Manufacturing Data Analytics
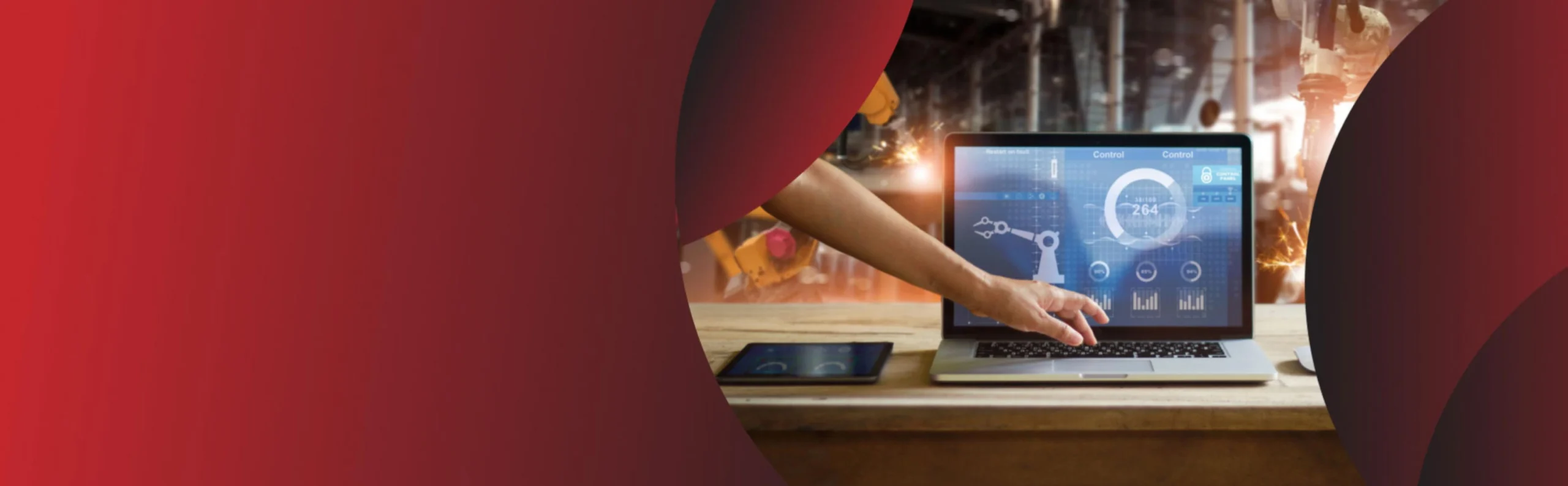
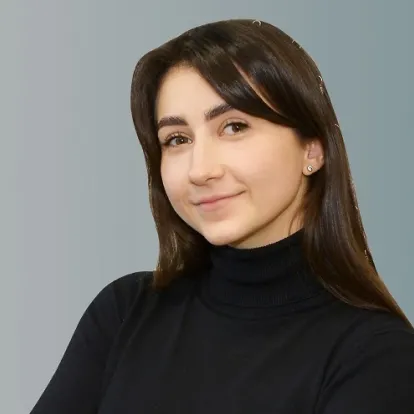
What is manufacturing analytics? It is a crucial component of Industry 4.0 that describes the process of collecting information from shop floor machines and processing it. The datasets can be visualized and used for extracting insights.
Manufacturing data analytics solutions refer to HMIs, MES, SCADA, business intelligence software, machine learning (ML), data logger tools, etc. The solutions are interconnected to enable automated data sharing, analysis, and insight delivery pipelines.
The implementation of analytics in the manufacturing industry unlocks the following:
- live-time analytics and alerts
- data visualization and automated reports
- predictive maintenance
- data-baked forecast development
- bottleneck detection and root cause analysis
How data analytics in manufacturing works
Data analytics in manufacturing help transform raw data into insights or actionable instructions tailored to custom business needs.
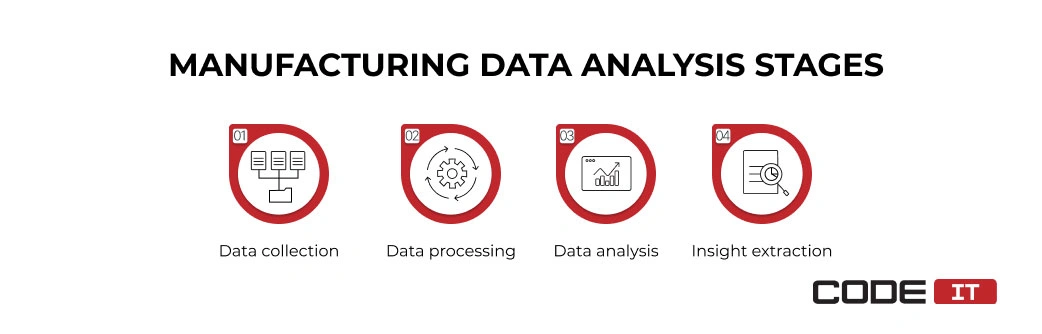
The core four stages of manufacturing data analytics are as follows.
- Data collection. Gathering data from sensors installed on a shop floor.
- Data processing. Large amounts of data are checked, validated, and transformed.
- Data analysis. Mathematical algorithms and machine learning models process data to detect trend changes, patterns, etc.
- Insight extraction. Data analysis outputs are interpreted into easy-to-understand insights and actionable recommendations.
The variety of data and insights delivered by manufacturing analytics solutions depends on business needs.
The foremost solutions and outputs of manufacturing business analytics are as follows.
Technologies/Hardware | Data Analysis Process | |
---|---|---|
Dashboard and Reports | Sensors, IoT devices, PLCs, RFID tags. | Data is collected and transferred to the central server. It is processed and displayed on a dashboard. Custom reports are generated upon a need. |
Machine Failure Alerts | Vibration sensors, temperature sensors, IoT devices. | Digital systems analyze data in real-time and deliver failure alerts if anomalies/critical issues are detected. |
Quality Control Reports | Cameras, sensors, manual input devices, scanners. | Information about items’ physical characteristics is captured and transferred to the main server. When defects are detected, stakeholders are notified. |
Supply Chain Visibility | RFID tags, GPS trackers, ERP systems, telematics devices. | Data on items’ locations and statuses is tracked and analyzed. Bottlenecks, stockout, or in-progress inventory data is displayed on a dashboard. |
Energy Consumption Review | Energy meters, environmental sensors, IoT devices. | Energy consumption and machine idling time are recorded and analyzed. Energy consumption reports and recommendations are delivered. |
Workflow Optimization | Digital twin, simulation software, customer feedback tools, and market analysis software. | Manufacturing data is used to create a genuine digital copy of a shop floor. A digital twin stimulates activities and discovers ways to optimize workflows. |
Demand Forecast | Machine learning, ERP system, MES, data analysis software. | ML-driven algorithms analyze large amounts of historical data. Seasonal demand change is forecasted, and hidden patterns are identified. |
Power of manufacturing analytics
The usage of data analytics in manufacturing helps companies achieve positive outcomes.
The research highlights the top companies that have achieved positive outcomes by implementing the analytics in the manufacturing industry are as follows.
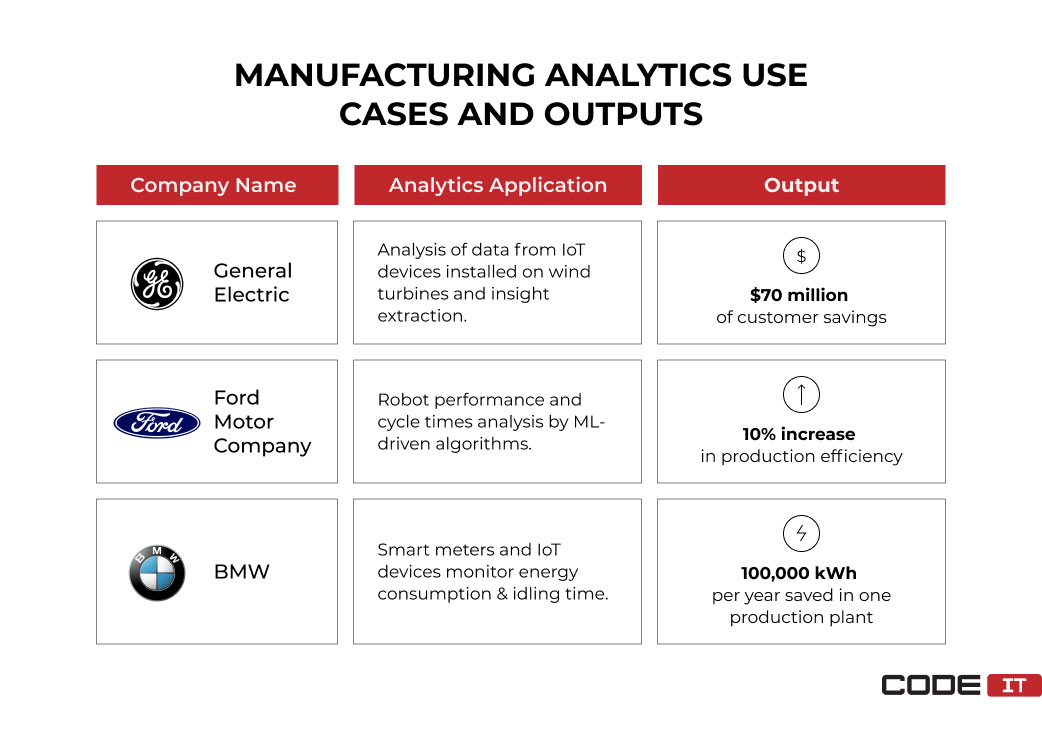
General Electric
The company has installed IoT devices on a fleet of more than 1,500 wind turbines. They collect information on rotor speed and weather conditions. Cloud-based analytics software is used to build predictive maintenance models.
Output: $70 million of customer savings has been achieved thanks to using insights delivered from big data analysis.
Ford Motor Company
The application of machine learning empowers the company’s manufacturing data analytics. Smart algorithms analyze cycle times and robot performance data to detect bottlenecks and discover ways to improve performance.
Output: The 10% increase in production efficiency has been achieved by the company by using the insights delivered by ML.
BMW
BMW uses IoT devices to monitor power consumption at its production plant in Spartanburg (SC, USA). Smart meters and IoT devices measure electricity consumption and machine idle time. The data is analyzed, and insights are delivered to stakeholders.
Output: Excessive energy consumption and anomalies detected by smart algorithms have helped to save 100,000 kWh per year.
Ready to enable process manufacturing analytics?
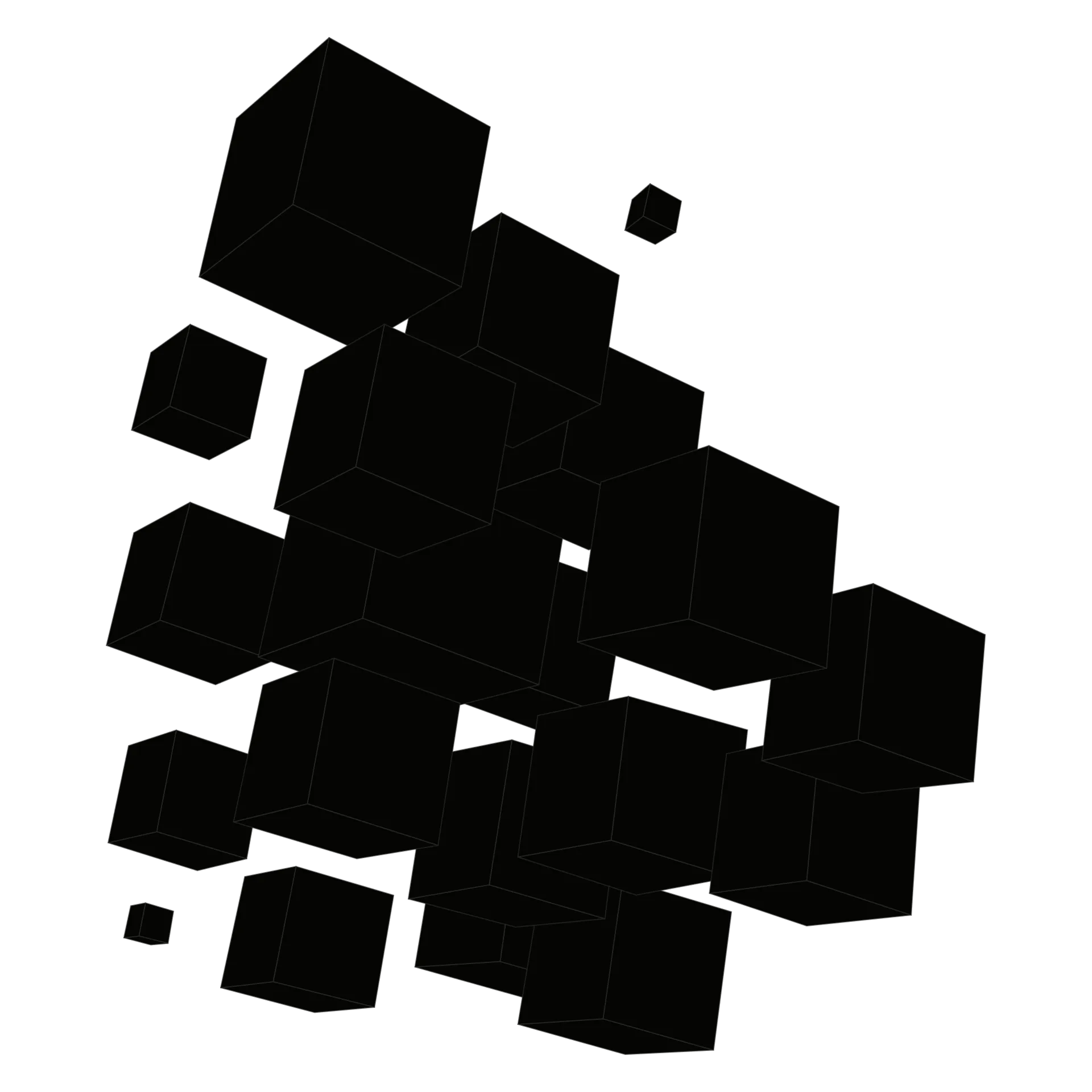
Business First
Code Next
Let’s talk
Applications of manufacturing analytics
Data analytics in the manufacturing industry help optimize processes, monitor the quality of finished goods, forecast demand, and more.
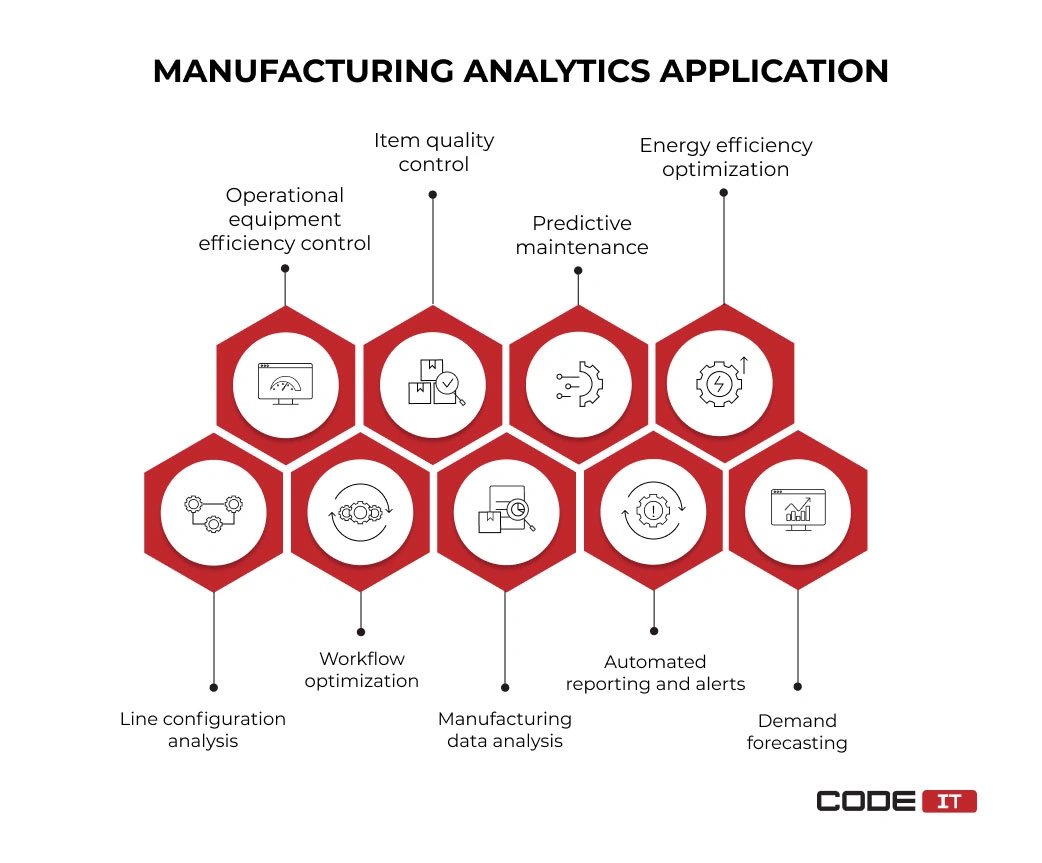
Check out the nine use cases of analytics in the manufacturing sector.
1. Operational Equipment Effectiveness Control
Collect data from machines and smart sensors installed on a production floor. Analyze the data to measure the operational equipment effectiveness (OEE) for machines or plant cells. The data can be summarized and visualized for quick monitoring of key metrics, including:
- downtime
- performance
- defect rate
- idling
- slowdowns
Benefits: The usage of data analytics in manufacturing for optimizing OEE helps enable full visibility of shop floor operations. Moreover, it is useful for detecting bottlenecks, reducing downtime, and discovering ways to improve operational efficiency.
2. Item Quality Control
Smart cameras, sensors, and scanners gather information about items’ physical properties, material composition, component assembly, etc. All the information is processed by algorithms to identify defects. Furthermore, data analytics manufacturing helps define the root causes of detected issues.
Benefits: Continuous quality inspection helps minimize production recalls by quickly identifying defective goods. Data-baked recommendations help better identify problems that cause defects or item assembly errors.
3. Predictive Maintenance
Smart sensors collect and analyze data on vibration, noise, temperature, etc. The analyzed information is used to assess machine health. Algorithms can automatically identify possible technical issues that may occur in the future by detecting anomalies in analyzed data.
Benefits: Minimizes the risk of unplanned downtime. The early detection of equipment malfunction helps reduce repair expenses and increase the lifespan of machine components.
4. Energy Efficiency Optimization
Smart meters track and monitor the electricity consumption of machines and shop floor cells. The insights delivered by analytics in manufacturing are used to identify areas of excessive energy consumption that can be avoided. These include machine idling, needless HVAC spending, and unessential lighting.
Benefits: Lowered bills are the foremost benefit of implementing energy and process manufacturing analytics. In addition, it is useful for improving sustainability and complying with energy regulations.
5. Line Configuration Analysis
Large amounts of data on product line machines are used for running simulations and manufacturing analytics. The digital twin technology enables the creation of a virtual copy of a shop floor. The line configuration can be adjusted and simulated virtually to discover the most optimal line configuration.
Benefits: The opportunity to virtually simulate various product line configurations delivers a cost-effective way to optimize line layouts. Automated data collection and processing reduces the chance of manual error.
6. Workflow Optimization
Business analytics in the manufacturing industry is used to process crucial metrics like human tasks, material handling, machine data, etc. The wide variety of data on manufacturing processes is analyzed. Bottleneck identification and workflow simulation insights are useful for discovering ways to improve workflows.
Benefits: Workflow analysis helps identify inefficiencies in existing processes. Moreover, it highlights automation implementation opportunities to improve productivity and reduce the risk of human errors.
7. Manufacturing Data Visualization
Analytics in the manufacturing industry are widely used to transform large datasets of raw data into easy-to-consume charts. The information displayed on a dashboard is usually updated in real-time. Moreover, users can create custom dashboards to access only the manufacturing data they need, considering business needs.
Benefits: The real-time access to easy-to-consume data improves decision-making. Custom dashboards help rapidly detect anomalies and enable full processes visibility.
8. Automated Reporting and Alerts
Custom reporting is one of the top business analytics in the manufacturing industry. Unique algorithms collect various data and process it to generate reports automatically. The real-time analytics helps instantly detect unforeseen issues and send alerts.
Benefits: Data analytics manufacturing makes stakeholders more informed and improves transparency. Alerts help minimize the resonance time for fixing unforeseen issues quickly.
9. Demand Forecasting
Machine learning, large historical datasets, and manufacturing data analytics tools are combined to generate demand forecasts. ML-driven algorithms are useful for detecting hidden patterns.
Benefits: Generated insights help optimize planning and supply chain strategies. Data-baked insights help minimize inventory holding costs and avoid stockouts.
Hire CodeIT to use analytics in manufacturing
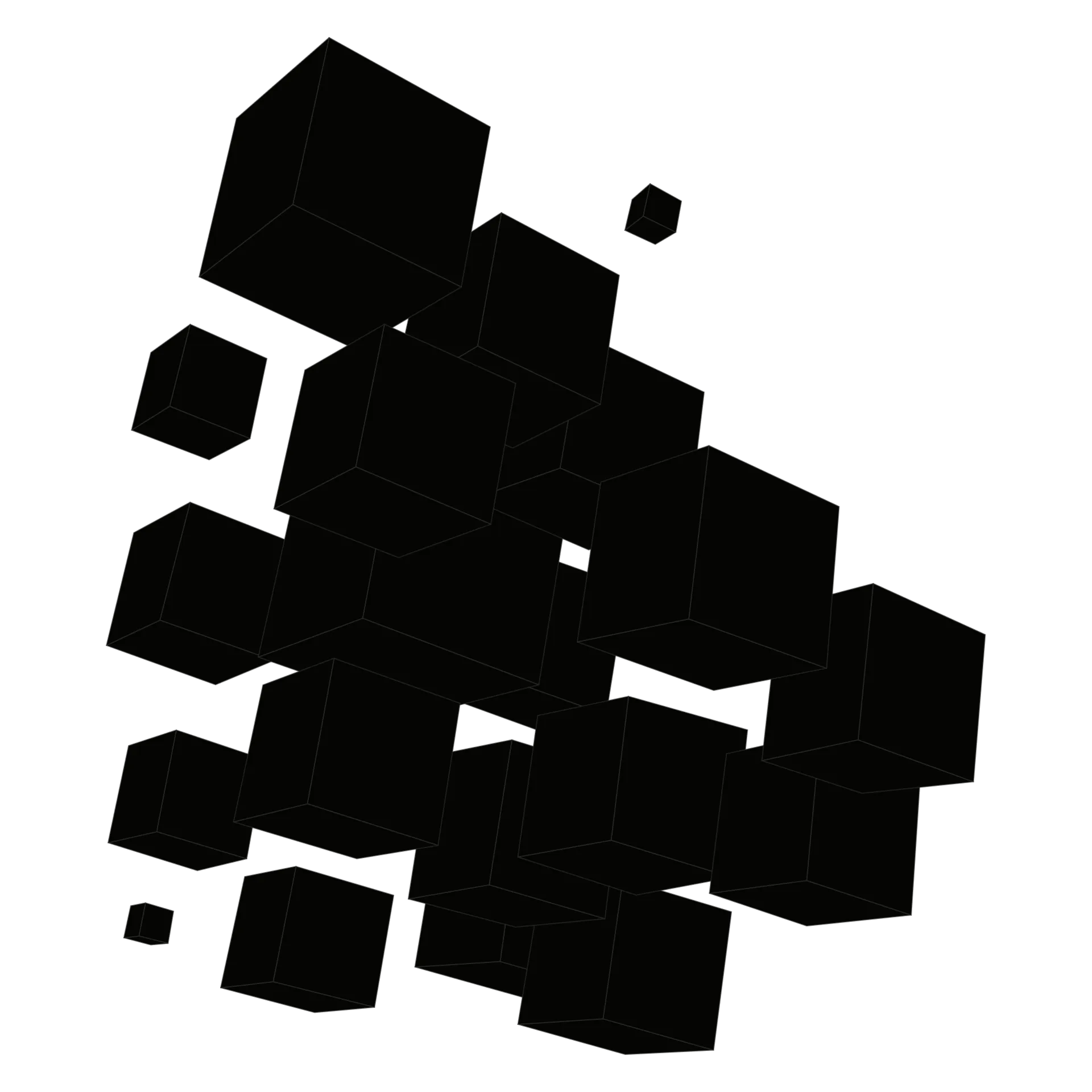
Business First
Code Next
Let’s talk
Manufacturing analytics system: key points to consider
The process of implementing data analytics in manufacturing is unique for each business. It mostly depends on project requirements, line configuration, and solutions implemented.
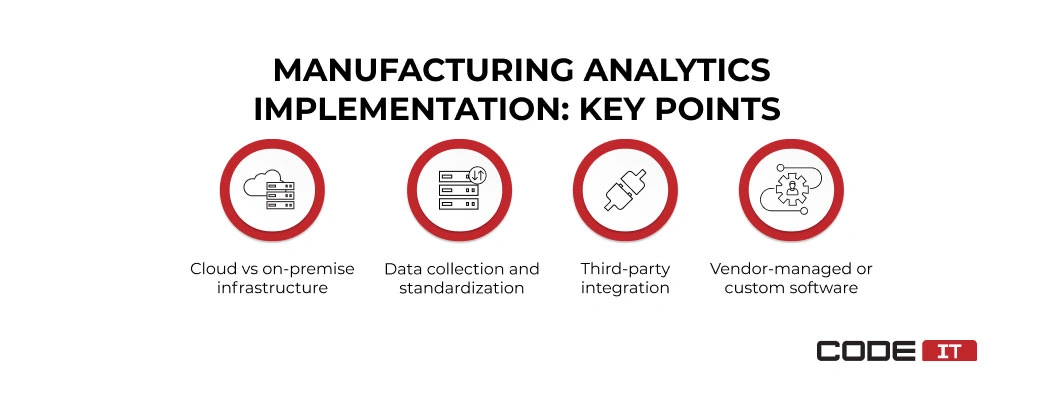
The four points stakeholders need to consider are as follows:
Cloud vs On-Premise Infrastructure
Cloud-based infrastructure comprises dedicated servers installed in a remote location. Cloud servers can only be accessed via the Internet and are managed by a third-party vendor.
The main strengths of cloud-based infrastructure are:
- Cost-effectiveness. Business owners don’t need to invest in hardware and in-house server maintenance, saving up to 75% of their IT budgets. They pay for the only computing power that has been used.
- Greater scalability. No additional hardware installation is required to increase the computing power or storage capacity. Cloud-based infrastructure can be easily scaled up and down by adjusting settings.
- Low tech skills requirements. The absence of in-house hardware minimizes the number of skilled specialists required to keep manufacturing analytics running.
- No initial setup costs. External vendors have already set up and configured servers. Hence, the cloud-based infrastructure can be easily configured remotely via the Internet.
On-premise infrastructure comprises servers that are physically installed in a shop floor and can be accessed offline, via a local network. All the hardware is fully managed and maintained by in-house tech specialists.
The main strengths of on-premise infrastructure are:
- Offline accessibility. On-premise infrastructure does not require an Internet connection to run data analytics in manufacturing.
- No data sharing. All the data collected by the shop floor machine is transferred via a local network. It is stored and processed by servers on a production site. No third-party vendors can access your production data and use it for improving software used for manufacturing analytics.
Data Collection and Standardization
Many connection standards are used to enable business analytics in the manufacturing industry. Moreover, machine manufacturers may implement custom software and data formats to lock in their clients.
Hence, defining data standards that manufacturing analytics solutions need to support is crucial. Otherwise, the lack of standardization forces manufacturers to develop additional middleware for transforming data.
Third-Party Integration
Connecting a large number of solutions from different vendors enables top-tier manufacturing data analytics. The selected/developed software needs to support API connectivity for connecting external solutions and implementing cross-system data-sharing pipelines.
Vendor-Managed or Custom Software
Using subscription-based software is an easy start. Pre-built solutions offer access to many tools for analytics in the manufacturing sector. However, they don’t offer the opportunity to customize a software solution or enrich its functionality by connecting third-party software.
The use of custom-built eliminates vendor lock-in. Moreover, it enables the development of software perfectly tailored to business needs. Perpetual licensing unlocks the opportunity to connect third-party software and customize the codebase upon need.
As per the build vs buy guide, the strengths and downsides of the two approaches are as follows.
Benefits | Drawbacks | |
---|---|---|
Out-of-Box | High customization Business-tailored 3rd party integrations Generate/update codebase Full software control | Extended development time Need for tech-savvy experts |
Custom-Built | Fast start Low initial implementation cost No maintenance and troubleshooting | Vendor lock-in No external software integrations No code editing Data is shared with a 3rd party |
C-Level insights: demand for advanced manufacturing analytics
The two foremost drivers of data analytics in manufacturing adoption are highlighted in the research and are the following.
1. Advanced Analytics is Rarely Applied
The researchers found that basic manufacturing business analytics is widely used. The most popular basic analytics activities comprised defect mapping and parameter change tracking.
Whereas, advanced manufacturing analytics technologies like big data and business intelligence (BI) are still rarely applied, despite the advantageous benefits they deliver.
The causes of the poor implementation of advanced analytics are:
- Lack of relevant and linked data. Even though large amounts of data are recorded, its relevance remains undefined. Stakeholders lack information on what parameters are included. Moreover, the collected data is usually poorly organized.
- Isolated solutions usage. Businesses collect data that is not linked. Hence, data analysis experts need to use cumbersome workflows. They need to import/export data, clean up values, and transform data, utilizing diverse software solutions independently.
- Lack of proper tools. Stakeholders highlight the lack of tools for efficiently handling large amounts of data. As per the feedback submitted by industry experts, the existing software solutions drop their performance drastically when the amount of data increases.
- Insufficient expertise. Technical and industry expertise is a requirement for manufacturing analytics. However, stakeholders report that on-site specialists usually lack expertise on how to handle/store large amounts of data and use industry-specific tools.
- Lack of motivation. Employees usually resist adopting new tools and technologies. Instead, they adhere to tried-and-tested manufacturing analytics methods. Skepticism and uncertainty about possible outcomes are one of the core issues that slow down the adoption of advanced analytics in the manufacturing industry.
2. Complex Problems Can Be Hardly Solved
Stakeholders report that traditional manufacturing analytics methods can hardly process ever-growing datasets. Hence, business owners experience issues with solving complex problems and discovering root causes quickly.
The causes of the insufficiency of current techniques are:
- Too many parameters and correlations. The amount of data collected is growing constantly. Therefore, the number of correlations increases correspondingly.
- Inability to identify root causes. Insufficient conventional data analytics manufacturing is useful for firefighting. The incapability to find the root causes keeps core product line issues unsolved, which can potentially lead to the development of more severe problems.
Future of manufacturing analytics
As per Gartner, business intelligence and analytics in manufacturing industry are the #1 trend. Moreover, stakeholders are constantly searching for solutions for effective management and storage of big data.
1. Advanced Technologies for Manufacturing Analytics
Conventional plug-and-use solutions cannot analyze large amounts of data and conduct complex manufacturing process data analytics. Hence, stakeholders widely adopt new technologies that help:
- deliver valuable insights
- identify root causes
- detect patterns
- forecast demand changes
“Fourth Industrial Revolution technologies are making data-powered ecosystems a reality in order to build applications such as demand forecasting, quality assurance intelligence, smart energy management, smart workforce management, etc.”
Haldun Dingec, Executive Director, Arçelik
2. Connected Manufacturing Environments
Many stakeholders report using isolated solutions for data analytics in manufacturing. Cross-system data pipelines and third-party integrations help implement connected solutions that collect data and process it in real-time.
“Data ecosystems are a huge advantage to operations excellence, whether inside our plants, across global supply chains, or at the level of our final customers.”
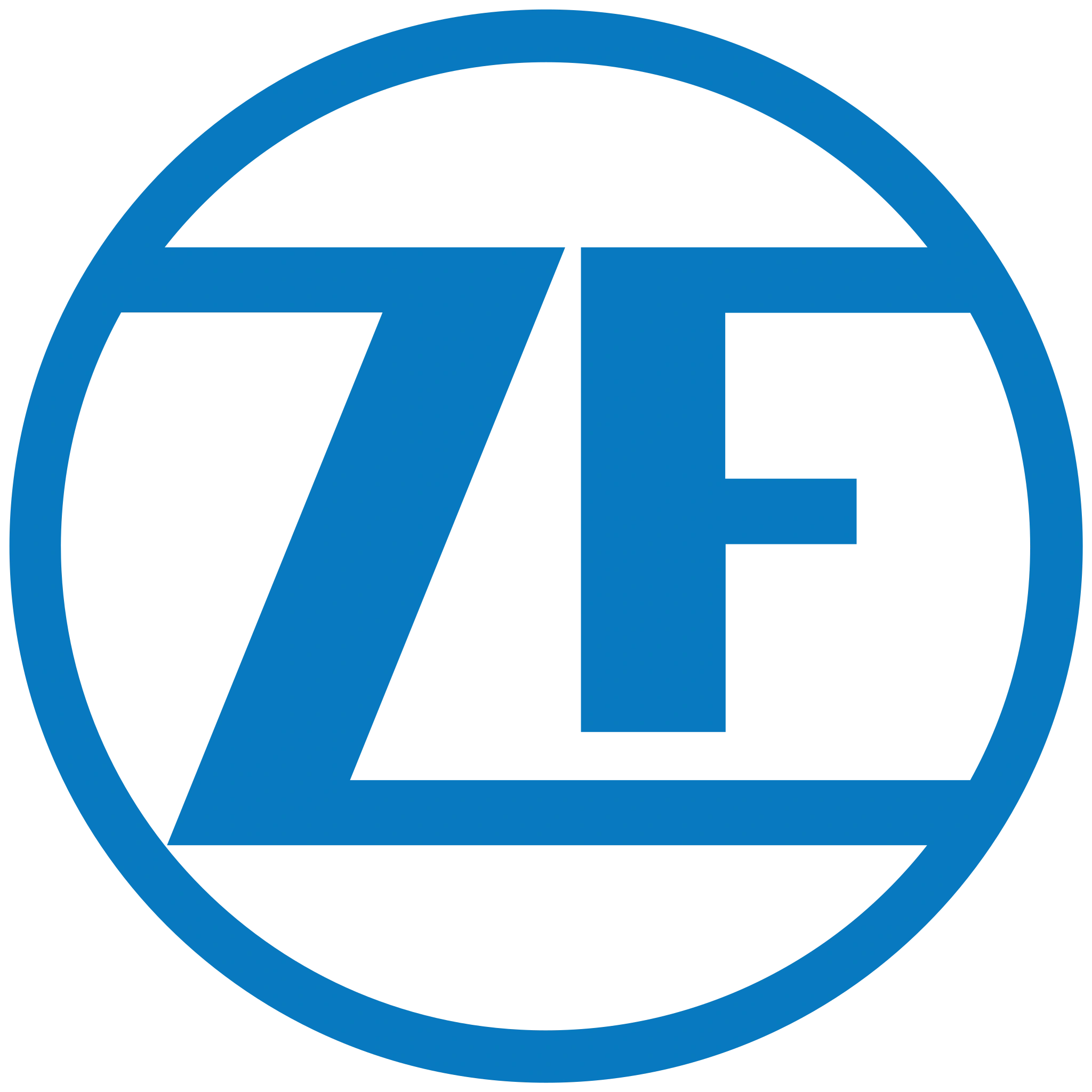
Gabriel Gonzalez, Senior Vice President, Corporate Production, ZF Group
3. Digital Twin for Process Optimization
The opportunity to create a genuine digital representation of a product line enables a cost-effective way to discover the most optimal configuration. Since simulations are run in a virtual environment, stakeholders can seamlessly run a large number of tests.
“Digital Twins offer various manufacturing advantages, including the simulation of production processes and supply chains for improved prediction as well as a more efficient approach to quality-by-design.”
Michelangelo Canzoneri, Global Head of Group Smart Manufacturing, Merck Group
Final words
Manufacturing data analytics involves using digital solutions to extract insights from shop floor data. A wide variety of software solutions are utilized to transform and analyze manufacturing data.
The top applications of analytics in the manufacturing sector include the following.
- Operational equipment efficiency control
- Item quality control
- Predictive maintenance
- Energy efficiency optimization
- Line configuration analysis
- Workflow optimization
- Manufacturing data analysis
- Automated reporting and alerts
- Demand forecasting
The top three real-world use cases of manufacturing analytics applications are:
- General Electric. Has achieved $70 million in customer savings by using data-driven insights.
- Ford Motor Company. Has achieved a 10% increase in production efficiency thanks to ML-driven data analysis.
- BMW. Has saved 100,000 kWh per year by using manufacturing analytics for energy consumption optimization.
Implement top-tier data analytics manufacturing
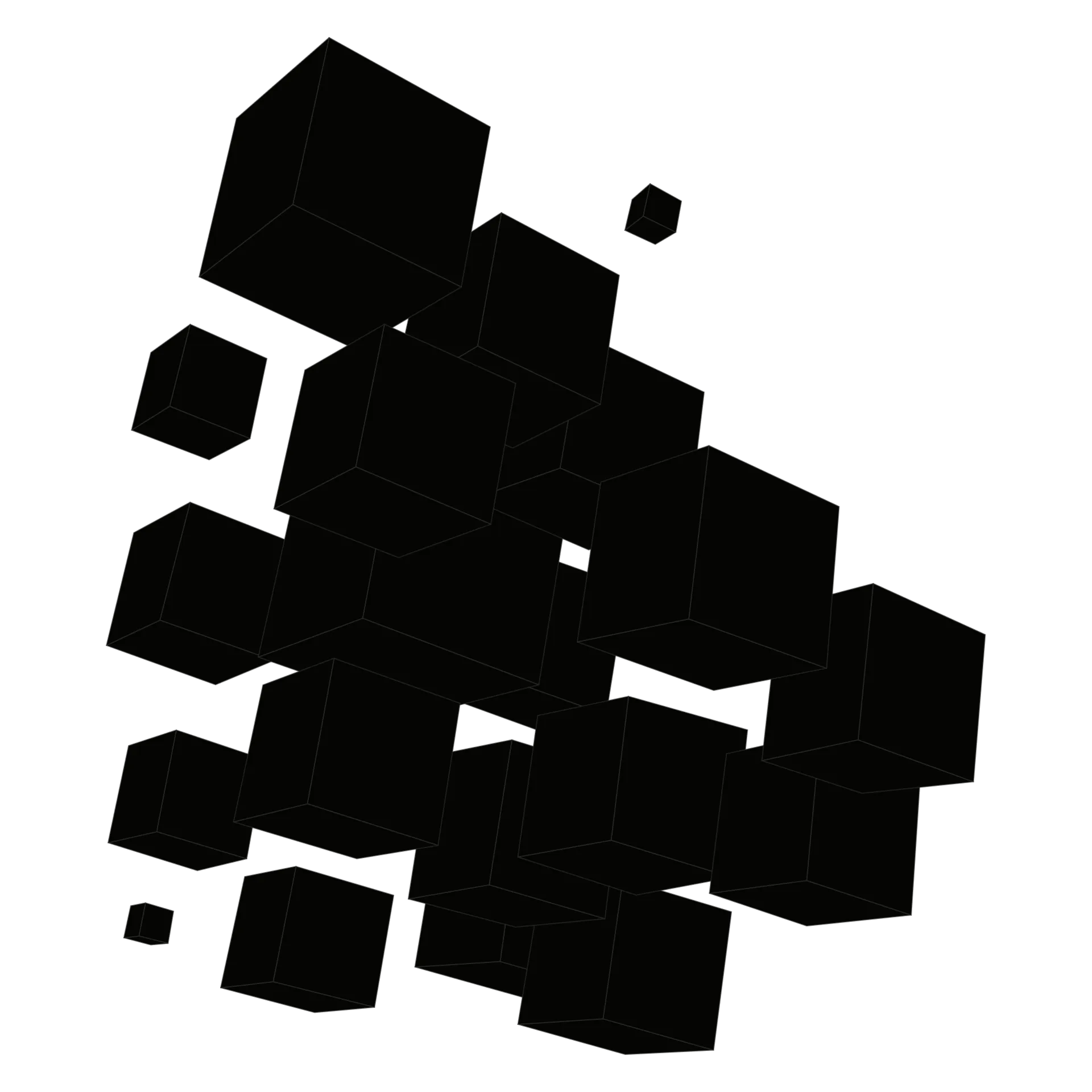
Business First
Code Next
Let’s talk
FAQ
Data analytics in manufacturing refers to the use of advanced technological solutions for analyzing large volumes of data collected from shop floor machines. Insights delivered by business intelligence software help optimize performance and cut operational costs.
Business analytics in the manufacturing industry is pre-processed and analyzed using algorithms to:
- visualize data
- summarize data
- discover insights
Moreover, stakeholders apply machine learning to:
- detect hidden patterns
- identify bottlenecks
- forecast trend changes
The insights delivered by custom manufacturing data analytics tools help address business-specific problems, including:
- inefficient production processes
- poor quality of finished items
- unforeseen machine downtime
- supply chain disruptions
- lack of shop floor visibility
The foremost manufacturing analytics challenges that stakeholders face are:
- lack of relevant and linked data
- usage of isolated solutions for manufacturing analytics
- insufficient tech expertise
- skepticism
- too many parameters
- inability to identify root causes
The major risks associated with not using data analytics in manufacturing include the following.
- Wasted data and insight-driven potential
- Core manufacturing issues remain unsolved because root causes are not identified
- Increased product development and inventory holding costs
Yes. Implementing manufacturing data analytics helps optimize workflows to achieve maximum efficiency. Furthermore, deep analysis of machine data is useful for cutting excessive energy consumption.
Build your ideal
software today
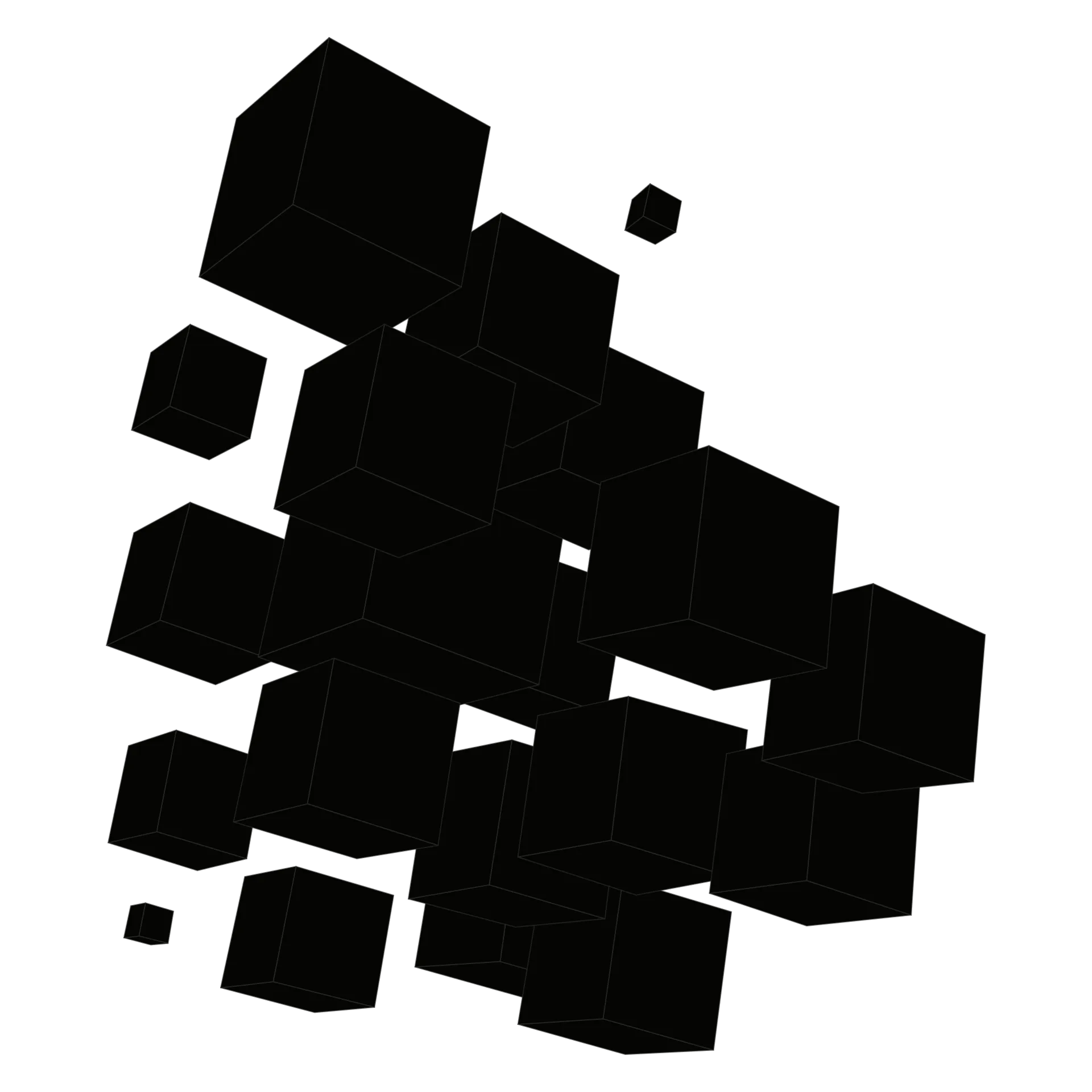