Manufacturing Visibility: Real-Time Insights and Analytics
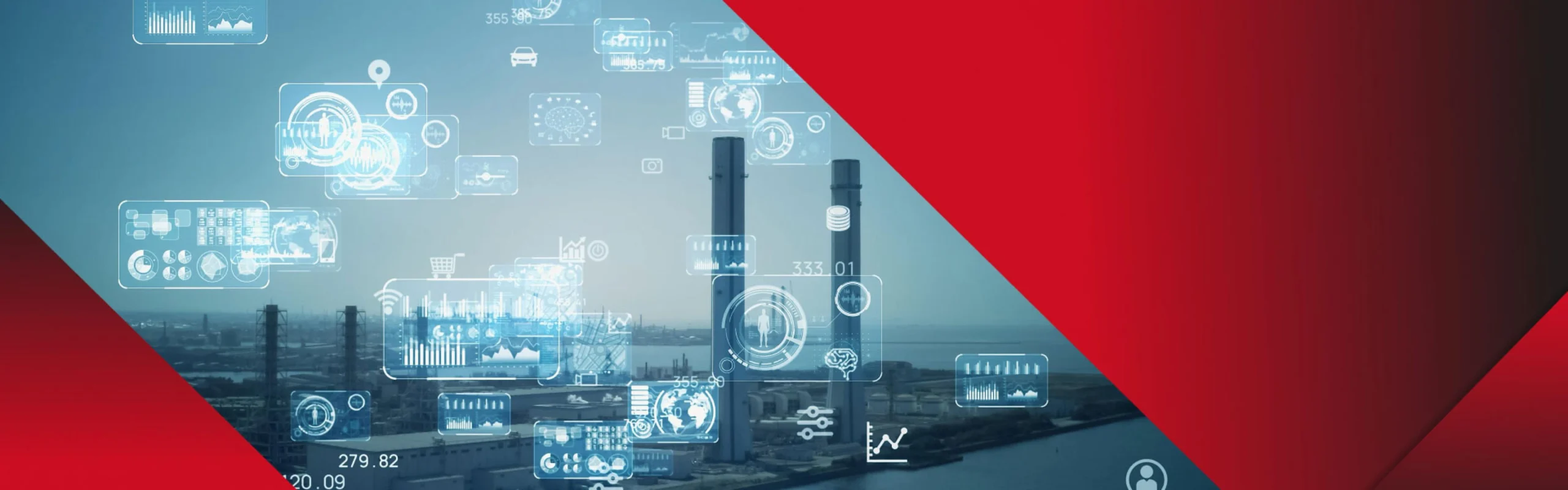
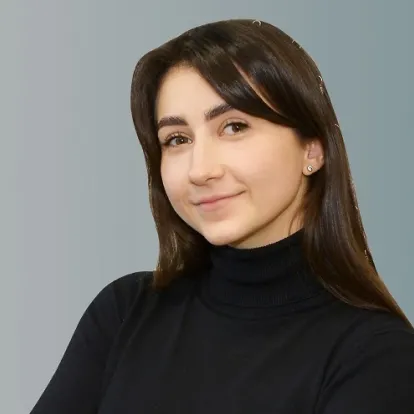
Manufacturing visibility describes the ability of stakeholders to track all processes meticulously using a centralized solution. It is enabled by the implication of Industry 4.0 technologies capable of capturing, pre-processing, and sharing data in real time.
The foremost outcomes of implementing manufacturing visibility are:
- real-time production information access
- increase overall equipment effectiveness
- improved quality control
- reduced operational expenses
- better agility and awareness
- data-driven decision making
The data collected from shop floor machines and smart devices is analyzed using advanced technologies like artificial intelligence and big data analytics. The integration of manufacturing execution systems (MES) helps track all the information about shop floor machines in real time using a centralized solution.
Build custom manufacturing visibility system
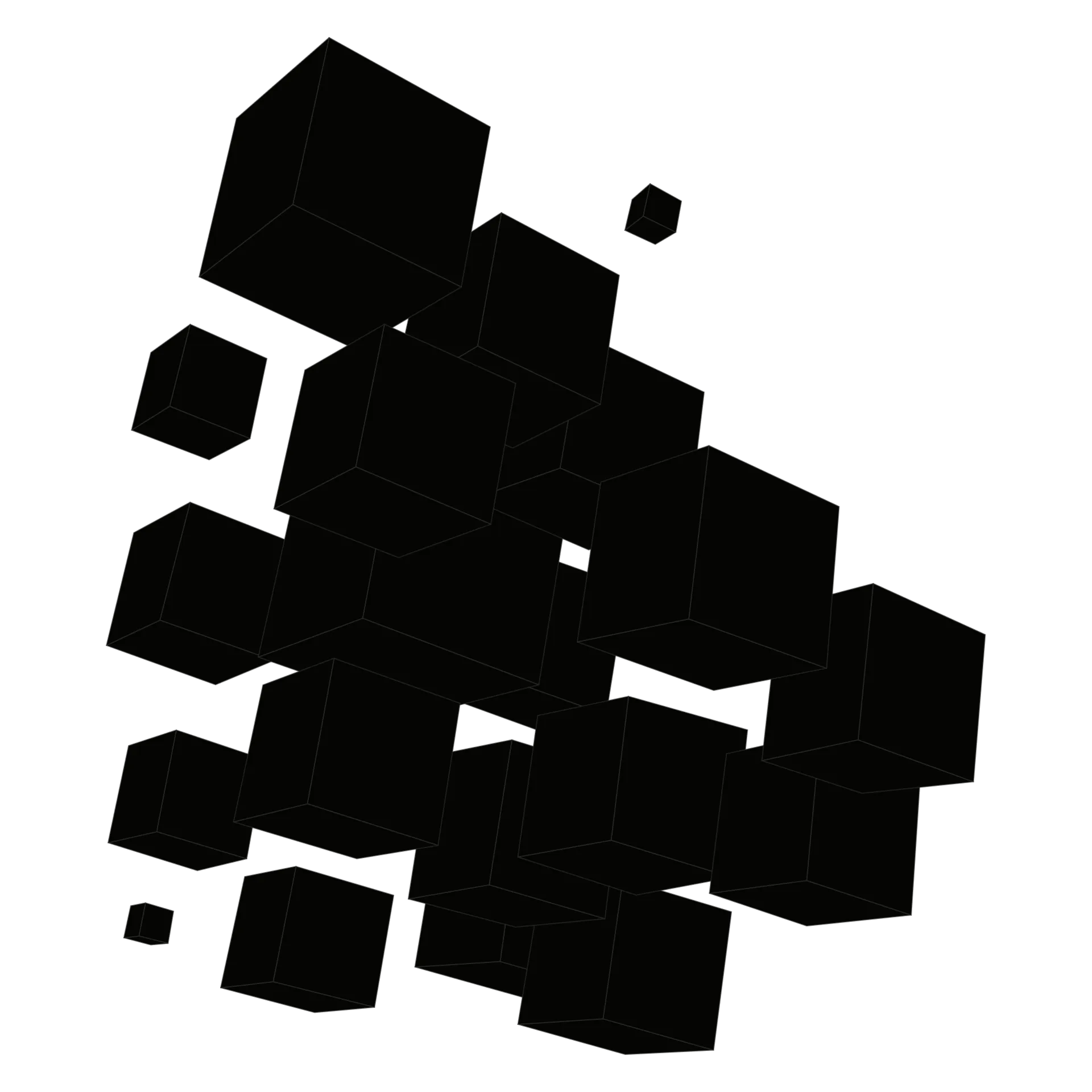
Business First
Code Next
Let’s talk
How manufacturing visibility works
The foremost Industry 4.0 technologies utilized include the Internet of Things (IoT), cloud computing, network devices, and programmable logic controllers (PLCs).
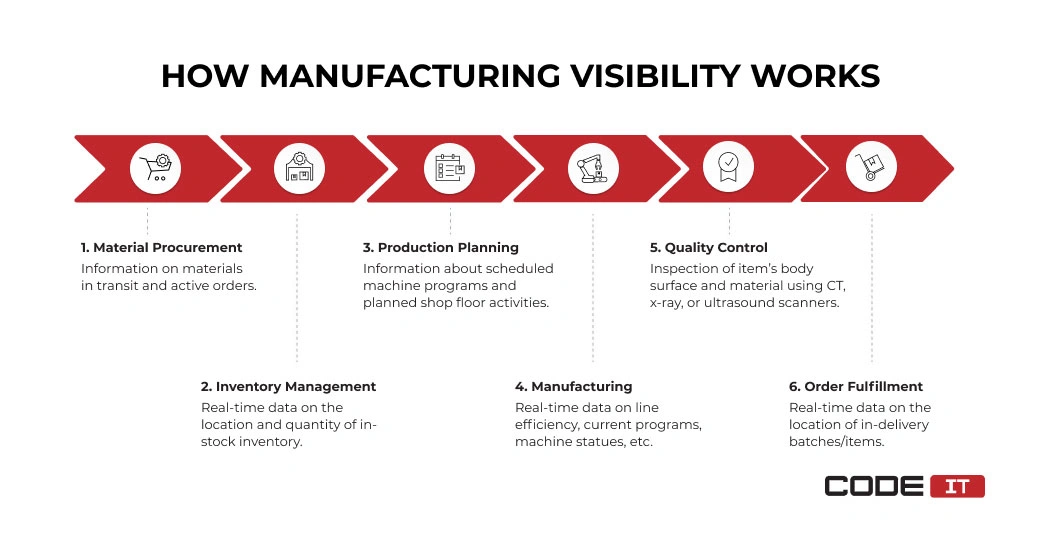
Discover how data visibility helps improve manufacturing efficiency by exploring production stages and the impact of technologies.
1. Material Procurement
Process description: The purchasing of new raw materials or pre-processed components used for further assembly.
Manufacturing visibility application: Get instant info on materials in transit and active orders. Use a centralized software solution for managing vendor relationships.
2. Inventory Management
Process description: Storage of raw materials and finished items. In-stock level monitoring and material replenishment.
Manufacturing visibility application: An automated unique device identification (UDI) system helps track the location and quantity of received/stored goods. Moreover, the integration with supply chain visibility software unlocks the opportunity to implement automated item replenishment or vendor-management inventory practices.
3. Production Planning and Scheduling
Process description: Planning of production operations, creation of programs for shop floor machines, and scheduling.
Manufacturing visibility application: Check information about upcoming programs to execute by machines and planned activities. The integration with the manufacturing execution system (MES) enables the opportunity to adjust parameters depending on labor shifts, order priorities, etc.
4. Manufacturing
Process description: The execution of machine programs to transform raw materials into finished products and parts assembly.
Manufacturing visibility application: Internet of Things (IoT) devices like smart sensors and UDI scanners capture shop floor data and transfer it to the central dashboard. The data helps understand the operational efficiency of line machines, manufacturing progress, current machine status, etc.
5. Quality Control
Process description: The inspection of finished products to ensure they meet defined quality standards.
Manufacturing visibility application: Smart cameras and sensors inspect items’ assembly. CT, x-ray, or ultrasound scanners analyze the body material of finished goods. Stakeholders receive notifications when item detections are detected.
6. Order Fulfillment and Shipping
Process description: This stage involves item picking, packing, and shipping. It may also involve collecting and analyzing customer feedback.
Manufacturing visibility application: Barcode and RFID scanners automatically monitor the movement of items and packages in a shop floor and warehouse. GPS-enabled telematics devices help trace the delivery of batches or separate items in real time.
Problems solved by manufacturing visibility
Instant access to shop floor data and data-backed analytics helps stakeholders fix inefficiency and solve production management problems.
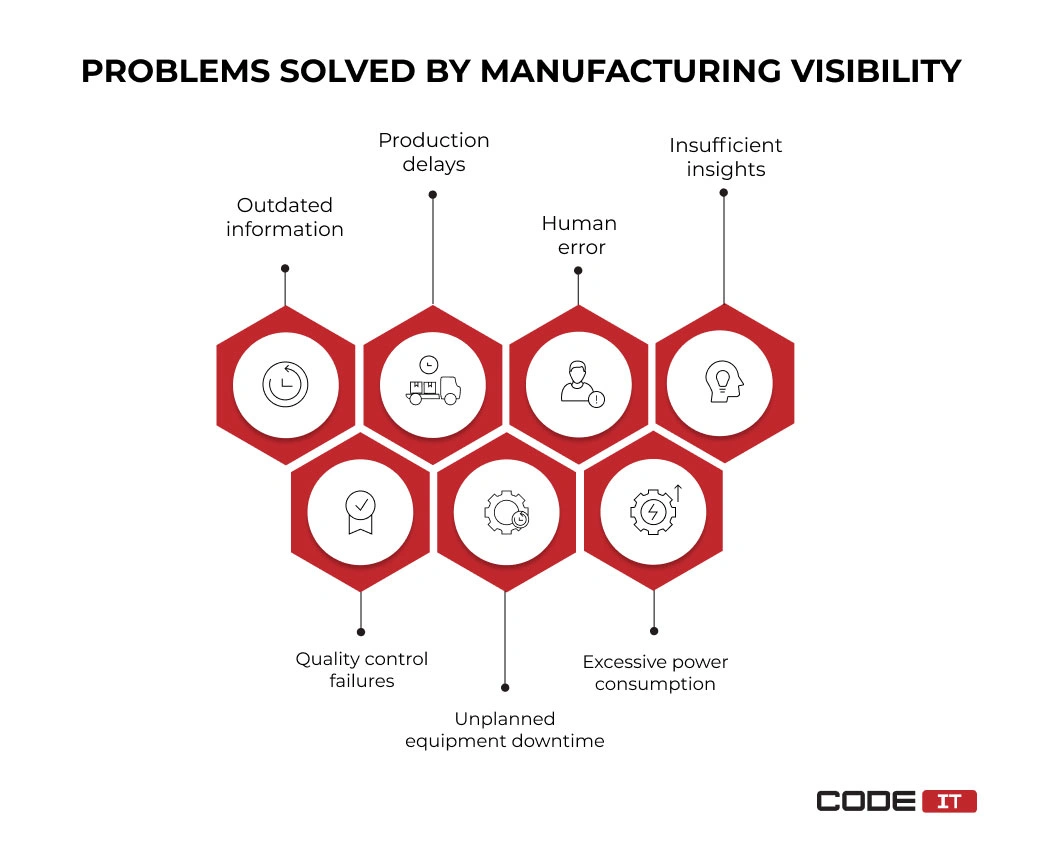
Outdated Information and Lack of Awareness
Stakeholders need to use isolated solutions to check the current programs, in-stock inventory levels, defect rates, idling machines, and other crucial metrics. Non-digitized shop floors collect data manually using spreadsheets.
Hence, they are not fully informed about manufacturing operations and problems. Besides, stakeholders may receive crucial information with delay.
Manufacturing visibility-driven solution: Automated data collection and processing eliminates the need for manual input. Moreover, algorithms can validate the data employees enter manually and notify them when possible errors are detected.
Production Delays
Unforeseen machine downtime, supply chain disruptions, or human error are the foremost reasons for production delays. Due to the lack of manufacturing visibility, stakeholders experience issues with responding to production challenges quickly.
Manufacturing visibility-driven solution: Real-time monitoring of shop floor operations helps identify early-stage bottlenecks. Furthermore, business intelligence (BI) solutions can analyze real-time data and deliver insights on potential supply chain or production issues.
Human Error
Manual data entry and collection can lead to an increased number of errors and misleading data processing. Also, it promotes workforce utilization inefficiencies.
Manufacturing visibility-driven solution: Automated data collection and processing eliminates the need for manual input. Moreover, algorithms can validate the data employees entry manually and notify when possible errors are detected.
Insufficient Insights
As per statistics, the lack of relevant data is the top issue that keeps stakeholders from generating useful insights. They report an incapability to conduct deep analysis to extract valuable insights and discover root causes.
Manufacturing visibility-driven solution: Integrated solutions and cross-system data-sharing pipelines enable access to actionable insights reaped from raw data.
Unlock the potential of your data
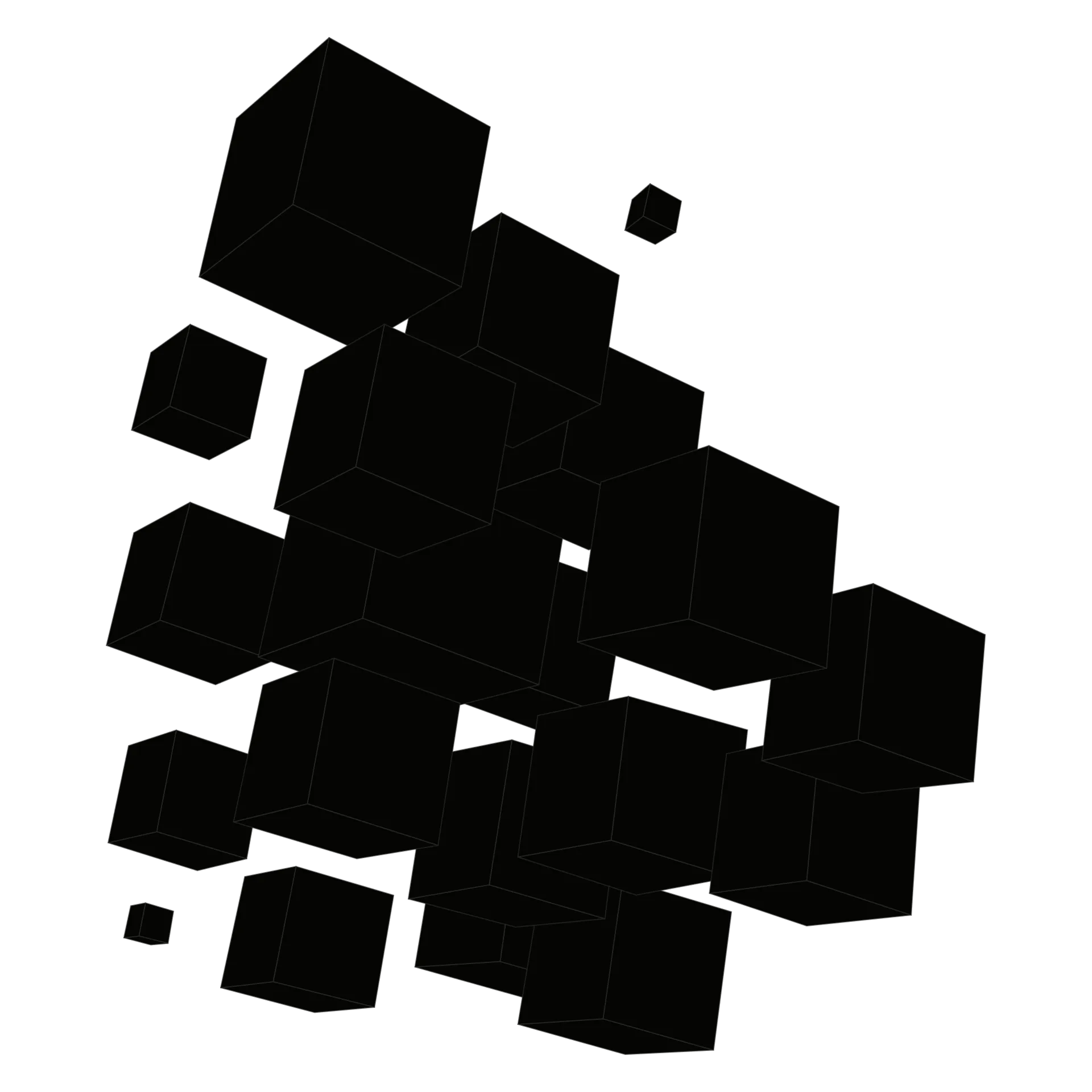
Business First
Code Next
Let’s talk
Quality Control Failures
The manual inspection of produced items is an inefficient way to detect defects. It can lead to the wastage of materials and energy. Also, batch recall can cause significant expenses.
Manufacturing visibility-driven solution: Automated inspection of produced items using advanced technologies helps identify defects in real time. It enables the opportunity to respond fast when item defects are detected.
Unplanned Equipment Downtime
The lack of manufacturing data causes the inability to enable predictive maintenance. Therefore, unforeseen machine failures can stop production and cause delivery delays.
Manufacturing visibility-driven solution: The data collected by smart sensors and IoT devices helps monitor equipment health and detect anomalies. BI solutions are used to identify possible equipment failures. They also deliver alerts notifying stakeholders about critical issues on the shop floor.
Excessive Power Consumption
The lack of manufacturing visibility doesn’t allow stakeholders to fully understand electricity consumption, which results in increased bills and an environmental footprint.
Manufacturing visibility-driven solution: Smart meters and energy monitoring systems provide real-time analytics on electricity consumption in a shop floor.
MES System Architecture
Manufacturing visibility technologies
The key hardware and software solutions used for automated data collection, sharing, and analysis are as follows.
- Internet of Things (IoT). Sensors and smart devices with Internet connectivity. IoT devices collect, pre-process, and share data in real time.
- Network devices. Routers, switches, wires, and other hardware used for creating local networks for transferring manufacturing data.
- Cloud computing. Dedicated servers are installed in a remote location that a third-party vendor manages. It is used to store and process shop floor data.
- Business intelligence software. Software solutions that help turn raw data into actionable insights. BI solutions are used for data visualization, analysis, forecast demand, and data-driven decision-making.
- MES integration. The application programming interface (API) enables the opportunity to connect third parties, enabling seamless data flow between diverse software solutions.
- Data transformation middleware. Data gathered from multiple sources and diverse machines may need additional cleansing and transformation to be processed by a single software solution.
Supply Chain Visibility Software
How to implement manufacturing visibility
There is no plug-and-play solution for enabling manufacturing visibility. Hence, a thorough assessment of the existing infrastructure, business goals, and technical capabilities is required.
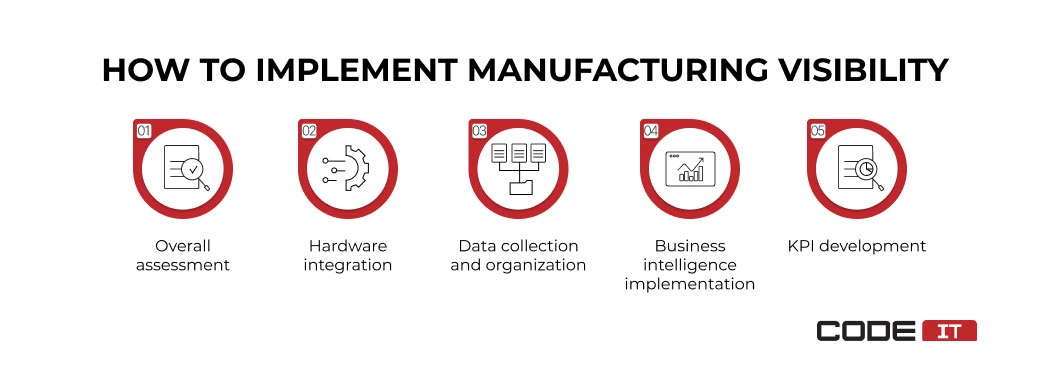
These five manufacturing visibility implementation stages are crucial for creating an integrated system without manual data input and analysis.
1. Overall Assessment
Analyze the existing shop floor machines and equipment to understand the starting point and infrastructure readiness. Also, it’s crucial to identify business goals for defining the best tools and technologies for implementing manufacturing visibility.
2. Hardware Integration
Integrate IoT devices, PLCs, and smart sensors for collecting line data. Also, it’s required to develop a local network and configure an on-premise or cloud-based server for storing and processing collected data.
On-Premise vs Cloud
3. Data Collection and Organization
Organize a repository for storing data collected from the shop floor. If a product line comprises machines from different vendors, middleware development may be required. For instance, additional data mapping tools need to validate and transform the collected data before sending it to the main repository.
4. Business Intelligence Implementation
Install and configure business intelligence solutions that turn raw data into actionable insights. BI solutions help visualize collected data and display charts on custom dashboards. If real-time data sharing is configured, the data is updated simultaneously.
Moreover, BI systems are capable of conducting deep analysis using advanced technologies like artificial intelligence and generating custom reports.
5. KPI Development
Analyze the manufacturing data to develop key performance indicators (KPIs). These are used to understand machine performance drops/rises and detect anomalies. Also, benchmarking helps set new business goals and check if they are achieved, measuring progress in numbers.
We can tap into your project now!
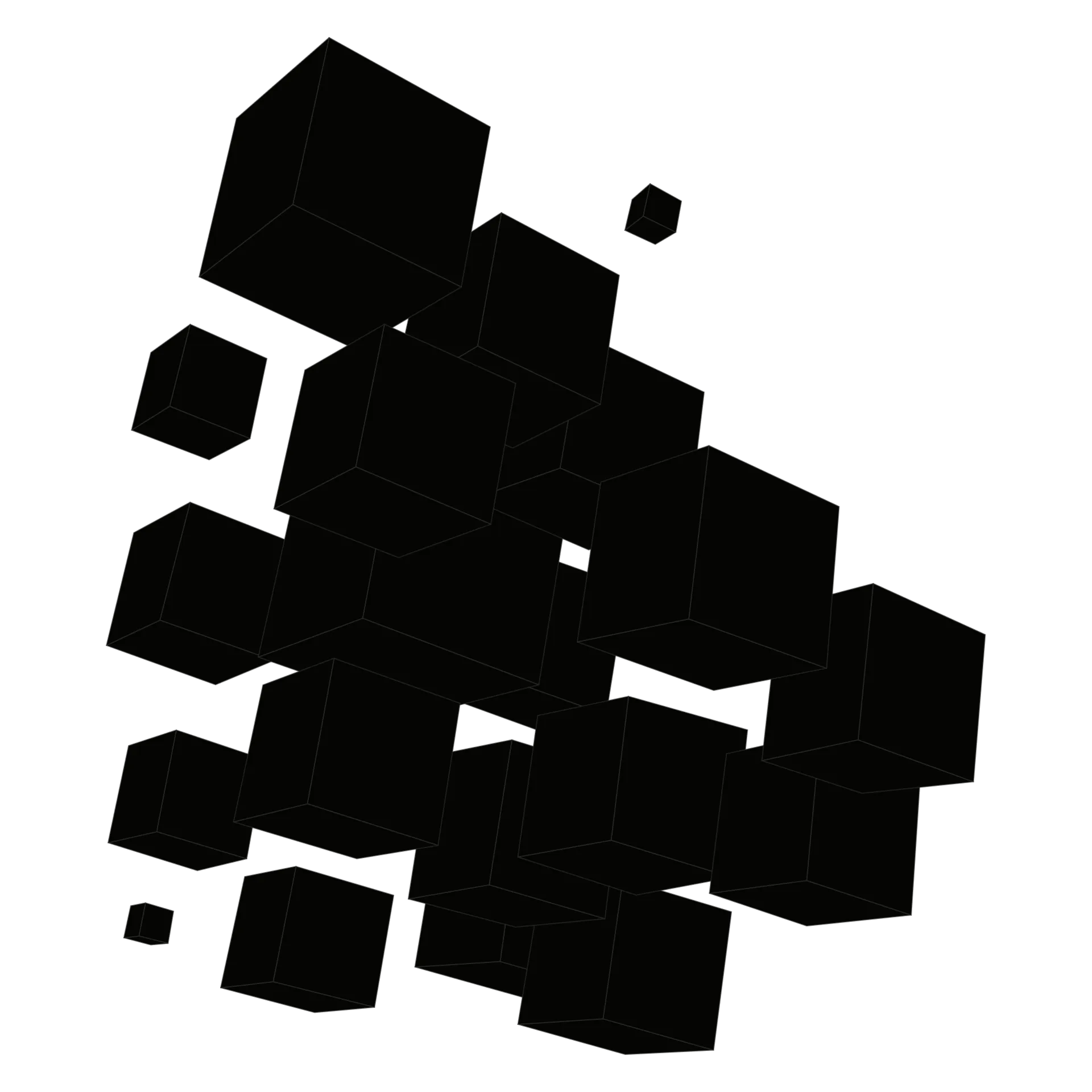
Business First
Code Next
Let’s talk
Real-world manufacturing visibility use cases
Manufacturing visibility is widely implemented by companies that produce/assemble items worldwide due to its benefits. Moreover, the implementation of real-time visibility solutions unlocks the opportunity to optimize processes and enable automation.

These top three companies have successfully implemented manufacturing visibility and improved their production processes.
1. Magna International
The company is a leader in the automotive manufacturing niche. It has implemented manufacturing visibility solutions to eliminate idling machines and achieve maximum operational efficiency.
Result: The real-time shop floor visibility enabled the opportunity to identify production disruptions and respond rapidly. The company has achieved a 40% increase in on-time deliveries. Also, it has doubled shipments without hiring new staff by optimizing workflows using the received insights.
2. Univar Solutions
The company is focused on producing chemicals and ingredients for global markets. Possible disruptions or late deliveries cause the company’s clients to lose hundreds of thousands of dollars per hour due to the large production scale.
Result: The implementation of real-time visibility solutions helps the company to meticulously track all the processes and receive notifications if unforeseen issues are detected. It enables the opportunity to respond immediately, promoting downtime reduction.
3. Robert Bosch GmbH
This German-based company is widely recognized as Bosch. It is one of the largest technology and engineering companies with many manufacturing sites around the globe. The company always implements innovative solutions for production monitoring and continuous improvement of processes.
Result: The company has installed IoT sensors and devices to enable smart manufacturing in its production sites. The implementation of IoT has helped the company to optimize supply chain management. Also, it has enabled predictive equipment maintenance and AI-driven demand forecasting.
CodeIT expertise — machine uptime monitoring software
The CodeIT team of five experts has developed a feature-rich plant floor monitoring software and integrated it with the existing MES.
Problem
The client is a manufacturer with more than a 30-year experience in the industry. He wanted to revamp the production processes by enabling digitalization. Our team was requested to create a solution for monitoring machine programs and analyzing the collected data.
Solution
We have analyzed business requirements and prepared a detailed solution development plan. The team of software engineers dedicated to the project has implemented the following:
- Dashboard — all the data from machines is displayed on the central screen.
- Data visualization — a BI solution visualizes the raw data collected from machines.
- Report generation — custom reports are generated automatically to track crucial metrics.
- Machine status viewer — the ability to simultaneously check a machine’s program using an MES.
- System permission configuration — all user roles have custom permissions that the admin user can update upon a need.
Want to learn more about the development process?
Wrapping up
Manufacturing visibility describes the stakeholders’ opportunity to track shop floor operations in real time using a centralized solution. It is implemented by Industry 4.0 technologies, including IoT, cloud computing, AI-driven data analysis, etc.
The foremost ways how data visibility helps manufacturing efficiency are:
- real-time manufacturing data access
- workflow analysis and optimization
- automated quality control
- data-driven decision making
Supercharge your production with custom software
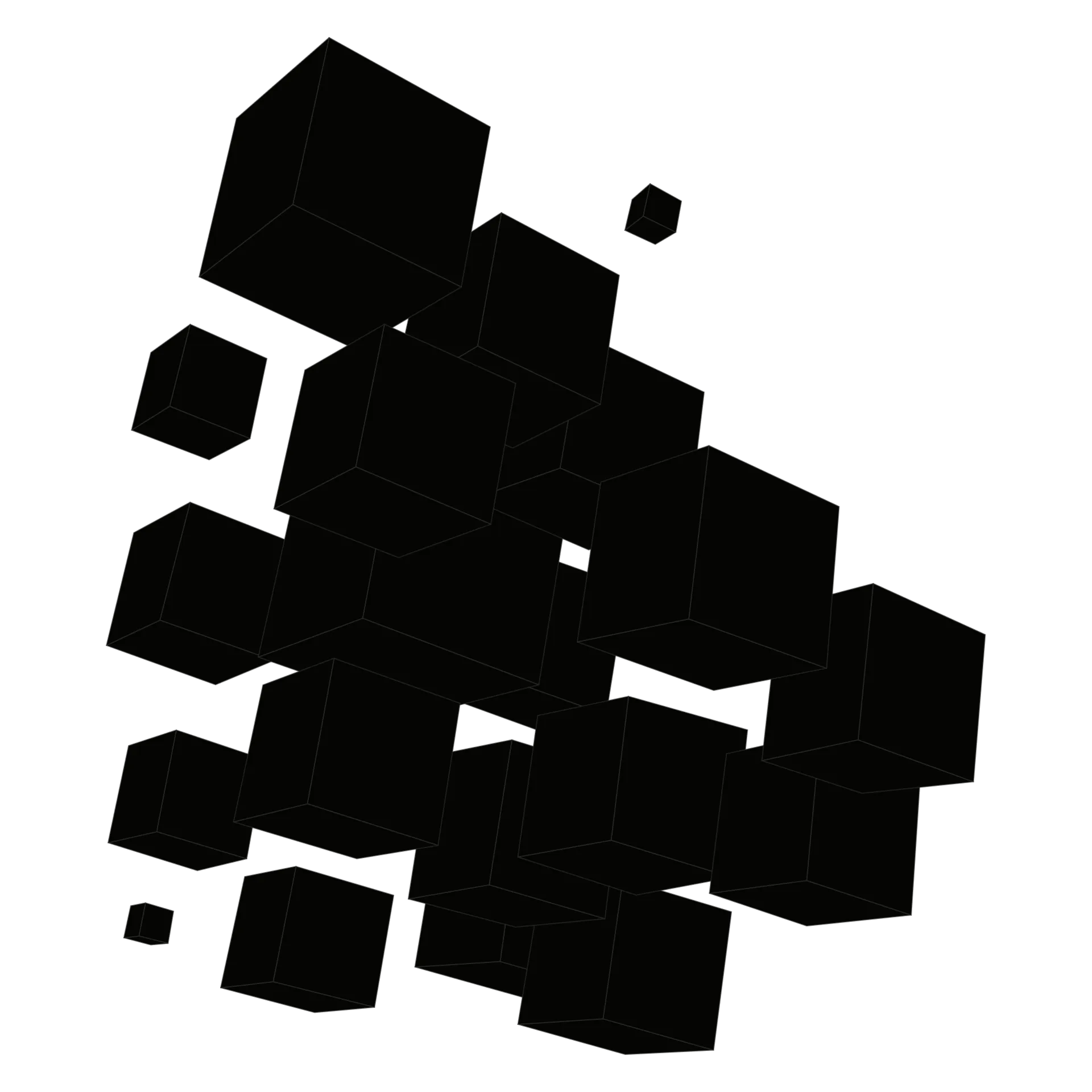
Business First
Code Next
Let’s talk
FAQ
The manufacturing visibility is enabled by implementing Industry 4.0 technologies, including the following:
- Industrial internet of things (IIoT)
- Big data analytics
- Manufacturing execution systems (MES) integration
- Big data analytics
The insights extracted from the analyzed data help stakeholders to do the following:
- Detect bottlenecks
- Run predictive maintenance
- Monitor item quality automatically
- Make data-backed decisions
The three real-world applications of manufacturing visibility implementation are:
- Magna International: a 40% increase in on time deliveries thanks to fast manufacturing disruptions identification and response.
- Univar Solutions: real-time performance tracking and notifications when disruptions are detected
- Robert Bosch GmbH: analyze data collected by sensors and IoT devices to optimize processes and increase productivity.
The implementation of manufacturing visibility comprises five crucial stages, which are listed below.
- Overall assessment. Analyze the as-is architecture to outline the starting point of digital transformation. Also, business goals should be defined to pick the best tools and technologies.
- Hardware integration. Implement IIoT devices and smart sensors. Also, a local network must be developed to connect all the devices.
- Data collection and organization. Implement an on-site or cloud-based server for storing and processing collected shop floor data.
- Business intelligence implementation. Develop a BI solution for visualizing manufacturing data and extracting insights.
- KPI development. Set key performance indicators to understand the drop/rise in production performance.
Build your ideal
software today
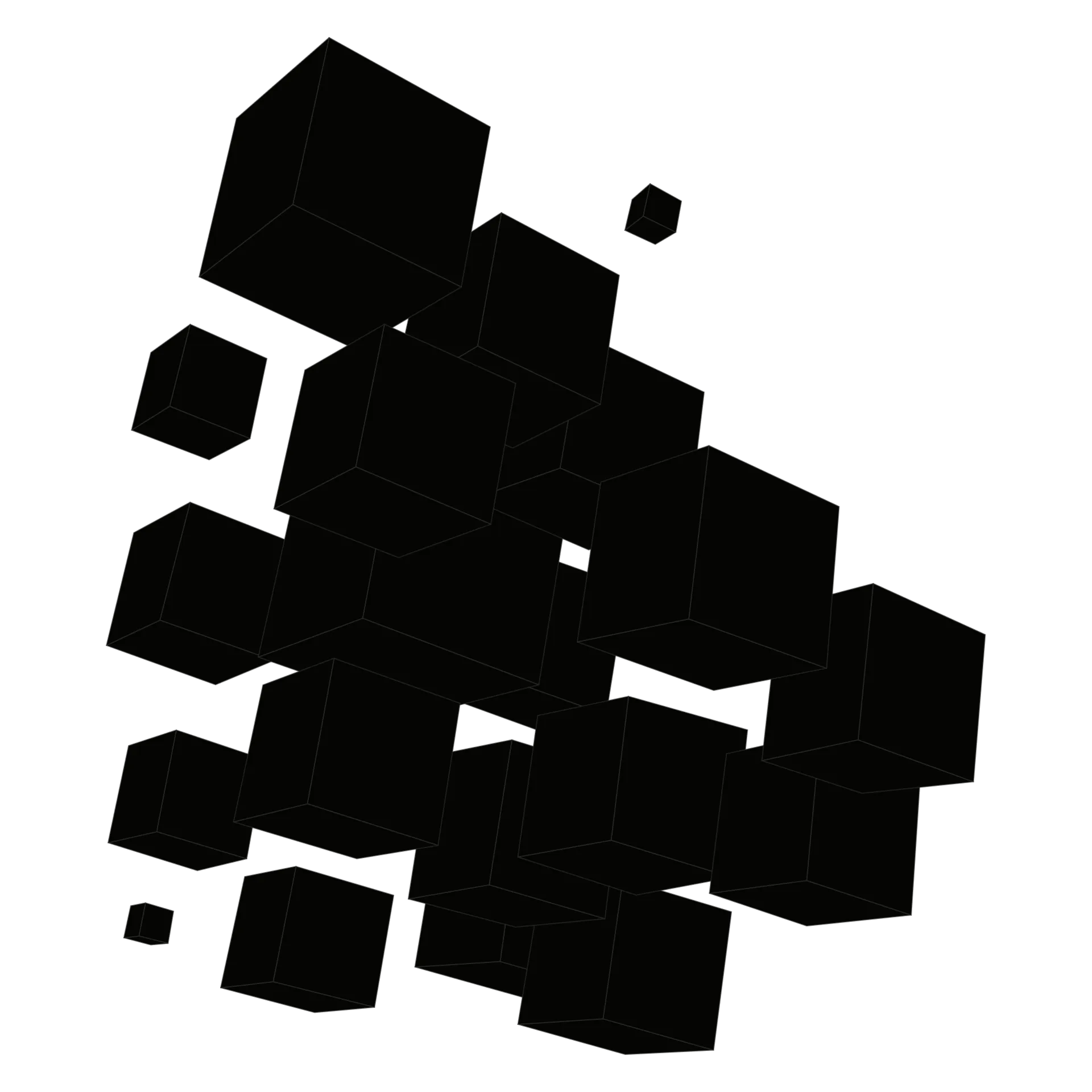