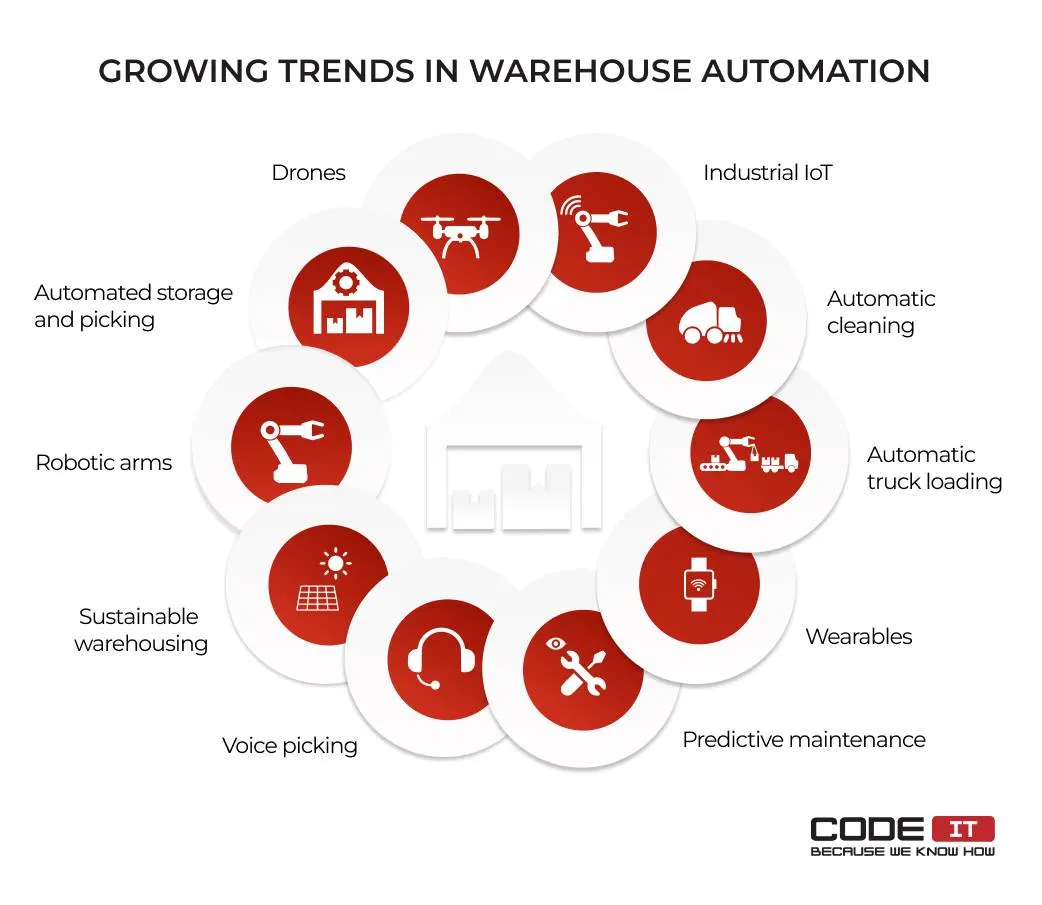
Let’s take a deeper dive into each warehouse automation trend below.
1. Robotic Arms
Robotic arms have been used in the manufacturing industry for a while. They help move packages automatically. Also, they help pick and pack heavy items.
This warehouse automation technology eliminates the need to use the labor force to pick assets. There are a lot of storage facility configurations that use robotic warehouse automation systems for different purposes.
However, robotic arms are usually used to pick items from shelves and put them on a conveyor belt, and vice versa. Besides, robotic arms can be installed on automated guided vehicles.
Need help implementing advanced technologies?
The top benefits of this technology are:
- 24/7 work
- Improved efficiency
- Increased safety
- Enhanced precision
Notably, robotics arms are usually designed to pick only one asset type. Consequently, they can hardly pick items of various sizes and shapes. Businesses put all assets into unified boxes that robotic arms can move to overcome this challenge.
2. Automated Storage and Picking Systems
This type of warehouse automation system is completely automated. They use many different technologies and work autonomously.
Integrating this technology aims to create a dark storage facility, a popular warehouse automation trend. Dark warehouses are 100% automated. Hence, no lighting is required.
Automated storage and picking systems use a combination of different technologies:
- Robotic arms
- Conveyor belts
- Automated guided vehicles
- Automated assets tracking
This warehouse automation system can pick the required items from shelves in the storage area and deliver them to people in a packing zone. Also, it can take arrived assets and put them on shelves.
A warehouse management system controls all the processes.
3. Drones
The usage of drones is one of the rising warehouse automation trends. These small devices can travel long distances and explore high shelves fast.
They can float automatically or be guided by a worker. Since drones can transmit video in real-time, an operator is not required to follow a drone.
The operations that drones can perform are:
- Storage facility inspection
- Barcode scanning
- Stock finding
- Packages’ moving
It is worth noting that inventory drones differ from commercial aerial shooting models. They have collision-avoidance sensors and blade protection to work effectively on the premises.
Inventory drones have no GPS connectivity and are not required to comply with local aviation regulation rules.
4. Industrial IoT
The Internet of things (IoT) is a concept that describes the use of intelligent devices connected to one system. It is one of the most popular warehouse automation trends that define many different devices, including the ones highlighted in the post.
The most widespread IoT devices used for warehousing are:
- RFID tags
- Beacons
- Smart sensors
- Smart HVAC systems
- AI-cameras
- GPS trackers
IoT devices can gather data and send it to processing units using a network connection. Some devices can process information and send condensed data.
The primary aim of industrial IoT is to automate processes and enhance warehouse management.
For instance, a smart sensor can detect lighting conditions in a warehouse and send commands to intelligent bulbs to adjust the lighting. Also, smart sensors can help HVAC systems automatically maintain the required storage facility conditions.
The key benefits of applying the Internet of Things in a warehouse are:
- Reduced operating costs
- Real-time tracking
- Improved inventory management
- Increased performance
- Enhanced forecasts accuracy
- Automated maintenance
- Reduced risks
- Detailed analytics
5. Automatic Cleaning
It’s essential to keep a storage facility clean. Usually, the labor force is used to operate sweeping machines in a warehouse.
Unfortunately, the labor force expenses evolve, making businesses consider robotics technologies to keep their premises clean and tidy.
Robotic cleaning machines are used to achieve automatic cleaning. These machines navigate using computer vision, LiFi technology, or floor stickers. They resemble standard sweeping machines but do not have operators.
This solution has a lot of warehouse automation benefits that are:
- 24/7 storage facility sweeping
- Automatic navigation and charging
- No dependency on workforce availability
- More meticulous cleaning thanks to precise navigation
- Hasse-free scaling
6. Automatic Truck Loading
One of the primary goals of warehouse logistics automation is to use trucks as efficiently as possible. Automatic truck loading is one of the rising warehouse automation trends that help minimize the idling time of lorries with the help of robots that can move heavy cargo.
The system comprises a large platform with rollers. Workers or robotic arms place palettes with assets on the platform in a storage facility.
When a new truck arrives, the platform automatically moves all the palettes into a truck. No labor force is required at this stage. Consequently, a lorry gets loaded fast and hassle-free. The system can unload cargo efficiently as well.
The use of the automatic truck-loading system helps achieve the following:
- Reduce truck idling time
- Load and unload a truck fast
- Increase the performance of a warehouse
- Improve safety
- Reduce demand in the labor force
Integrating the automatic truck loading system with logistics software is recommended. Consequently, it can calculate the loading time and build accurate schedules automatically.
7. Wearables
Wearables are small devices that can be used by personnel. They help facilitate operations and enhance productivity.
They can guide workers and help them manage inventory faster. Wearable technologies need to have an internal source of power. In most cases, they use batteries that need to be replaced or charged. Also, they need to be connected to a network to share and receive data in live time.
The core advantages of using wearables in a warehouse are:
- Enhanced productivity of workers
- More focus on primary tasks
- Improved accuracy
- Better labor management
- Increased safety
The top wearable devices that help streamline warehouse automation are:
- Wearable computers — Small tablets attached to an arm of a worker. The device offers quick access to a warehouse management system.
- AR-glasses — Glasses that use Augmented Reality technology can display the required information about items on lenses. Consequently, workers don’t need to take external devices to learn more about a package. Also, they can display the direction and distance to the required items to pick.
- Voice headsets — Headphones that enhance voice picking. The device can send voice commands to a server and play answers simultaneously for hand-free item detection.
- Wearable barcode scanners — The device is usually connected to finger-trigger gloves. Workers can point a scanner attached to a hand on a barcode and engage a scanner by touching one finger with another.
- Beacons — It is a device that collects data using built-in sensors. It can track workers’ activity, precisely track their location, and detect idling time. It uses Bluetooth to pair with another device connected to a network for sending data to a WMS.
8. Predictive Maintenance
It is a great solution that has a lot of benefits. It helps reduce downtime and make mechanisms last longer.
In most cases, businesses fix tools and warehousing equipment only when it stops working. However, with predictive maintenance, managers can keep all the mechanisms up and running without unforeseen interruptions.
Predictive maintenance positively affects innovative warehousing. The adoption of this warehouse automation trend can help achieve the following:
- Minimized downtime
- Enhanced safety
- Increased lifespan of equipment
- Well-planned schedule of technicians
- Decreased maintenance and repair costs
The two fundamental types of predictive maintenance are:
- Planned — Maintenance of mechanical equipment is scheduled, and managers get notified about the need to replace parts of mechanisms with the help of warehouse management software. The time of maintenance sessions is calculated automatically based on the usage of tools.
- Preventive — Smart sensors analyze the condition of mechanisms and create reports on the need to maintain tools. Sensors can analyze acoustic information, track vibrations, and even check the visual conditions of instruments and tools. In case any abnormal values get detected, a WMS notifies managers simultaneously.
Build software for predictive maintenance?
9. Voice Picking
It is one of the warehouse automation solutions that help workers increase productivity. It erases the need to use an external device that may distract from performing job responsibilities.
Workers receive commands issued by a WMS in the form of voice instructions. They guide labor on what items should be picked, where they are located, and where they need to be delivered. The voice-picking technology implies a headset connected to a warehouse management system.
Some advanced voice-picking systems offer the opportunity to clarify instructions and have conversations with digital voice assistants.
The benefits of adopting the voice-picking technology are:
- Hand-free interactions with a WMS
- Improved performance and accuracy
- Lowered risk of human error
- Enhanced productivity
10. Sustainable Warehousing
Sustainability is a new warehouse automation trend in the industry. Many businesses strive to reduce the negative impact on the environment by adopting new warehouse automation systems.
The top most popular techniques and solutions that promote sustainable warehousing are:
- Solar panels and wind turbines
- Adoption of power-efficient technologies
- Meticulous climate control on premises
- Efficient storage space usage
- Materials reusing and recycling
The use of renewable energy generators like solar panels and wind turbines helps reduce utility bills and enhance energy independence.
Moreover, excessive energy generated can be emitted to the grid. In such a case, businesses can earn money by generating electricity and selling it.
Warehouse Automation Statistics
Let’s take a closer look at the statistics on warehouse automation development and the market growth.
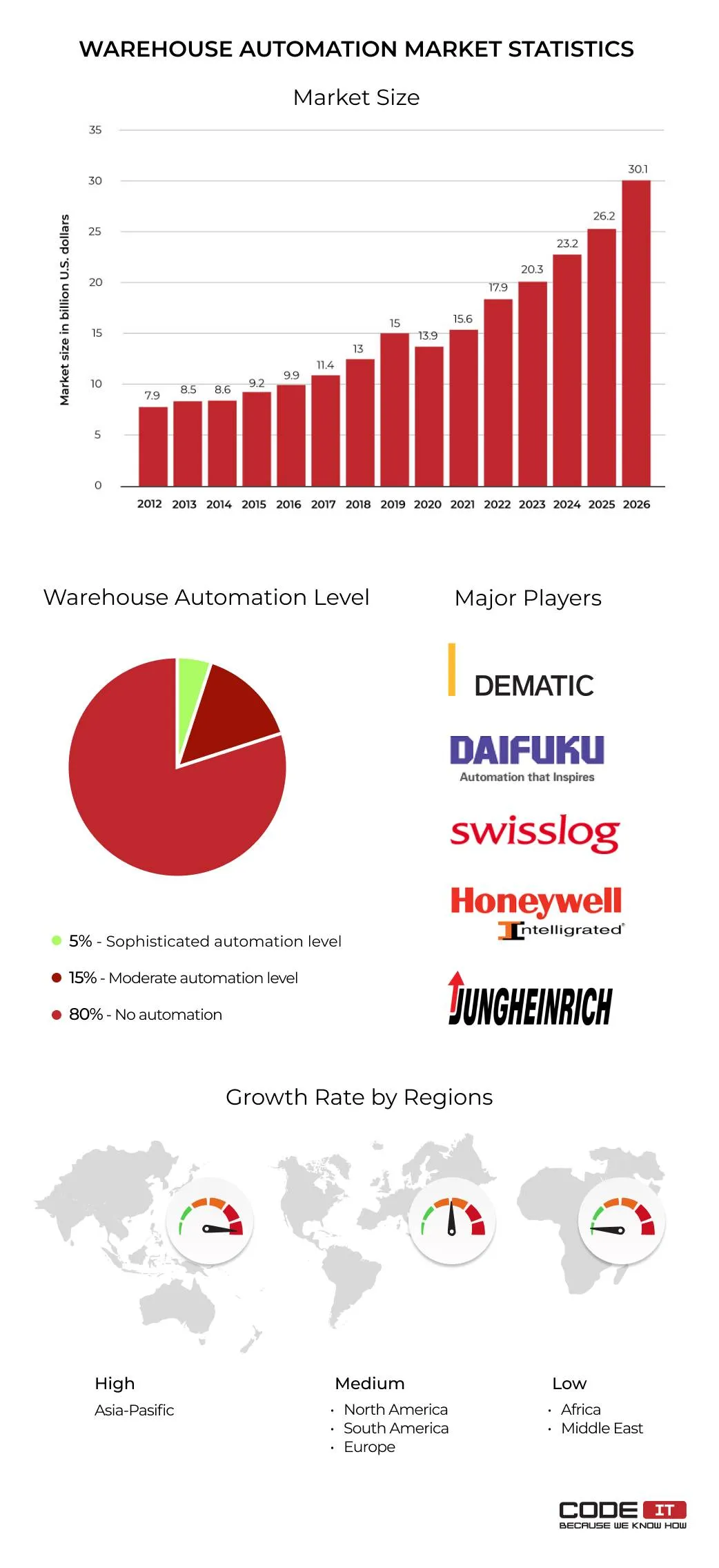
The automation levels across the industry include:
- 5% — sophisticated automation level
- 15% — moderate automation level
- 80% — low automation level
87% of companies plan to enable/expand warehouse automation by investing in:
- 49% — warehouse management systems
- 40% — conveyors and sortation equipment
- 25% — actuators and robotics
- 14% — automated guided vehicles
Warehouse Automation Drivers
The foremost intentions for implementing warehouse automation technology trends include the following:
1. Labor Shortage
The lack of labor and/or high cost of labor make it challenging for business owners to rely solely on manual operations in warehousing. Moreover, the shortage of skilled workers makes it difficult for enterprises to scale up their operations fast.
Statistics: More than 70% of businesses have reported having trouble hiring qualified workers.
2. Demand for Fast Delivery
Businesses implement fast or same-day delivery practices, striving to gain a competitive advantage. Hence, they need to optimize processes and enable automation to meet the customers’ demand for fast delivery.
Statistics: 4 out of 5 stakeholders report that automation helps achieve faster order fulfillment.
3. Operational Efficiency Improvement
The implementation of warehouse automation technology trends helps stakeholders optimize workflows and improve operational efficiency. They manage to automate data-sharing and repetitive tasks.
Statistics: 62% of business owners report that human error elimination is the #1 reason for warehouse automation implementation.
Final Words
The future of warehouse automation is shaped by the following trends:
- Robotic arms
- Automated storage and retrieval
- Drones
- Industrial IoT
- Automatic cleaning
- Automatic truck loading
- Wearables
- Predictive maintenance
- Voice picking
- Sustainable warehousing
The foremost drivers for implementing warehouse automation for most businesses are:
- Labor shortage
- Demand for fast delivery
- Operational efficiency improvement
FAQ
The future of warehouse automation is the usage of connected solutions operated by centralized software. The top warehouse automation ideas include:
- Cross-system data sharing
- AI-driven data analysis
- Repetitive task automation
- Worker assistance and guidance
The top ten warehouse automation technology trends are:
- Robotic arms
- Automated storage and retrieval
- Drones
- Industrial IoT
- Automatic cleaning
- Automatic truck loading
- Wearables
- Predictive maintenance
- Voice picking
- Sustainable warehousing
As per the interviewed stakeholders, the foremost drivers for implementing warehouse automation are:
- Labor shortage
- Demand for fast delivery
- Operational efficiency improvement
Statistics say that only 5% of warehouses are fully/nearly fully automated. 15% of warehouses have a moderate level of automation. The remaining 80% have a low warehouse automation level.
Related services and industries
Logistics Software Development
Get solutions designed to streamline operations
Build your ideal
software today
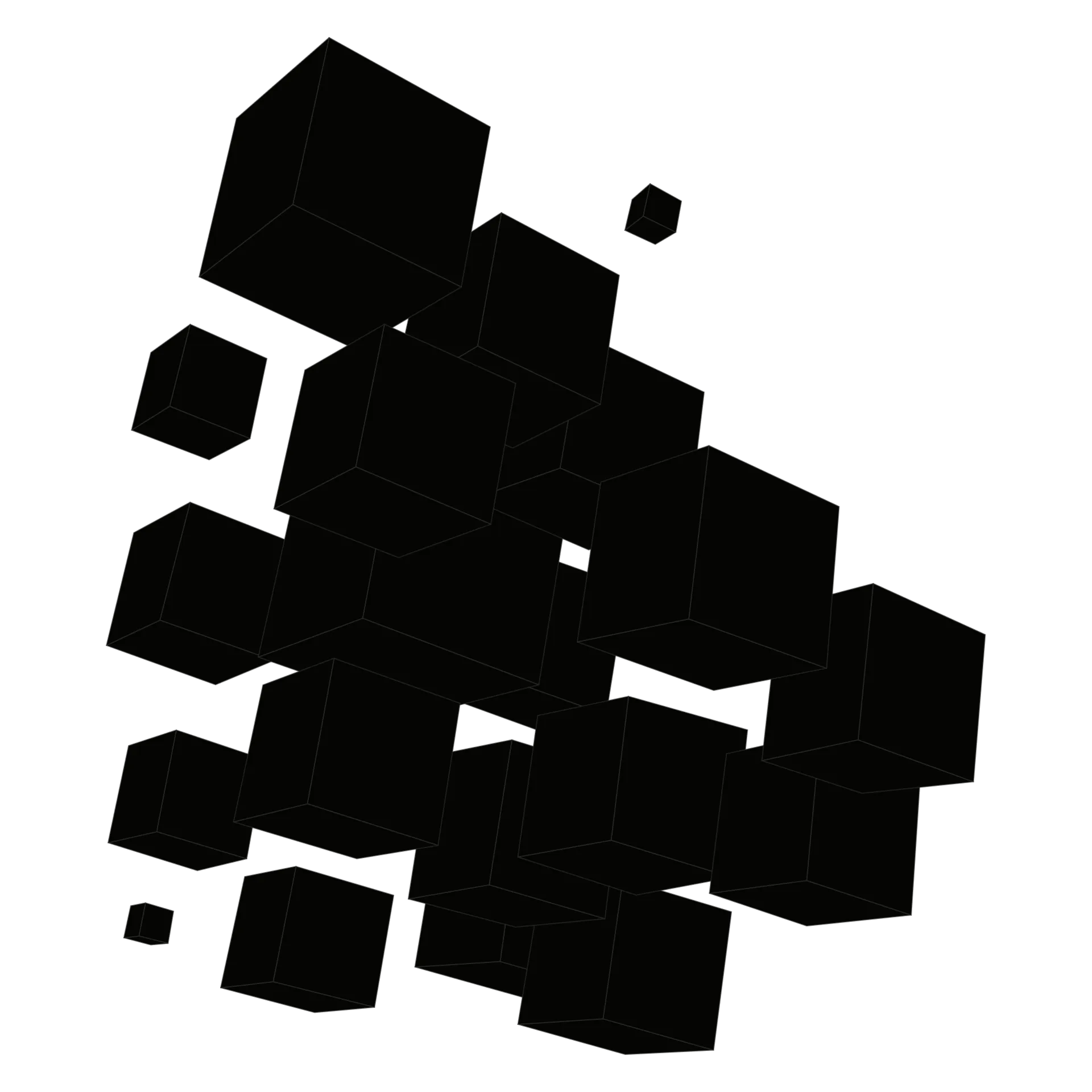